As a result of its flexibility, the Xelter range can also be used in the household appliance sector: an ongoing collaboration with one of the leading players in the industry, has led to the production of seals for washing machine drums. Yet again, they provide a suitable replacement for rubber, as Sirmax elastomers are the only ones currently on the market to possess the physical characteristics to replace it. However, there is one key difference: Xelter products are all recyclable.
Xelter elastomers are also used for applications in the building industry for insulation and sealing systems as well as in the Sports & Leisure, where the new-generation polymers are applied in ski boots, technical soles and anywhere a secure grip is needed in sports equipment (e.g. Pro Grip brand grips). In all cases, Sirmax solutions follow a tailor-made approach, which is designed to adapt, just like Xelter, to the customer’s requirements.
“The Sirmax Group’s commitment focuses on three core areas,” explains Stefano Capurro, Global Product Owner Elastomers Director. One of the goals remains to achieve better performance on elasticity by replicating rubber characteristics more effectively, with a particular focus on the combination with rigid materials. Furthermore, Sirmax is actively working on contact electrification, which is instrumental in enhancing product safety, especially the flame-retardant capacity of polymers. A third, highly ambitious goal concerns the production of antibacterial plastics through the use of non-toxic materials that can drastically reduce the proliferation of microbes on finished materials. A feature that is increasingly sought after by the market and can make a difference, not only in the light of pandemic risks but also of the emerging and ever more widespread problem of antibiotic-resistant bacteria, which is of particular concern to hospitals.”
Sirmax and its presence in Poland
By attending Plastpol, Sirmax consolidates its Polish presence, which dates back to 2006, when the Italian company set up its first plant in Kutno, within the special economic zone of Łodz. Besides being the largest in the entire group, this 52,000 square metre facility (20,000 of which are covered by the production area) can manufacture up to 85,000 tonnes per year of plastics, most notably polypropylene compounds and engineering plastics for the automotive and home appliance sectors. An investment in technology and human resources that paid off, so much so that, just thirteen years later, Sirmax doubled with another facility, the group’s twelfth, with a production area of 12,500 square metres, and the new products of the Xelter family see the light of day in this second facility. Overall, the two Polish plants employ 130 workers.“Poland remains a strategic region for Sirmax,” adds Massimo Pavin, President of Sirmax Group, “so much so that we are evaluating the possibility to expand our production facilities in the next years, to meet the growing demand in both the automotive and appliance sectors. The shift towards sustainability we have undertaken since 2019 and the continuous investment in research and development further strengthen our standing as a highly innovative and competitive manufacturer. The market demands a lot nowadays, even from a simple plastic granule; the goal is total recyclability, circular economy, reduction in material usage, and attentive design that allows for never-ending service life, and Sirmax is already providing the customer with all of that.”
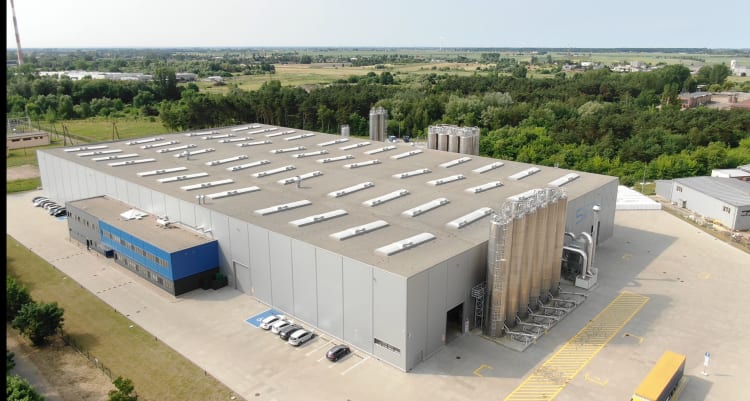