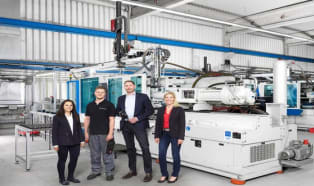
KraussMaffei offers APC plus, now also for thermosets
KraussMaffei has further advanced the proven APC plus (APC = Adaptive Process Control) machine function and also offers it for thermosets.
KraussMaffei has further advanced the proven APC plus (APC = Adaptive Process Control) machine function and also offers it for thermosets.
Chinaplas 2019, with the theme of “Innovation is Key to the Future”, is going to present a series of high-tech application solutions for that ever-evolving sector.
The Chemours Company today announced the startup of the new Opteon YF (HFO-1234yf) low global-warming-potential (GWP) refrigerant production facility at its Corpus Christi manufacturing plant in Ingleside, Texas.
Over a number of years, Windsor has retrofitted many an IMM from single-component to multi-component units offering most attractive economic solutions.
CHINAPLAS is returning to Guangzhou this year and will be held from May 21-24, 2019. An estimated total of over 3,500 exhibitors will be presenting to more than 180,000 visitors from 150 countries.
Vacuum laminating is key to success utilizing high automation to insure the best product quality at the lowest price level. Kiefel’s answer to high customer demand is the newly designed and developed "Tailored Blank Laminating" Technology and Machine.
Naberezhnye Chelny is the capital of machinery manufacturing of the Republic of Tatarstan. At a conference organized by R&P Polyplastic, the company not only presented the latest solutions for the auto industry but also discussed the fundamental trends of the industry.
Rondo Plast, a member of the Polykemi Group, is supporting Volvo Cars ambition to have at least 25% of the plastic in their cars being made from sustainable material by 2025. The Volvo Cars demonstrator vehicle that was revealed this summer exemplifies their commitment to this ambition, which is the most progressive by any premium automotive manufacturer.
More than 300 participants met at the two-day automotive conference trend.scaut 2018, which injection moulding machine manufacturer and systems expert Engel hosted in Shanghai at the end of October.
Glass and carbon fibre reinforced plastics are in demand when lightweight and forward-looking solutions are called for. This trend towards lightweight construction is currently one of the strongest drivers for the Composites industry.
In close cooperation, Workaround GmbH, Albis Plastic GmbH and BASF have modified an important component of the smart glove ProGlove.
Almost three years after its founding, Evosys Laser GmbH celebrates the successful move to new premises. In addition to the increase in the number of employees, expansion areas were leased in particular.