Lower production and material costs
Injection molding of plastics generally eliminates expensive post-processing and assembly steps, which are often required when molten metal is poured into a steel mold under high pressure and the metal solidifies into a solid casting. Processes such as deburring, sandblasting, milling or thread cutting are usually used to make the die-cast metal part ready for use. Another advantage of plastic parts over metal parts is that no corrosion protection needs to be applied. This all contributes to the fact that, in addition to the material costs, the manufacturing costs for injection-molded components are also lower than those for die-cast metal parts.
But that's not all: injection moulding allows more complicated geometries and colored components to be produced. This results in greater design freedom than with metal die-casting. Another advantage of plastics is that they are lighter than metal. This is particularly important for applications in vehicles: every gram saved in electric cars, for example, helps to reduce power consumption. This increases the distance that can be covered on a single battery charge. Furthermore, plastic components dampen noise better than metals, which is also important in the automotive sector and in mechanical engineering.
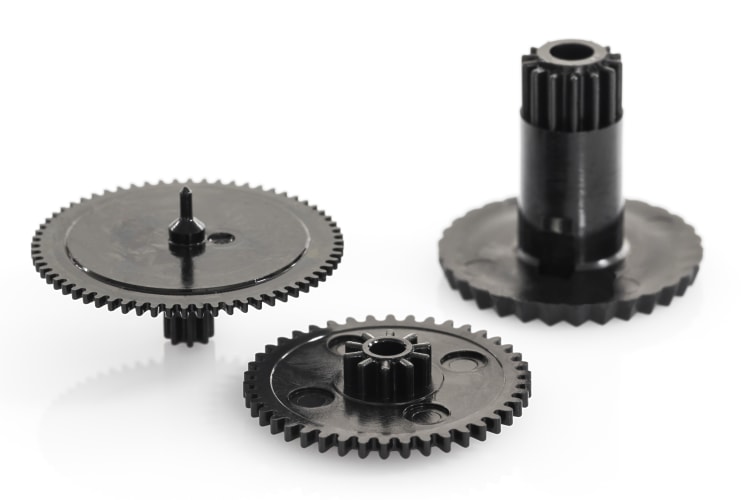
Screws, rollers, fan wheels and housings
- In view of the potential cost savings and many advantages, manufacturers should check whether they can replace die-cast metal parts with radiation-crosslinked plastics in certain applications - advises BGS expert Daněk. Which molded parts in particular? - For example, screws, fastening clips and rollers in cars and other vehicles, fan wheels in heat pumps, housings for or in electronic devices and bonded plastic-metal composite materials in shipbuilding.
Conclusion
There are many factors to consider: In addition to the specific application, these are primarily the number of units, the design complexity and the required quality of the components. Close cooperation between material scientists, engineers and product designers is recommended in order to take all aspects into account. Then the substitution of a die-cast metal part with a more cost-effective injection-molded plastic component can become a success story.
Author: Dr. Michal Daněk, BGS Beta-Gamma-Service