ScrewPilot: Control concept for the "fill mould" core process
Filling the mould cavity in a reproducible manner from cycle to cycle is the basis for consistent component quality. A successful control concept for this is the "aXw Control ScrewPilot" or "position-regulated screw" pilot function, where the filling process is adapted to the requirements of the flow path in several stages by a speed-regulated screw movement. This concept can be compared to a driving assistant for cars: if the movement (in this case of the screw) deviates from the programmed speed due to disruptive influences (here, for example, variations in the viscosity of the plastic melt), it is regulated in a way that ensures that the distance is still covered in the allotted time. The active acceleration and braking dynamically compensates for disruptive influences, so that a constant amount of melt is fed into the cavity. These dynamics have proven to be particularly useful at high injection volume flows, especially when it comes to preventing pressure peaks and overfilling by targeted and rapid braking.
ReferencePilot: Control in the holding pressure phase
The holding pressure phase is also crucial for part quality. It is usually executed as a quasi-static, pressure-controlled process, with the optimum parameters previously determined by a machine setup technician. No account is taken of short-term influences during ongoing production, such as viscosity variations in the melt (caused by recyclates, lubricants or colour additives), or long-term wear, e.g. on the non-return valve and other mechanical components. In the long term, this can lead to variations in the cavity pressure and hence to irregular part quality.
For this reason, as early as 1988, Arburg developed an injection process regulation function that is integrated in the controller and regulates the holding pressure curve in real time via a pressure sensor in the mould. This software function has been continuously developed and is now known as "aXw Control ReferencePilot". The ReferencePilot uses the nominal value reference curve of a good part as the basis for active regulation in the holding pressure phase, where the current holding pressure is adjusted according to the internal pressure. A pressure sensor positioned as close as possible to the sprue in the mould is required as the associated hardware. The way it works is comparable to autonomous driving: even with GPS and a known route, a vehicle still needs additional active sensors to be able to move safely in road traffic. This is the only way to detect unforeseen bumps, road works or other road users, for example.
Mould cavity pressure as an influencing factor
So that it can quickly counteract disruptive influences and actively balance out pressure variations, the software receives signals regarding mould cavity pressure that are recorded in real time by the sensor. This enables ReferencePilot to regulate the internal pressure curve from the current actual value to the desired nominal value. When ReferencePilot is used for control, the pressure conditions in the mould are precisely adjusted from shot to shot to match the reference, with the actual value being raised to the nominal value. This results in a constant shot weight and consistently high part quality, without the need for manual intervention during process parameterisation.
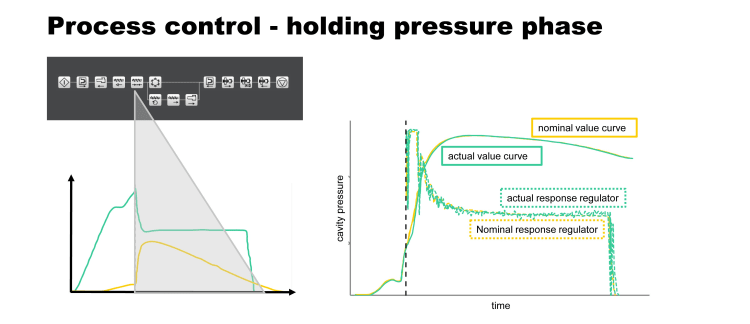
Calibrated pressure sensor required
To be able to use ReferencePilot, two conditions must be met:
- The injection moulding machine must be equipped with "aXw ScrewPilot", which is standard for electric and hybrid Allrounders.
- There must be enough space in the mould cavity to install a pressure sensor.
The sensor itself causes additional expense; in addition, expertise and time are required to recalibrate it for each setup process and to maintain it regularly. This is the only way to ensure that the internal pressure sensor measuring equipment is fully functional and delivers the correct signals.
If all requirements are met, the injection moulding process can be stabilised quickly and reliably through the interaction of the sensor and the pilot function. The number of start-up cycles can be greatly reduced and there is less scrap. The results are longer, trouble-free production times, fewer downstream testing processes and increased production efficiency. Depending on the case of application, investing in a sensor system can quickly pay off.
RecyclatePilot: Control in the injection phase
An alternative is the new "aXw Control RecyclatePilot" function, which controls the injection moulding process directly in the injection or mould filling phase based solely on data from the standard machine sensor system. Compared to ReferencePilot, which receives signals directly from the cavity, the RecyclatePilot has a longer partial control circuit. Nevertheless, it offers a number of clear advantages:
- There is no need for additional sensors.
- The pilot function integrated into the controller can be activated simply by pressing a button.
- The function uses the proven sensor system inside the machine, which only needs to be calibrated every few years.
- This pilot function balances out short-term variations from shot to shot and also across cycles.
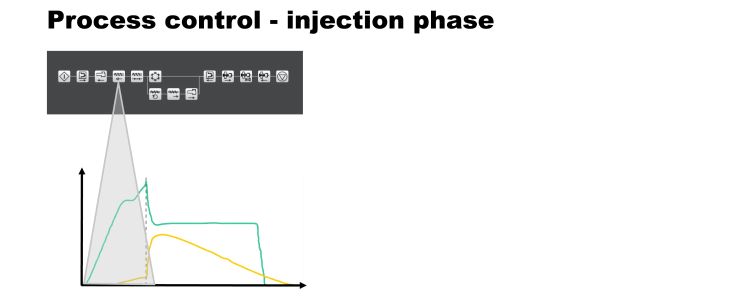