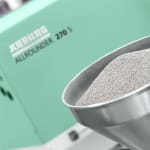
Taking place between 9 and 13 October, the World PM 2022 Congress & Exhibition is returning to Europe after six years. In the French city of Lyon, at the industry’s largest event for powder metallurgy, Arburg will be using its stand (139 - 144) to showcase an efficient and precise powder injection moulding (PIM) application in which a hydraulic Allrounder will produce complex mass components from an innovative BASF feedstock. Known as primary levers, these components are used in the valve control systems of car engines.
World PM 2022 will focus on additive manufacturing and systems such as presses and sintering plants for processing metal powders. Powder injection moulding (PIM) is an established process for producing high-quality components made of metal and ceramics, designed for applications such as the automotive industry and medical technology. It is an area in which Arburg boasts decades of expertise and is able to offer a full spectrum of support.
Highlight in practice: primary levers
Arburg will be demonstrating the PIM process on a hydraulic 370 S Allrounder with a clamping force of 700 kN, using an example of a metal primary lever - one of the very first MIM components in a combustion engine. The cycle time is around 40 seconds. For precise processing of metal powders, the exhibit is equipped with a special MIM cylinder. The aXw Control ScrewPilot feature, integrated into the machine controller, ensures a stable filling process by regulating the position of the screw. The feedstock processed is Catamold motion 8620 from BASF, which was developed for high-performance components in the automotive industry.
Highly sought-after: PIM partner Arburg
Machine manufacturer Arburg has well over 50 years of experience in powder injection moulding. The PIM Allrounders are the ideal solution for a broad range of applications and sectors, and are used in areas such as the automotive, jewellery and watch industries, plus the IT and dental sectors. Arburg’s expertise ranges from feedstock preparation and the production of complex precision small parts all the way through to the integration of assemblies and the conceptual design and realisation of complete turnkey systems. Arburg even has its own PIM laboratory, which is now almost a unique selling point on the market. Its broad-ranging areas of skill cover not only powder injection moulding itself, but also all the process stages upstream and downstream of this - including material preparation, debinding, sintering and part analysis. Arburg’s experts are continually working to develop the PIM process, keeping customers’ wants and needs in mind every step of the way. They also provide advice on component geometry and material selection, in addition to establishing links with potential system and tool suppliers.
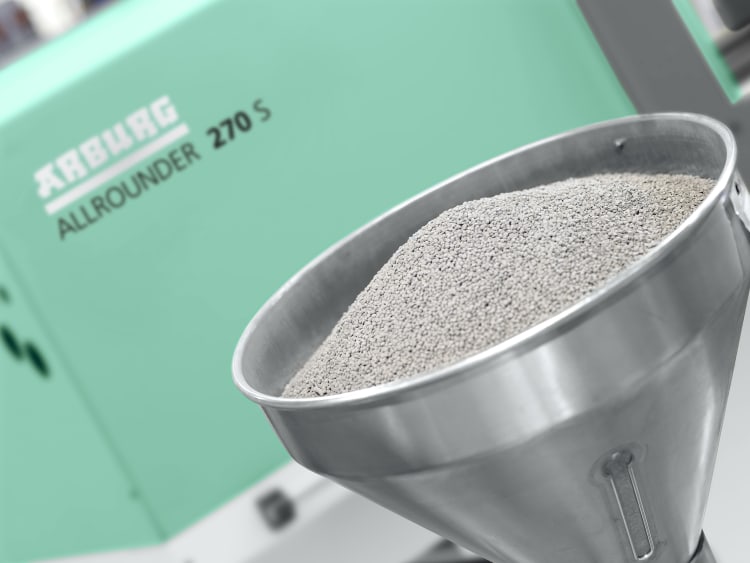