Process control at the push of a button
The operator initially optimises the process settings as usual so that the required quality of the good part is achieved. This reference is transferred to the pilot function via a control command. An additional command activates RecyclatePilot, which then analyses the injection behaviour, detects distinctive points and deviations in the injection process and ensures that the injected volume and therefore the mould filling remain constant. This is done by comparing the event pattern in the same cycle with the reference entered during the injection phase and, if necessary, adjusting the switch-over point at short notice. In addition, correcting the dosage volume also makes the overall process more stable in the long term and across cycles.
Case study: Comb
Varying material characteristics and viscosities in the injection moulding process are particularly evident during sprueless production with no holding pressure. This results in varying degrees of incomplete mould filling, as the "hair comb" example shows. The part was injection moulded from PA6 in three material variants - virgin material, recyclate in the form of granules, and reground material. The extent of the mould filling can be seen from the part weight:
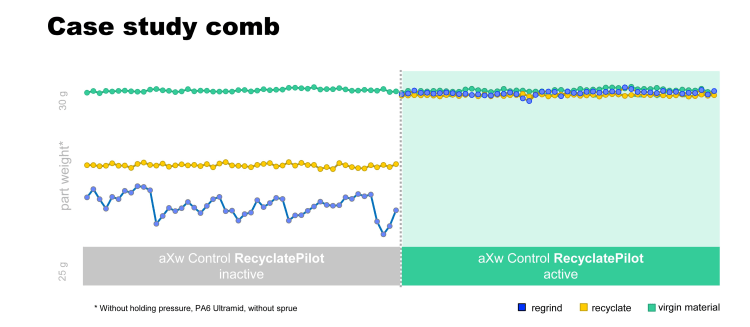
- The comb made of virgin material was not fully formed in the mould because it was deliberately produced without holding pressure and served as a reference.
- With the moulded part made from granules of recyclate, the weight remained constant but was significantly lower than that of the virgin material.
- With the reground material, significant variations in the part weight were also observed.
This changed virtually at the push of a button with active control using RecyclatePilot. Now the part weight was constant and almost the same for all three variants. With this case study, Arburg has shown that the digital pilot function can balance out the resulting variations in mould filling, thereby significantly increasing both process reliability and part quality. This significant improvement in mould filling also results in a high level of mould reliability.
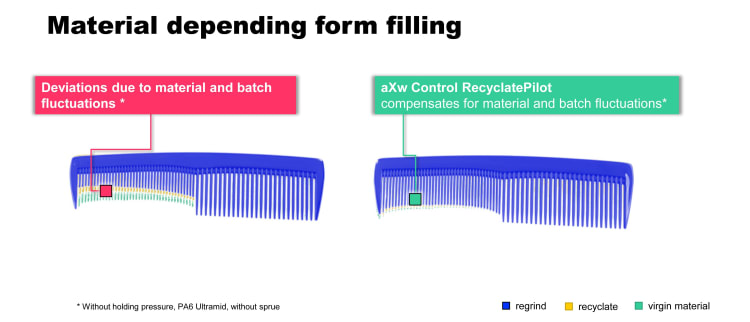
Conclusion
The controller is the "brain" of an injection moulding machine and can provide operators with comprehensive and active support. With the help of digital pilot functions such as RecyclatePilot and ReferencePilot, process reliability can be significantly increased during the processing of recyclates by means of active control in the injection and holding pressure phases. The injection profile and filling process of the moulded part remain stable and correspond to the specified reference.
Of course, it is not possible to overcome the inadequate material characteristics of recyclates across the board, meaning that there are limits to how much part quality can be improved. Knowledge and experience on the part of the user are still crucial to determining which concept will deliver good results for which process. In future, overarching, AI-supported methods could provide additional assistance here.
Author: Dr Thomas Walther, Director Process Development at Arburg