We are also seeing the rapid development of AI. This is particularly noticeable in the social sphere, although we often see side-effects of this development as well. But let's stay with our business. What is the role of AI for injection moulding processes?
It is not enough to simply collect data. You also have to have the process expertise and domain knowledge. Arburg started thinking about neural networks for process optimisation more than 20 years ago. The advantage is that we can base our AI ideas on the Gestica control system we developed ourselves, the Arburg host computer system, and our own arburgXworld customer portal.
Particularly in the areas of AI and machine learning, we still see great potential for machine operation. In future, an injection moulding machine must also be able to automatically process 'difficult' materials such as recyclates in a way that produces quality parts without putting more strain on the operator. One issue for the future is to ensure that the machine not only keeps itself stable, but also optimises itself. A typical case of application is that, in the event of a malfunction, for example, the control system records the actions of the operators, compares them with each other, and uses them to determine the best course of action to provide targeted support if there is another malfunction. So the system learns continuously by means of 'machine learning' and gets better and better over time. Another example is the automatic programming of robotic systems. In future, the operator will only have to enter the desired start and end positions – the control system will take care of the rest by automatically determining the optimum operational sequence.
The big challenge in injection moulding is that AI models are highly dependent on the respective process, material, and equipment. Arburg is working on developing original models for various process types, materials, and machine equipment and making these available to our customers. They can then refine their model 'at the edge' – for example in the laboratory – and make a rollout, e.g. via our arburgXworld customer portal or our host computer system ALS, for machines distributed at different locations worldwide. From an extract of optimised models from different customers, we could then create the next generation of an original model.
Another very practical potential field of application for AI is the improvement of spare parts management by means of 'intelligent' image processing. The plastics processor could photograph an oil filter in need of replacement, for example. If the picture were linked to arburgXworld, the processor could automatically receive an order suggestion, plus other products that go with the spare part - in a way that would be familiar from Amazon.
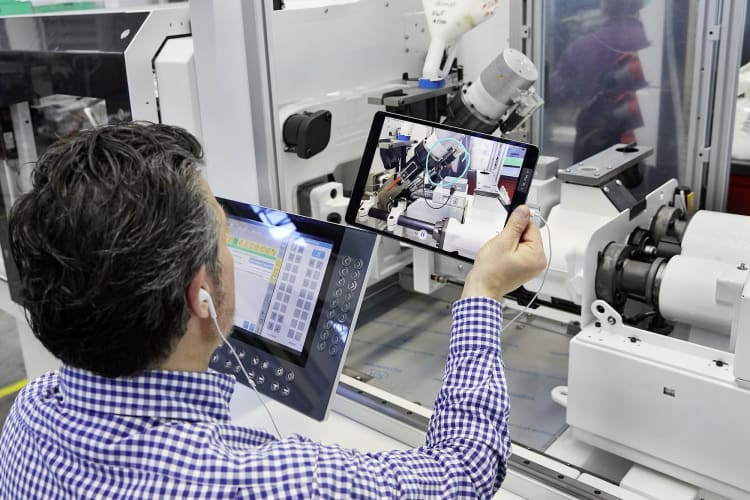
Finally, I would ask you to play the role of a visionary. What will the injection moulding technology sector look like in 20 to 30 years?
My vision is that, thanks to their smart assistance functions, 'intelligent' machines will make injection moulding as easy and convenient as autonomous driving makes it to get from A to B. There could also be fewer types of plastic in the future. Instead, a few basic materials will be modified directly on the injection moulding machine as required. In order to modify these materials with appropriate additives for achieving the desired properties, one can imagine progress towards the smallest, most complex extrusion-injection moulding combinations with compounder functionality. This is also of interest as regards the topic of the circular economy in the short to medium term. In the future, I would also like to be able to 'cultivate' modern plastics that break down into biologically harmless components through simple chemical or physical effects when they are disposed of.
There will probably be a smooth transition between additive manufacturing and injection moulding in the future. Freeformers and other 3D printers will produce ever higher quality plastic parts ever faster and injection moulding production will become increasingly flexible. Looking into my glass ball for Arburg, I see even more standardised clamping units that will be coupled with various 'injection modules' in a very versatile way in the future. So-called 'memory' metals are conceivable for demoulding. However, the central question is how in general we are going to deal with the issues of circular economy, energy, carbon emissions, and resources in the coming decades. That depends very much on whether we humans want to remain on this Earth. If so, then we must also do everything we can to preserve it.