Omni Recycling Machines
Gneuss’ MRS Extrusion Technology is known as an alternative for the reprocessing of contaminated materials like polyester (PET), polystyrene (PS), polypropylene (PP) or polyethylene (PE). In combination with Gneuss’ highly efficient Rotary Filtration Systems, optimized vacuum technology, an online viscometer VIS and Gneuss Measurement Technology, customizable recycling lines tailor-made for a specific material can be engineered. As an option, light-weight or fluffy materials can be fed into the extruder via a 3C Rotary Feeder. OMNI recycling lines offer Several Letters of Non-Objection (LNOs) from a North American food safety authority, EFSA conformity and local approvals in Latin America confirm the decontamination efficiency of the technology. As volatile contamination is removed very efficiently in the MRS extruder under vacuum and solid contamination is removed by fine filtration in the rotary filtration system, OMNI recycling lines offer high quality and food compliant recycling in one simple, compact and sustainable extrusion step. Typical applications for Omni Recycling machines include the processing of PET reclaim, such as bottle, sheet regrind or fiber waste, into high quality end products, such as thermoformed sheet (suitable for food contact), staple fiber, POY, FDY, BCF or strapping tapes. In addition, a wide range of input materials such as PS, PP, PE, or PLA can be recycled. The Omni series can also be used in the decontamination of post-consumer waste to produce direct food contact products such as HDPE bottle caps or milk bottles, coffee caps and for odor reduction and degassing of PA, SAN or other polymers.
Omni 110 Recycling Machine for post-consumer PET reclaim
At the K show, Gneuss will present the core of an Omni Recycling Machine - a Multi Rotation System MRS 110 extruder. After the show, the complete line - including, among other components, a water ring vacuum system and the fully automatic RSFgenius 90 melt filtration system - will be delivered to Cotnyl, a leading Argentinian manufacturer specializing in thermoformed plastic packaging. Designed to process 600 kg/h of undried and uncrystallized PET or 400 kg/h of PP, the system will produce high-quality thermoforming sheet for food packaging applications. The technology has already been approved for food contact by Argentina’s food safety authority Senasa.
In addition to its compact design, which requires very little space and can therefore be easily integrated into existing premises, the Omniscores highly in terms of flexibility. The fully automated control of vacuum, extruder, dosing, degassing dwell time and filter exchange ensures a consistently high quality of the end product while allowing the use of lower cost input materials. With the tight and varying materials market, it is becoming increasingly important to have maximum flexibility in regard to the input material, especially in the case of varying and uncertain input qualities in the future. The compact design also results in very low energy consumption, significantly reducing the CO2 footprint of the recycling process.
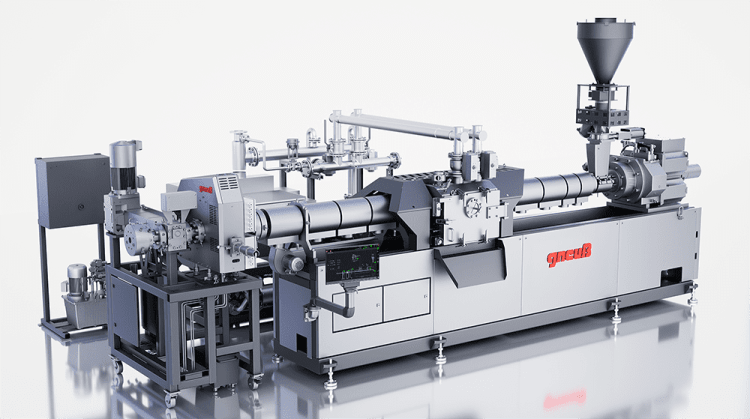
Open House at Gneuss
Gneuss’ headquarters are located just about 200 kilometers from Düsseldorf. During the K trade fair, an Open House event will take place at the Gneuss Technical Center. On Friday, October 10, several systems will be running at the facility in Bad Oeynhausen. Various applications will be demonstrated, focusing on key topics such as odor reduction and the recycling of plastics for food contact applications.
Gneuss Measurement Technology
Reliable Sensor Solutions from Gneuss - Gneuss offers robust and adaptable sensor technology for pressure and temperature measurement in extrusion processes. Designed to meet the harshest industrial demands, Gneuss sensors withstand abrasion, corrosion, and extreme temperatures. Thanks to flexible in-house production, Gneuss delivers both standard and custom-made sensors with short lead times.
Safety and Quality in Focus - the increasing demands placed on safety and quality make the continuous monitoring of measuring equipment essential. This is particularly true of pressure sensors with a safety function. The reliable Gneuss CCS 1000 pressure sensor testing device is now available with a heated sensor holder, enabling testing under real operating conditions. Thanks to its modular design, the CCS1000 can also be retrofitted with a temperature-controlled pressure port. Additionally, the newly developed clamping device for the sensor holder reduces wear on the sealing surfaces, preventing leaks during testing. Gneuss can provide a customised solution for your testing needs based on the CCS1000. Pressure ports are available for various thread types, including ½” and M18. Display units can be integrated for the sensor types you use on request.
Future-proof - Gneuss sensors are future-proof thanks to digital IO-Link communication and optional identification using RFID chips.
Visit Gneuss at K 2025: Hall 9, Stand A22.