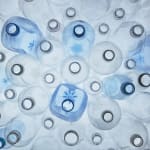
Brand owners and packaging converters in the plastics industry are facing major bottlenecks in recycled content availability. To overcome this challenge and meet ambitious recycling targets, recyclers and material sorting facilities (MRFs) are using advanced technologies to produce feedstock for high-grade applications, expanding their business opportunities.
As legislation continues to push for a reduction in plastic waste, the demand for high-quality recycled plastics are at a record high. Plastics are durable, efficient, and convenient, which makes them hugely beneficial to consumers and businesses alike. Making plastic products and packaging more sustainable is the challenge of our time. As brand owners look to increase the share of recycled content to reduce their production emissions and satisfy consumer demands, they are met with a new set of challenges. High-grade applications like automotive and packaging require high-quality recycling processes and advanced sorting technologies to effectively source feedstock from post-consumer and post-industrial plastic waste.
Demand vs. recycled content availability
In 2020, worldwide plastic production amounted to 367 million metric tons (mt). Europe produced 55 mt of plastic, with 70% of the total market demand coming from the largest countries, using 40.5% of the material for packaging production. In the quest to create a circular economy for plastics, the share of virgin material in manufacturing should be reduced and replaced by secondary raw materials. this, however, is easier said than done.
Plastic recycling has certainly had its share of bad publicity, not least due to downcycling - after all, there is a limited demand for items such as park benches, flowerpots and speed bumps. But The recycling industry, working in collaboration with members of plastic value chains, has now made it possible to create virgin-like recycled content with advanced mechanical recycling. Not only does this prove to be an economically feasible and practical alternative to primary materials, it also gives recyclers and MRFs the opportunity to create new revenue streams. Even in the case of highly contaminated plastic waste streams, like municipal solid waste (MSW), it is now possible to source quality feedstock that can be used to create new products.
The S&P Global Platts Analytics predicts that by 2030 more than 1.7 million metric tons of virgin polymers will be replaced by mechanically recycled plastics – compared to 688,000 mt in 2020. To date, only a tiny portion of recyclates have found their way into the production of new materials. Most of the recyclates are used for lower-grade applications. So, how can industries such as automotive, food and beverage, and cosmetics ensure a reliable supply of high-quality recycled feedstock? Bridging the gap of material shortages starts with effective collection of recyclables. Deposit Return Systems (DRS), for instance, are a global best practice for the recycling of beverage containers in a closed-loop system. There is not a one--fits-all solution: to achieve circularity, complementary solutions are needed to capture other products made of plastic, like post-consumer film packaging. Mitigating contamination and increasing the quantities of recovered recyclates across all waste streams is crucial to the future of plastics.
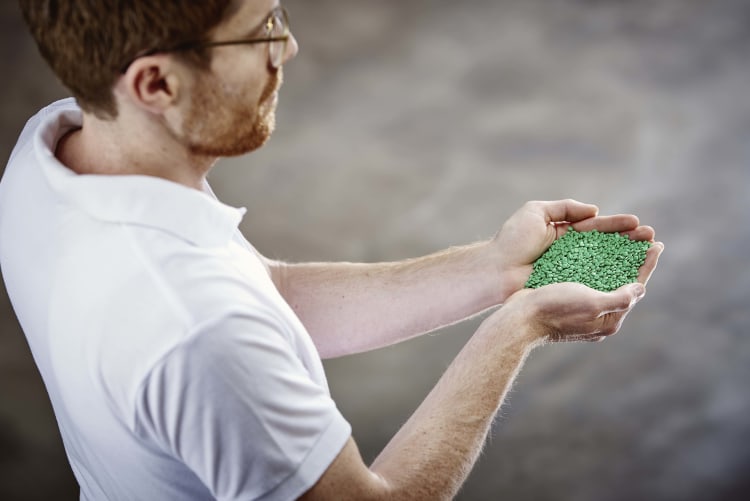