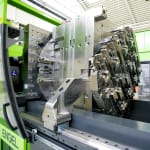
When ENGEL first unveiled a tie-bar-less injection moulding machine at the K trade fair in Düsseldorf in 1989, the reaction was mixed: technical fascination on one hand, open scepticism on the other. At that time, few would have predicted that this “revolutionary” design would evolve into one of the most successful technologies in injection moulding machinery. Today, 35 years later, ENGEL looks back on more than 85,000 tie-bar-less machines delivered worldwide - and continues to drive this innovation forward with a consistent focus on customer needs. At this year’s K 2025, ENGEL is presenting a world première: a new electric tie-bar-less injection moulding machine.
Customer benefit as the starting point
The impetus for developing a tie-bar-less machine came from practical experience: A customer told ENGEL how much the four tie-bars interfered with mould set-up and how much easier mould changes would be without them in the way. The development department at ENGEL picked up on this idea and examined whether it would be possible to design the clamping unit of an injection moulding machine entirely without tie-bars. A simple idea - yet a major leap in design. Up until that point, it was regarded as an unshakeable principle in mechanical engineering that an injection moulding machine had to have four tie-bars, regardless of or application. The tie-bar-less clamping unit marked a radical new beginning in engineering.
Technical pioneering work from Upper Austria
The breakthrough was achieved with a novel joint principle that compensates for the asymmetry of force application in the C-frame. Instead of guiding the platen over tie-bars as previously done, the mould is clamped via a solid frame - with a freely movable bending-bar joint between the moving platen and the clamping piston. This Flex-Link element, now patented and further developed under the name Force Divider, ensures that the mould halves remain absolutely parallel. It also provides for an even distribution of clamping force across all cavities of the platen and thus over the entire mould surface. This marked the birth of a new generation of machines that not only impressed technically but also opened up new freedoms in mould design. The first complete series went into production in 1990 - the name victory became the official product name in 2000.
Experience and evolution across four generations
What began with a lever pin in the prototype has been systematically developed over several generations. ENGEL has continuously refined the joint system of its tie-bar-less machines, evolving from manually lubricated slide bearings to today’s Flex-Link with decentralised force application. At the same time, the machine series has been progressively expanded and enhanced with new drive technologies.
Today, the tie-bar-less machine portfolio from ENGEL comprises three variants:
- Hydraulic, under the victory line, for flexible and universal use in technical moulding.
- Hybrid, under the e-victory line, featuring an electric injection unit for technical parts requiring higher precision.
- Electric, under the victory electric line, designed for particularly demanding applications such as high-volume precision components.
These three variants all share the advantages of the tie-bar-less clamping unit: maximum utilisation of the mould mounting surface, faster mould changes, ergonomic access to the mould area, and flexible automation concepts.
Another economic advantage of the large, open mould area is that it allows the use of very large and complex moulds on machines with comparatively low clamping force.
Success through consistency of principles
ENGEL’s continued unique position in the field of tie-bar-less technology is not only due to its early lead in technology. The company has also secured its position through continuous development and comprehensive patent protection. It became clear early on that the benefits go far beyond simplified mould changes. Especially for high-cavity moulds with a small projected area, the tie-bar-less design allows for the use of smaller machines with significantly lower energy consumption and reduced investment costs.
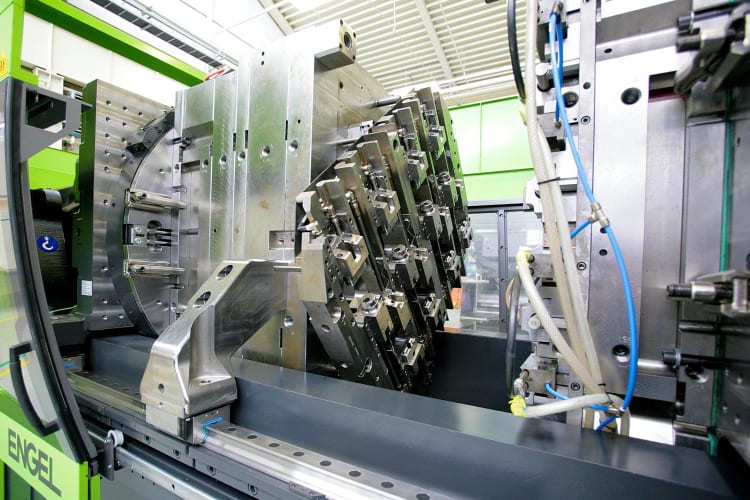
Energy efficiency by principle
A milestone in the development was the introduction of the ecodrive servo-hydraulic drive technology, which reduces the energy consumption of hydraulic machines to the level of all-electric ones. In combination with the tie-bar-less clamping unit, this results in an ideal solution for demanding applications with high requirements for energy efficiency. Today, ENGEL equips all hydraulic and hybrid injection moulding machines with ecodrive as standard.
Forward-looking: modular, integrated, future-proof
The fact that the tie-bar-less machine technology remains as relevant today as it was 35 years ago is evident above all in its adaptability. Whether for cleanroom applications, multi-component technology, or highly automated production cells - ENGEL’s tie-bar-less injection moulding machines can be configured in a modular and needs-based way. In doing so, they stay true to their core principle: maximum efficiency through functional simplification.
Outlook for K 2025: next stage of evolution with a world premiere
At the K 2025 trade fair, ENGEL will present the next evolutionary stage of its electric tie-bar-less technology for the first time. The focus is on design advancements that create additional benefits for users. The goal is to address customers’ specific requirements even more precisely - just as it was 35 years ago, when a simple question led to a completely new machine concept.
Visit us at K 2025 in Düsseldorf, Hall 15, Stand B42 & C58