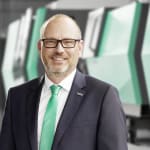
As part of our "Future of Injection Molding" series, we talk to Guido Frohnhaus, Managing Director Technology & Engineering at ARBURG
The rapid development of digital technologies has thrown the door wide open to the 'Industry 4.0' era. What impact does digitalisation have on the injection moulding machine industry and how has it changed the approach to injection moulding processes?
As a pioneer in the industry, Arburg is working hard and with a practical focus to find ways of using digitalisation to further increase production efficiency in plastics processing. With high-quality technology, a 'smart' control system and digital products and services, even difficult processes can be optimised and kept stable. What was previously associated with considerable time, staffing and control outlay is now becoming increasingly simple, efficient and reliable in terms of processes. This is precisely what plastics processors expect from us machine manufacturers - to use digitalisation and automation to make everyday work in injection moulding easier and more profitable.
There is a demand for extensively interlinked 'smart' injection moulding machines that know the parts they are producing, monitor their processes, control them adaptively, and actively support the operator in every situation. This also includes assistant-supported operation and seamless documentation. The data collected provides a great deal of information about the manufacturing process and enables users to organise their own sequences more quickly and with greater added value, and also to inform customers about the status and quality of individual orders, for example.
The Arburg host computer system, or 'ALS', our own MES specially developed for injection moulding, makes this possible. Besides Allrounders, injection moulding machines from other manufacturers and metalworking machines and peripheral devices, for example, can also be connected with this tool.
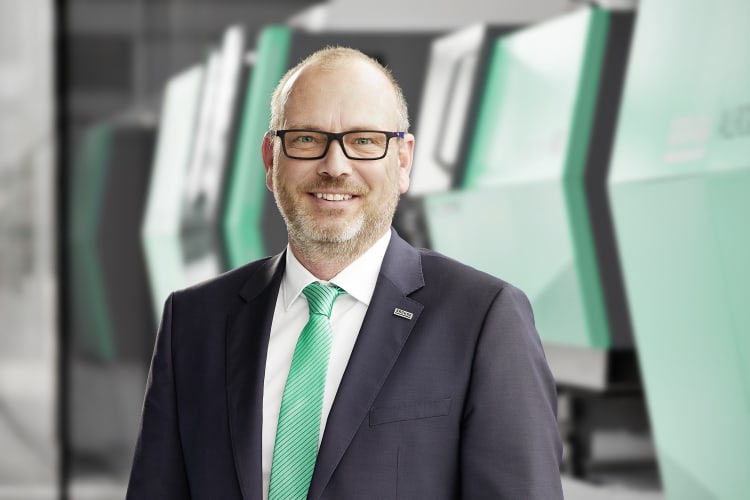
Guido Frohnhaus, Managing Director Technology & Engineering at ARBURG
Last but not least, digitalisation is essential for a functioning circular economy and hence for the sustainable and resource-efficient use of plastic as a recyclable material. Arburg is involved in this area as part of "R-Cycle", for example, a cross-industry initiative for plastics recycling. This has been nominated for the German Innovation Award for Climate and Environment (IKU) 2022 in the category "Use of digital transition for climate and environmentally friendly innovations". The aim is to use a digital product passport to automatically record properties relevant to recycling during production so that recyclable packaging can be identified and separated by type in waste sorting plants and then used to produce high-quality recyclates.
But these are still the beginnings of advanced digitalisation and, generally speaking, the level of maturity in terms of the digitalisation of injection moulding processes still varies widely.
Mechanical engineering is following the same development path as the automotive industry - software and 'smart' technologies are also becoming increasingly important in plastics processing. But we are only at the beginning of a new era here. Together with our customers and partners, we are embarking on a journey towards digital transformation. However, because digitisation has progressed differently in different countries, industries, and companies, we want to meet everyone exactly where they are at the moment. Our aim is to be at our customers' sides to offer advice and assistance, and in so doing create 'connectivity', so to speak, between them, our machines and Arburg.