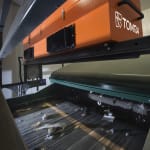
Opened in 2014, Roaf is a fully automated waste sorting plant featuring Tomra’s optical sorters and ranks second in sorting municipal solid waste by volume in Norway. Since it abolished the separate collection of plastics, the facility could boost its recovery rates of organics and plastics while maximizing its recycling efforts and keeping environmental impact low. Not only does the plant come closer to reaching EU’s 2025 plastics recycling rates of 50% %, but also uses the organics recovered for biogas production and the fueling of its waste collection trucks.
The facility is situated in Skedsmokorset, near Oslo, and collects and sorts waste from 7 surrounding municipalities. Until seven years ago, plastics have been collected separately curbside, just as paper and cardboard and residual waste. Unfortunately, a lot of recyclables still ended up in the household waste fraction and were thus deemed to be burnt. To optimize resource recovery and mitigate the negative impact of incineration Tomra and Roaf jointly examined the household waste composition and came up with a new business model to introduce a new waste management approach for the seven municipalities served.
Mixed waste sorting drives up resource recovery
Based on a detailed analysis and various tests carried out with municipal solid waste examples from the region in Tomra’s Test Center in Germany and locally in Norway, the partners developed a new business model. The new approach includes a change in the region’s waste management and collection practices and the construction of a new sorting facility. As for waste collection, the municipalities Roaf serves abolished the separate collection of plastics and now follow a 3-container waste collection system: inhabitants dispose of biowaste in green bags and throw it together with plastics and residues in the municipal solid waste container, which is collected by a Roaf truck and transported to the sorting center. A second container gathers paper and cardboard whereas the third one is used to dispose of glass and metal packaging. The second part of the new business model was the construction of the world´s first fully automated sorting plant for MSW. After a 3-year period of extensive planning, German plant builder Stadler constructed the plant within only 3 months and was awarded the German-Norwegian business award for its efforts in 2014. The trommels, bag openers, ballistic separators, eddy current separators, overhead magnets, and vibratory screens work in unison with the most advanced optical sorters from Tomra.Sixteen Autosort’s process 40 tons of waste per hour. From this waste, the units recover biowaste, paper, and plastics with high levels of accuracy in the sorting process.
Once the organics along with the residues collected curbside arrive at the sorting plant it is fed into the facility. First, three of Tomra’s Autosort systems separate green bags from the remaining waste. Whereas the green bags are sent to a biogas site, where the organics are converted into biogas for refueling the plant’s collection trucks and bio-fertilizers, the remaining waste bags undergo further sorting steps. Different drum screens separate the materials by before ballistic separators and 16 highly precise Autosort’s undertake a much more precise differentiation by material type. Thanks to the sensor-based sorting units’ advanced technologies including NIR and VIS, five different types of plastics (LDPE, HDPE, PP, PET, and mixed plastics), as well as paper, can be accurately separated from the infeed material. In the last step, magnets and eddy-current separators remove metallic fractions. All individual fractions generated are stored in bunkers and sold to European processors, who turn the materials into high-quality recyclates.
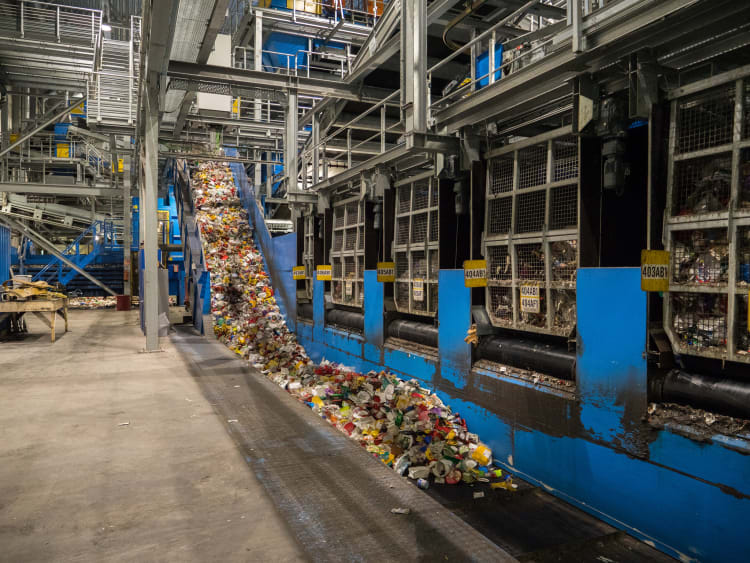