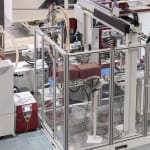
From 23 to 26 May, Wittmann Battenfeld Polska will present to interested trade visitors ultra-modern injection molding machines and process technology, as well as state-of-the-art robots and auxiliaries at the Plastpol 2023 in hall F, booth No. F-9.
The Polish market is one of the most important export markets for the Wittmann Group. Consequently, the Plastpol is a key platform for Wittmann to present latest technologies to this market in cooperation with its subsidiary Wittmann Battenfeld Polska.
At this year’s Plastpol, two servo-hydraulic injection molding machines will be shown.
On a SmartPlus 90/350 equipped with the new control unit B8X as well as the CMS Lite conditioning monitoring system and an automation cell designed and manufactured by Wittmann Battenfeld Germany, Wittmann produces a spirit level made of ABS with a 1+1-cavity mold supplied by Sola, Austria. As a first production step, the top and bottom parts of the spirit level housing are injection molded. The top part is then deposited and printed at a laser station. Simultaneously, the bottom part placed on a tray is fitted with vials from Sola. Next, the top part is pressed onto the bottom part by a pre-set force. The finished parts are then transported to a testing station, where the positioning of the vials is checked by a vision system. After quality inspection, the finished spirit levels are removed and deposited on a conveyor belt by a WX138 robot from Wittmann.
Special features of the SmartPlus are high levels of cost and energy efficiency and repeatability. By using proven technologies combined with carefully selected options, it has become possible to offer an excellent price/performance ratio for these machines.
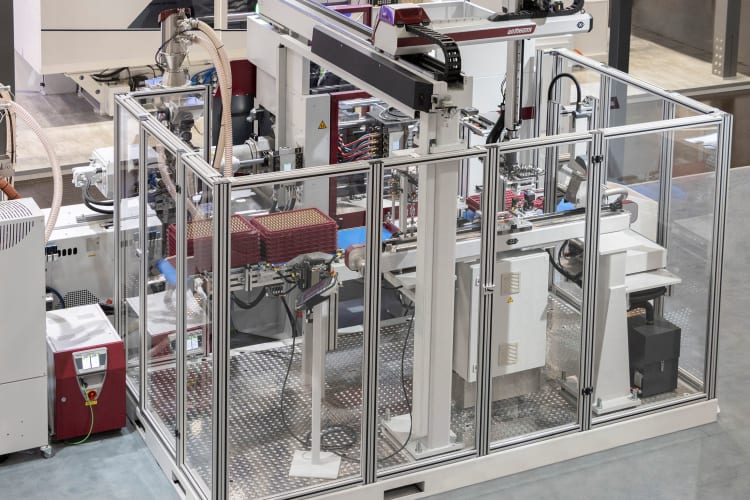
SmartPlus 90 with complex automation and digitization via Wittmann 4.0
The second machine is a SmartPower 60/210. This machine comes with Airmould internal gas pressure technology. Using this technology, a clothes peg will be manufactured with a 1+1 cavity mold. In the Airmould process, nitrogen is injected into the cavity partly or completely filled with melt by an Airmould nozzle specially developed for this purpose, which leads to the formation of a bubble structure. In this way, substantial quantities of material can be saved, with the result of a significant cost advantage especially for mass products such as clothes pegs. In this application, the latest-generation Airmould technology, known as Airmould 4.0, will be demonstrated. It stands out by its compact hardware, plus a high level of user friendliness through its integration in the Unilog B8 control system. All components were developed and are produced in-house by Wittmann Battenfeld.
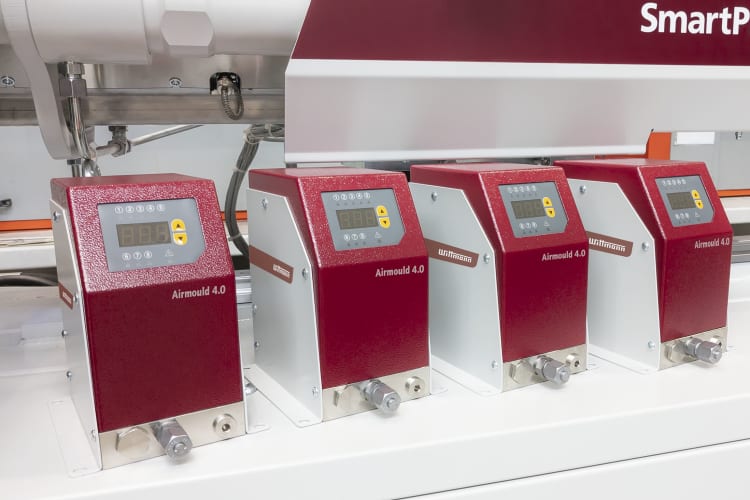
Airmould 4.0