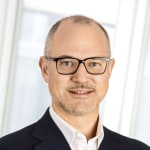
Rising energy and raw material prices see plastics processing companies face new challenges. "Reducing the CO2 footprint even faster gives companies leeway. Competitiveness and resilience are boosted," as Dr. Gerhard Dimmler, CTO of the Engel Group, emphasises in the run-up to K 2022. "Engel is the role model when it comes to solutions that save CO2 in injection moulding. And that is precisely what we are demonstrating in Düsseldorf this October."
"Engel offers a wide spectrum of mature and proven technologies and solutions that contribute towards reducing the use of energy and raw materials. The focus now is on making even more intensive use of these to substantially improve the CO2 footprint and the cost structure at the same time," says Dimmler. From the design, sample inspection and production, through to maintenance and service, Engel supports its customers throughout the product life cycle and beyond. After all, reducing a company's CO2 footprint is not a purely technical challenge. It requires close cooperation along the entire value chain, which Engel and other market players are actively engaged in.
Every participant in the value chain has a specific role. As an injection moulding machine manufacturer and system solutions provider, Engel is responsible for three areas: the overall efficiency of the injection moulding production cell, digitalisation of the injection moulding production processes, and processing technologies which support the circular economy.
Overall efficiency: It's a question of temperature control
Conserving resources and energy has always been firmly anchored in Engel's corporate philosophy. From servo-hydraulic, through hybrid, to all-electric, injection moulding machines by Engel are some of the most efficient on the market in their and performance classes. "Many processors think that they have already achieved the maximum energy savings potential by using an all-electric injection moulding machine. But a precisely tuned temperature control solution helps them do far more," as Dimmler explains. Supplying and dissipating heat often consumes more energy than the movements of the injection moulding machine in today's production operations. This is why Engel has focused intensively on mould temperature control for more than ten years, offering temperature control solutions perfectly tuned for the injection moulding machines. With dynamic single-circuit closed-loop control and demand-driven control of the temperature control units, these systems solutions by Engel combine energy efficiency with constant temperatures and very high productivity. This makes it possible to reduce energy consumption to an extent comparable with the energy savings achieved a few years ago by switching to a state-of-the-art drive technology.
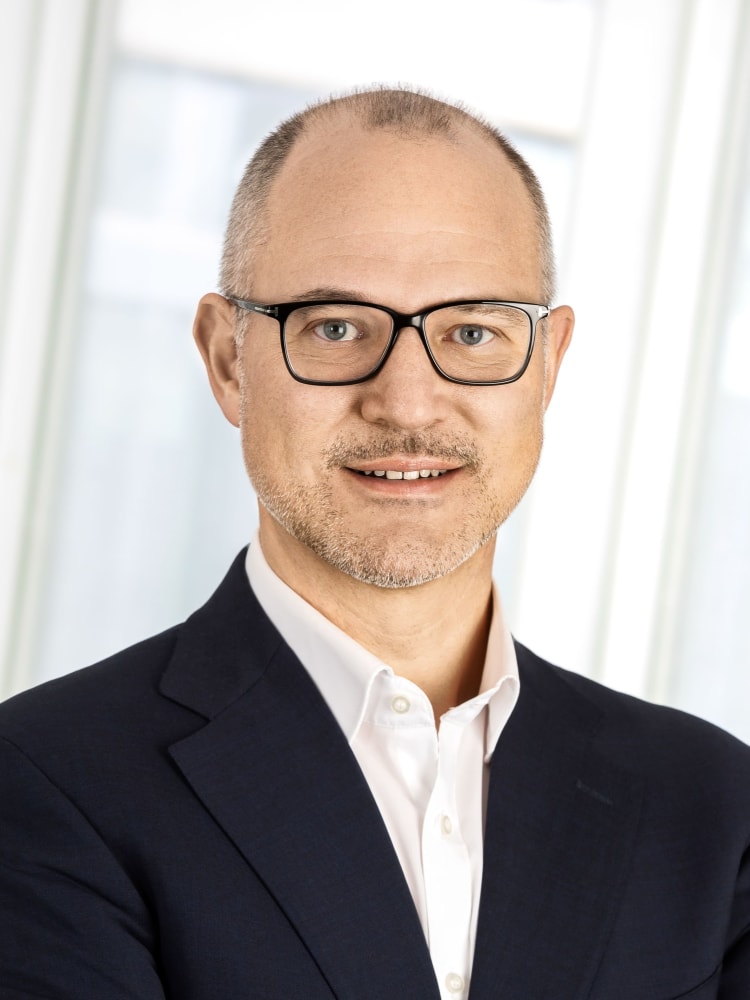
Digitalisation for consistently high product quality
iQ flow control is the smart assistance system which Engel specifically developed to optimise the temperature control processes. All told, the iQ product family includes nearly ten smart assistance systems and Engel will present another system at the K show 2022: iQ hold control. Smart assistance started ten years ago with iQ weight control, which automatically identifies fluctuations in the raw material and ambient conditions, and automatically adjusts the quality-defining process parameters individually for each cycle.
The self-optimising injection moulding machine is an essential feature in digitalising the injection moulding processes. It is all about avoiding rejects and boosting energy efficiency.
A recent study conducted by Accenture on behalf of bitkom of operations in Germany predicts that digitalisation could reduce the current CO2 emissions by up to 58 percent. At 23 percent, the manufacturing sector is responsible for a particularly large share of this.