Irradiation changes the behavior of polyamides under heat. For example, the modulus of elasticity of non-crosslinked glass fiber-reinforced PA 66 drops sharply at around 240 degrees Celsius: the material begins to melt. Radiation-crosslinked PA 66 is different: at 240 degrees Celsius, it has a modulus around 120 times higher than non-crosslinked PA 66. The residual stiffness hardly drops at all up to a temperature of 360°C. In summary, this means that the cross-linked plastic retains sufficient strength even at temperatures of 350°C. In addition, radiation crosslinking reduces the coefficient of thermal expansion, which ensures good dimensional stability of the manufactured molded parts at high temperatures.
The radiation treatment also improves the mechanical properties. It reduces the tendency of plastics to deform plastically under mechanical stress, which can impair functionality. The reduction of this creep is essential for plastics to be able to replace metals in fastening elements or screws, for example. The creep tendency of glass fiber-reinforced PA 6, for example, is reduced by around 70 percent through radiation treatment.
Cross-linked plastics are also more resistant to brake fluids and other aggressive chemicals. They are also less affected by solvents. This is demonstrated, among other things, by the fact that they retain their strength better when exposed to solvents.
Another important criterion when selecting materials for machine elements, for example, is the tribological behavior of the materials. This is because wear and friction are factors that are decisive for the service life of components such as plain bearings, guide rollers and gear wheels. Blasting has a positive influence on tribological behavior. For example, it reduces the wear coefficient of PA 66 by 60 to 70 percent.
- The radiation crosslinking of a plastic is always carried out on the finished component by a service provider - emphas Daněk. - This means that the manufacturer of the respective component can carry out the shaping by injection molding, extrusion or blow molding as usual - This means there are no additional costs for purchasing new machines or tools. They can carry out the production process as usual and at the optimum speed. The beam crosslinking of components at a service provider can be integrated into the transport route to the end customer to save time. Post-processing is not necessary.
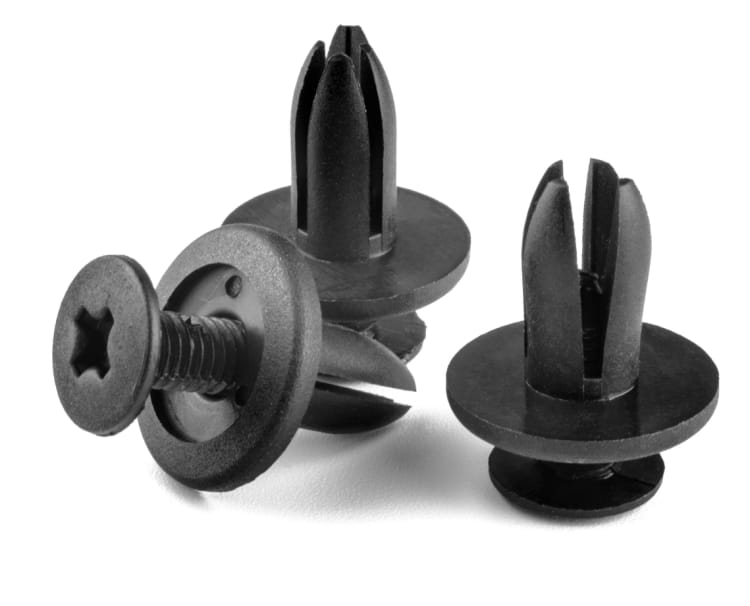