Technical Moulding: Saving resources and using installation space efficiently
World premiere - New generation of electric tie-bar-less machines / Automated overmoulding of fittings
One of the highlights at the ENGEL stand is the world premiere of the latest generation of its electric tie-bar-less victory injection moulding machines. This new model is fast, clean, and energy-efficient, and also features a completely new technical design - delivering additional advantages for users.
On the new victory electric, fittings are produced with a cycle time of just 23 seconds. The mould includes large-volume core pulls, which are optimally supported by the free access provided by the tie-bar-less design. Thanks to ENGEL tie-bar-less technology, even large moulds can be used on comparatively small machines, saving space, energy and investment.
After injection moulding, the fittings are automatically equipped with seals. The production cell is equipped with two easix articulated robots to handle this step.
Blocks made from recycled material with high structural stability
On an all-electric e-mac 220 injection moulding machine with 2,200 kN clamping force, ENGEL is producing thick-walled, foamed construction blocks for the building industry. The material comes from yellow bag household waste, reprocessed by EREMA. Mould and foaming agent formulation are supplied by Moxietec. For optimum foam homogeneity, an optimised mixing screw is used during plasticising. The result: components with up to 30 % weight reduction and 10 % higher strength. This technology is particularly well suited for logistics pallets and as a substitute for concrete in construction applications.
As 100 % post-consumer recyclate with corresponding material fluctuations is processed, the new iQ weight control plus plays a key role. After defining just two parameters, the digital assistance system automatically adjusts the switchover point and pressure curve during every injection cycle. This reduces scrap by up to 50 %.
An integrated automation solution with servo sprue picker and an integrated conveyor belt inside the machine makes the cell particularly energy-efficient and compact.
Packaging: Scalable sustainability in series production
Thin-walled cups with 30 % rPET produced using a stack mould
ENGEL is demonstrating a series-ready solution for processing rPET in thin-walled packaging on an all-electric e-motion 420 injection moulding machine with 4,200 kN clamping force. What was previously only feasible using hydraulic injection, ENGEL now achieves electrically. A 6+6-cavity stack mould from Plastisud is used to produce yoghurt cups made from 70 % virgin material and 30 % bottle-grade rPET. The rPET is supplied by NGR and upgraded for food contact via Liquid-State Polycondensation.
This production setup delivers excellent repeatability at high performance. The combination of injection compression moulding, iQ motion control, and iQ weight control plus enables the manufacture of thin-walled, precise cups with minimal material usage. The application already complies with the requirements of the Packaging and Packaging Waste Directive for 2030. Moreover, it illustrates the potential to replace thermoforming as the preferred manufacturing process, enabling producers to save on upstream steps (film production) and material (trimming waste). ENGEL thus presents a practical example of how sustainability and precision can be combined in an economically viable production environment.
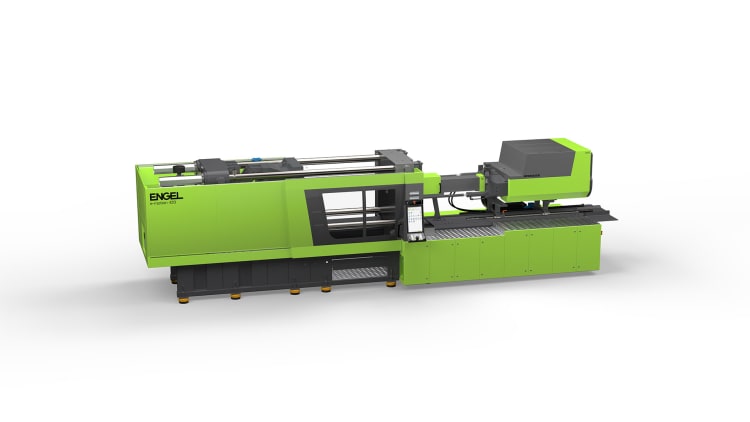
inject AI: Digital intelligence for real-world production benefits
Smart assistance systems with practical impact
With inject AI, ENGEL is taking its inject 4.0 programme to the next level. At K 2025, ENGEL will showcase the next step toward self-optimising machines by integrating artificial intelligence into many new and existing ENGEL products.
The iQ process observer monitors up to 1,000 parameters per shot, detects process deviations in real time, and provides AI-supported automatic correction suggestions - a key contribution to process optimisation and scrap reduction. The systems continuously learn from the data of all connected machines, creating added value for every new project - a genuine boost for quality and efficiency.
e-connect portal with AI: Digital support for every shift
In the event of machine or process faults, a new AI-supported feature in the e-connect portal provides machine-specific assistance - quickly, precisely, around the clock, and in all languages. Thanks to intelligent search functionality in the ENGEL machine manuals, downtime can be significantly reduced. The system will be available as a pilot series in time for K 2025.
Humans and AI - a team effort
ENGEL does not see AI as a replacement, but as a complement to human expertise. Adaptive assistance systems ease the burden on personnel, stabilise processes and increase equipment availability - an especially valuable benefit in times of skilled labour shortages. In this way, the self-regulating machine is gradually becoming a reality.
ENGEL - Your Partner for the Future
At K 2025, ENGEL is demonstrating how machines, automation, and digital systems can be combined into fully integrated manufacturing solutions. Each exhibit on the stand represents a production cell precisely tailored to meet specific customer requirements - and a well-considered, economically viable response to those needs. The exhibits are complemented by expert corners on topics such as plastification, technologies, temperature control, and training, where ENGEL presents customer-focused solutions.
Whether lightweight construction, the use of recyclates, validation, or process stability: ENGEL thinks in terms of solutions. The trade fair appearance encourages open, hands-on and forward-looking dialogue. Because while plastics processing may not be getting any easier, with ENGEL it remains manageable, flexible, and efficient.
K 2025: Hall 15, Stand B42&C58