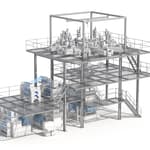
Reifenhäuser has three line technologies for barrier films: cast film, air-cooled blown film and water-cooled blown film. At K 2025, the extrusion specialist will be presenting its new developments, which offer higher performance and top quality at lower production costs.
Barrier films are used in a wide variety of packaging types - especially in the food, medical and hygiene industries. The desired barrier properties are achieved through a precise multilayer structure of the film and the use of special materials. The trick is to achieve a high throughput with stable quality despite complex multi-layer processes and to reduce expensive barrier raw materials, such as EVOH, to a minimum. Thanks to the three system technologies in this application area, Reifenhäuser is one of the few suppliers on the market that can advise producers on all technologies - depending on product requirements or production volumes.
Marcel Perrevort, CSO of the Reifenhäuser Group, says: "With our systems, producers are already achieving the highest throughputs with optimum quality and barrier properties. We will continue to expand this leading competitive position with our developments and introduce clever features that bring our customers measurable added value."
New edge encapsulation for cast lines saves up to 150,000 euros per year
Cast film systems are the ideal technology for high production volumes of barrier films. They also have a technical advantage. In flat film production, encapsulating the barrier layer prevents expensive barrier raw materials from reaching the edges of the film, which are cut off before winding. The edge trim can then be immediately fed back into the production process. The result: the film edges consist only of the more cost-effective raw material - producers can save up to 150,000 euros per year on average. Reifenhäuser is presenting a particularly elegant solution for this at K 2025, in which the encapsulation of the barrier layer is not carried out at the die, but already in the coextrusion adapter. This eliminates the investment and operating costs for an additional extruder, which is necessary with other solutions. The solution also speeds up the start-up process, as there is no need to set up the encapsulation extruder.
For further efficiency gains, Reifenhäuser cast lines can be automated on request with the proven PAM option (precise, autonomous, mechatronic). The patented system controls the coextrusion adapter and die via mechatronic actuators and carries out product changeovers fully automatically. Reifenhäuser is presenting a new generation of the solution at K, which will significantly increase the level of automation even further thanks to new features. Producers will thus become independent of the shortage of skilled workers and save energy as well as raw materials at the same time.
Extra powerful cooling for up to 1,000 kg/h throughput for barrier blown film
Due to their principle, blown films are suitable for smaller production volumes and, in addition to lower investment costs, offer specific advantages such as outstanding individual layer distribution. With the new developments, Reifenhäuser is significantly increasing throughput - for both PA and EVOH barrier films - from 800 to up to 1,000 kg/h, for example, with a film width of 2,600 mm. The 25 percent increase, which offers producers an enormous productivity advantage, is due in part to a new generation of cooling systems. Precise sensor technology and temperature regulation ensure bubble stability and the highest film quality at all times.
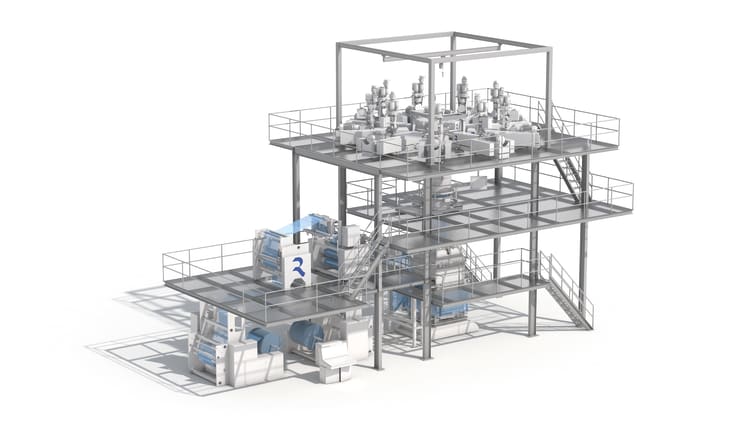
Water cooling for special film properties
For barrier applications with special requirements in terms of puncture resistance, transparency or thermoformability, it is important to keep the crystallinity of the film as low as possible. Reifenhäuser offers a special process for this: EVO Aqua Cool blown film lines. The shock-like water cooling cools the plastic melt extremely quickly, which inhibits or even stops crystallization. EVO Aqua Cool is particularly suitable for customers who require a slightly thicker film, but still attach great importance to transparency, because the thicker the film, the clearer the advantages that result from the rapid cooling of the film. Thermoforming films, lidding films, vacuum skin packaging or vacuum bag packaging are typical products in which EVO Aqua Cool shows its strengths.
"Regardless of the barrier application in which our customers operate, we have a comprehensive technology portfolio that is designed to achieve the optimum balance between maximum performance and quality. At K 2025, we will be demonstrating the specific advantages and advising on the optimum customer solution," says Marcel Perrevort.