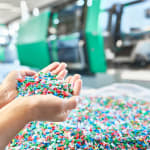
Reproducibly manufacturing moulded parts out of virgin material from shot to shot and batch to batch at a consistently high part quality is state of the art, but usually places high demands on the controller technology. When it comes to processing content such as post-industrial recyclate (PIR), post-consumer recyclate (PCR) and bioplastics, the material and processing properties can vary considerably. Control concepts that ensure constant mould filling and, ultimately, consistent quality of the end products are therefore required if recyclates are to be used efficiently. For this task, Arburg has developed digital pilot functions for its machine controllers that keep the injection moulding process stable during the injection and holding pressure phase.
Various committees, movements and initiatives are pushing for the establishment of closed-loop recycling systems. Even if this is not yet economically viable, the goal is to significantly reduce the use of fossil resources in the medium and long term. In this context, recyclate processing is becoming increasingly important. However, the growing range of materials, their different origins and preparation, as well as their non-homogeneous processing behaviour, make this challenging. The same can also apply to batch to batch variations with virgin material or inadequately prepared granules, for example due to uneven or insufficient drying of the material.
From a chemical perspective, recyclates are plastics just like conventional virgin materials, with the difference that they have already been finished products that have had a period of use and have then been reprocessed. However, there are still many unanswered questions as to whether and how recyclates can be used as effectively and reliably as virgin materials. Injection moulding processors have to face a new set of challenges here.
"Black boxes" challenge
From the machine's point of view, injection moulding involves two large "black boxes" that significantly influence process stability and part quality. This is because the machine itself has no knowledge of
- which material is fed into the hopper, or
- what happens between the two mould mounting platens.
These are two major challenges when it comes to reliably controlling process parameters such as the temperature progression of the moulding compound and the temperature progression and pressure profile in the mould. The biggest difference between processing recyclates and virgin material is that the material properties and characteristics such as mechanical quality, colour and smell can vary within a delivery or an order over a wider range. Since no clear material specification can currently be assigned to the recycled granules in most recycling processes, no data sheet is available during machine setup, which makes processing significantly more difficult.
However, the Gestica and Selogica controllers for Allrounder injection moulding machines have pilot functions, for example, that counteract fluctuating viscosities in the melt: "aXw Control ReferencePilot" and "aXw Control RecyclatePilot" can detect and reliably even out irregularities and actively control the ongoing injection process in order to keep the mould filling as constant as possible and ensure consistent part quality despite major variations.
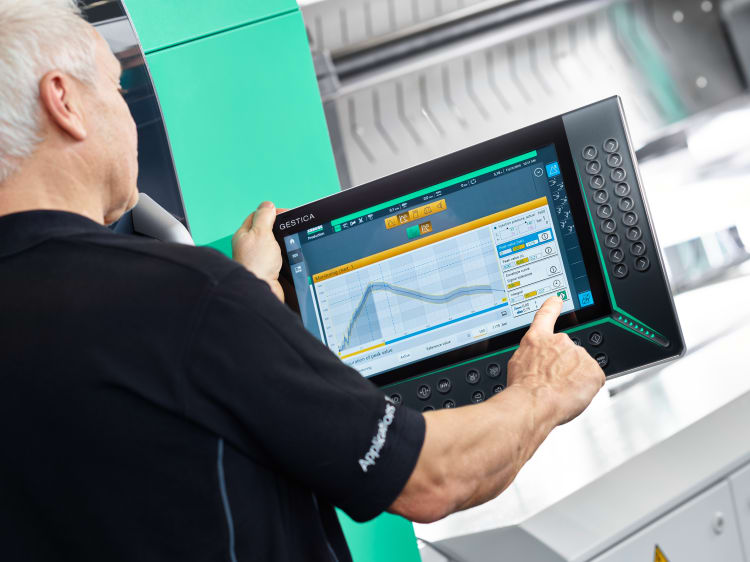
Melting process as an influencing factor
A homogeneous and stable melting process is an important influencing factor in the production of good parts. It starts with the material being fed into the plasticising screw as evenly as possible. The shape and quality of the recyclate play an important role here. If the material is in the form of granules, recycled plastic can generally be processed as well as virgin material without the need for additional hardware. The situation is different for flakes and reground material. Flakes can vary greatly in size and shape. Reground material, on the other hand, which is material from plastic parts that have only been shredded with a sprue grinder, consists of fragments of different sizes, ideally in grain sizes of two to five millimetres. These grains are usually accompanied by finer material, up to and including dust-like material. To ensure a stable melting process, any dust must be removed from the reground material.
Recyclate package for reground material and flakes
For the processing of reground materials and flakes, Arburg offers a retrofittable recyclate package that combines software and hardware features. Among the software features are multi-stage start-up parameters and the digital "aXw Control ScrewPilot" assistance function, which ensures precise and stable mould filling. In terms of hardware equipment, a modified cylinder module enables uninterrupted feeding even of poorly flowing materials. A plasticising screw with a modified, deeper high-compression (HC) geometry ensures homogeneous processing. Grooves in the feed zone help the material to be drawn in, despite its irregular shape, and conveyed forward in a stable manner. The screw also has a CrN coating to reduce the formation of deposits and wear caused by unexpected foreign bodies.
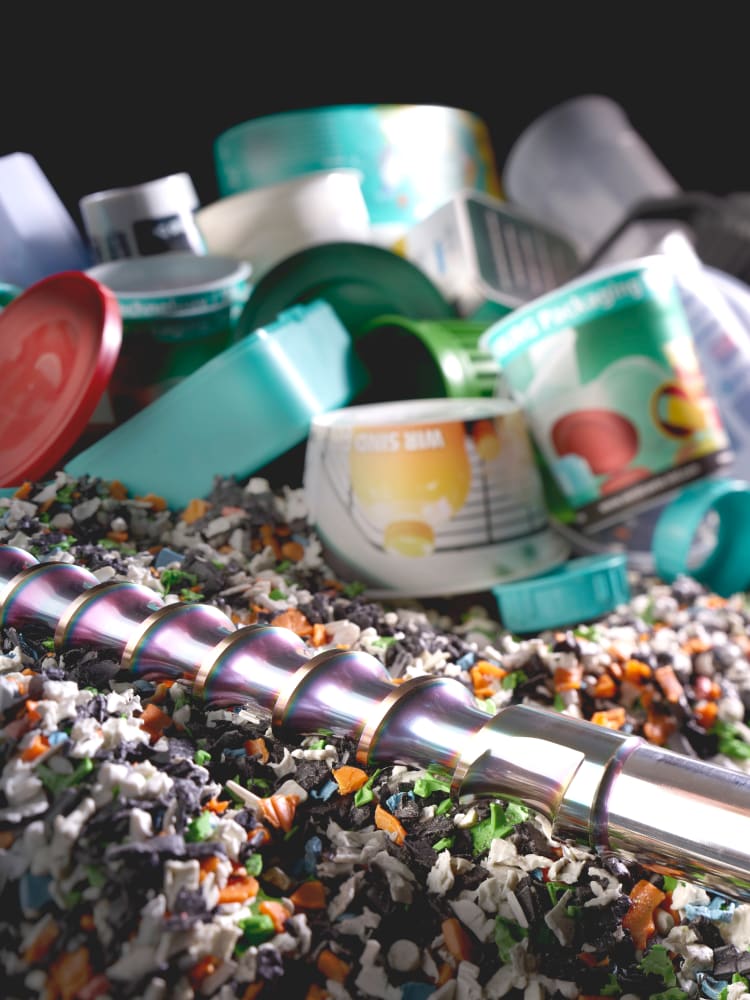