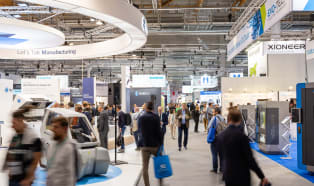
Formnext powers ahead at the start of the year and offers year-round content
Formnext has hit the ground running in 2023 with the highest number of registrations to date. By the end of February, more than 550 companies had signed up to attend the world's leading trade show for AM technologies and next-generation manufacturing; 62% of them from outside Germany.