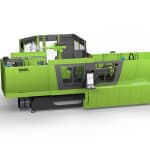
At K 2025, ENGEL will demonstrate how technological innovation, digital intelligence and sustainability can be effectively combined. The trade fair presentation focuses on industry-specific injection moulding solutions that enable companies to manufacture more efficiently, precisely and flexibly. ENGEL will showcase its technologies and solutions in practical operation - from the use of artificial intelligence in the running injection moulding process to highly integrated production cells for the automotive, medical, technical moulding and packaging sectors. Visitors are invited to gain a comprehensive overview of future-proof applications at ENGEL’s stand in Düsseldorf - and to witness the world premiere of a new electric tie-bar-less injection moulding machine.
Automotive: Efficient mastery of function, lightweight design and new materials
Where design meets function: rear-end-light modules with clearmelt and foilmelt without hardcoating
ENGEL is demonstrating the highly integrated series production of innovative rear-end-lights on a high-performance duo 700 two-platen injection moulding machine with 7000 kN clamping force. The visible parts, measuring 600 x 240 mm, are manufactured using a combination of decorative foilmelt and functional clearmelt technologies in a vertical rotary table mould. In addition to design freedom, downstream processes are integrated into the injection moulding cell, and a separate hardcoating process is no longer required thanks to clearmelt. While the transfer the colour design from a decorative foil is applied to the component on one mould side by back-injection of thermoplastics (foilmelt), the opposite side is overflooded with polyurethane (clearmelt) to form a highly transparent and robust protective layer. A space-saving integrated automation system with a viper 40 linear robot enables short cycle times within a compact and efficient cell. The transfer foil is supplied by Leonhard Kuraz. At the partner’s stand, the component is further processed using an integrated LED function foil.
With this application, ENGEL demonstrates how visible parts in the automotive sector can be both functionalised and decorated - economically, with high precision, and in a compact production process.
Overmoulding with liquid silicone: precision seals for fuel cells
A production cell with a vertical insert 150 injection moulding machine, offering 1500 kN clamping force, demonstrates the fully automated manufacturing of liquid silicone rubber (LSR) seals on sensitive gas diffusion layers (GDL) for fuel cells. The LSR seal is applied with absolute platen parallelism directly in the machine, inspected in the mould and the component is immediately removed. The automation system, featuring ENGEL easix articulated robot and a rotary table mould supplied by ACH, ensures short cycle times and high process reliability. To save space, the control cabinet is integrated directly into the machine frame. ENGEL is showcasing a highly cost-efficient solution for fully automated overmoulding with thin LSR layers in a compact footprint.
Lightweight, strong, sustainable: bicycle handlebars with fluidmelt and organomelt
A novel bicycle handlebar is manufactured as a hollow component on a tie-bar-less ENGEL victory 180 injection moulding machine with 1800 kN clamping force. The fluidmelt process is used to create the hollow structure, while unidirectional continuous carbon fibre tapes are simultaneously integrated using the organomelt process. This innovative combination of technologies enables maximum part performance with minimal weight and a short cycle time of just one minute. The process is fully automated with an easix articulated robot. With these technologies, ENGEL once again sets new benchmarks in production efficiency and sustainability - opening up new markets for plastic components in applications traditionally dominated by metal.
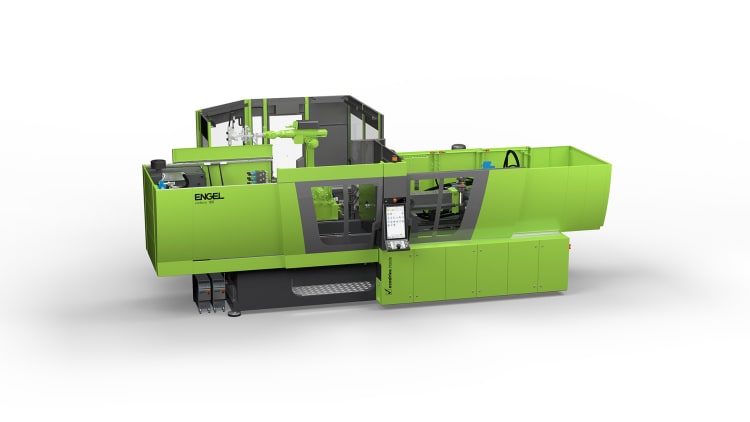
Cost-efficient and ready for series production: Physically foamed B-pillar trim using MuCell
A B-pillar trim component is produced in just 50 seconds using the ENGEL foammelt technology on a t-win 6500 two-platen injection moulding machine from the Wintec brand, part of the ENGEL Group. The foamed part, weighing 290 g, is made of mineral-filled PP from Sabic. ENGEL’s foammelt technology reduces weight and cuts material and production costs while achieving excellent surface replication. Automation is handled by a highly integrated viper 20 robot. Wintec here demonstrates a cost-effective solution for producing visible interior automotive components.
High-precision manufacturing for medical products: Cell culture plates with accelerated validation
In the Medical area, ENGEL showcases a highly efficient injection moulding cell built around an all-electric e-motion 260 combi M injection moulding machine equipped with two injection units and a central rotary platen. Using a stack mould from Hack, 24-well cell culture plates and matching polycarbonate lids are produced simultaneously in a single shot - with a cycle time of just 11 seconds. The additional injection unit is arranged at an angle to shorten the hot runner path, enable central injection without weld lines and improve material protection. This manufacturing solution, featuring a side-entry robot from Ilsemann, delivers the entire process including assembly and packaging in a compact, ergonomic setup.
A key highlight is the validation solution jointly developed by ENGEL and toolmaker Hack. This system enables structured and digital documentation of all validation phases - from Design Qualification (DQ) to Performance Qualification (PQ). Machine - and tool-integrated sensor technology, combined with products from the ENGEL iQ family and standardised documentation modules, significantly reduce the effort required. As a result, the time- and personnel-intensive validation process is substantially shortened.