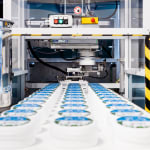
If you were to put a figure on enhanced productivity, what would your ultimate manufacturing output goal be? Five percent, maybe ten? Given the current challenges, some processors may even push for 20 percent! Research by Sumitomo (SHI) Demag reveals that when all the productivity production stars align - including optimising all-electric technology, engaging people, utilising automation and other digital tools, and reducing production downtime - 50 percent or higher is entirely reachable.
Productivity is the hot topic at Interplas 2023, with a number of seminars and panel discussions already scheduled. Inevitably, these programs will showcase and share best practice on how to ‘achieve more output with the same or less effort’. After-all, this is the ultimate quest.
Ahead of the productivity curve is Sumitomo (SHI) Demag. Gathering information and data when visiting customers following new all-electric and machinery installations, the team reveals everything they’ve learned. Including how both small and large polymer processors can lean on their technology and team to unlock more untapped productivity opportunities.
All of this information is being captured in an insightful new Whitepaper. However, given the significance of this trailblazing evidence and yield-boosting benefits, the team shares a taster of how mass moulders can, with just a bit of expert support and guidance, double their manufacturing capacity and productivity.
Turning empty promises into reality
Imagine the profit possibilities if each all-electric injection moulding machine within your fleet delivered an extra six months of processing capacity. How many extra projects could you take on? How much machine footprint could this save? What would this mean for your delivery schedules and customer satisfaction?
Phased Total Factor Productivity improvements to manufacturing processes holds huge promise. For many UK moulders, this could finally be the golden egg to change the operational landscape and future prosperity of polymer manufacturing firms of all s?
Integrating an all-electric machine into production lines, alongside intelligent utilisation of digital tools and automation, combined with investing in training and development, can decrease cycle times by up to 55% percent. This can equate to an extra 168 days of production, illustrates the Processing Productivity whitepaper.
It doesn’t require doing everything all at once. Instead, the Sumitomo (SHI) Demag team assures customers that in a short space of time, marginal gains can unlock accumulative enhancements to boost profit margins.
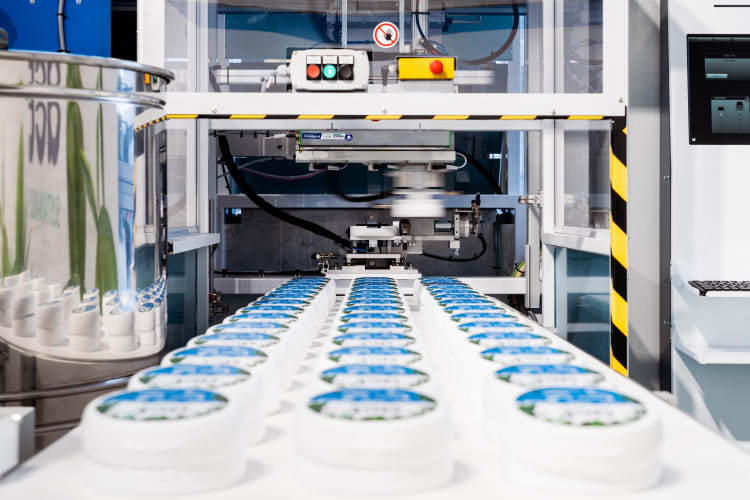
Field site tests prove that integrating an all-electric machine into production lines, alongside digital tools and automation, combined with training and development, can reduce cycle times by 49.3% .
All-electric closes the productivity chasm
It’s widely considered a ‘given’ that energy efficiency and reduced pollution are the benefits of all-electric injection moulding machines. Especially in today’s eco-conscious manufacturing world. However, beneath the hood of these machines are a number of velocity and injection power features that, when used correctly and repeatably by moulding operatives, result in faster cycle times and more stable start-ups. Even before any process optimisation steps have been introduced and expert setting knowledge has been imparted.
The advanced direct drive technology deployed by the IntElect series illustrates this point. Reducing a 10 second dry cycle time by just 0.55 seconds, for instance, can equate to an additional 2,274 cycles every day. Multiplied, this productivity improvement alone can add up to 14.3 extra production days!
MGS Technical Plastics is just one customer that observed an instant dry cycle time improvement of six seconds after switching from a Demag Ergotech 50ton to an IntElect2 50ton. “From these figures we can deduce that it equates to a 20 percent increase in cycles per year, giving MGS over 53 days of extra production capacity,” notes area sales manager Ashlee Gough.
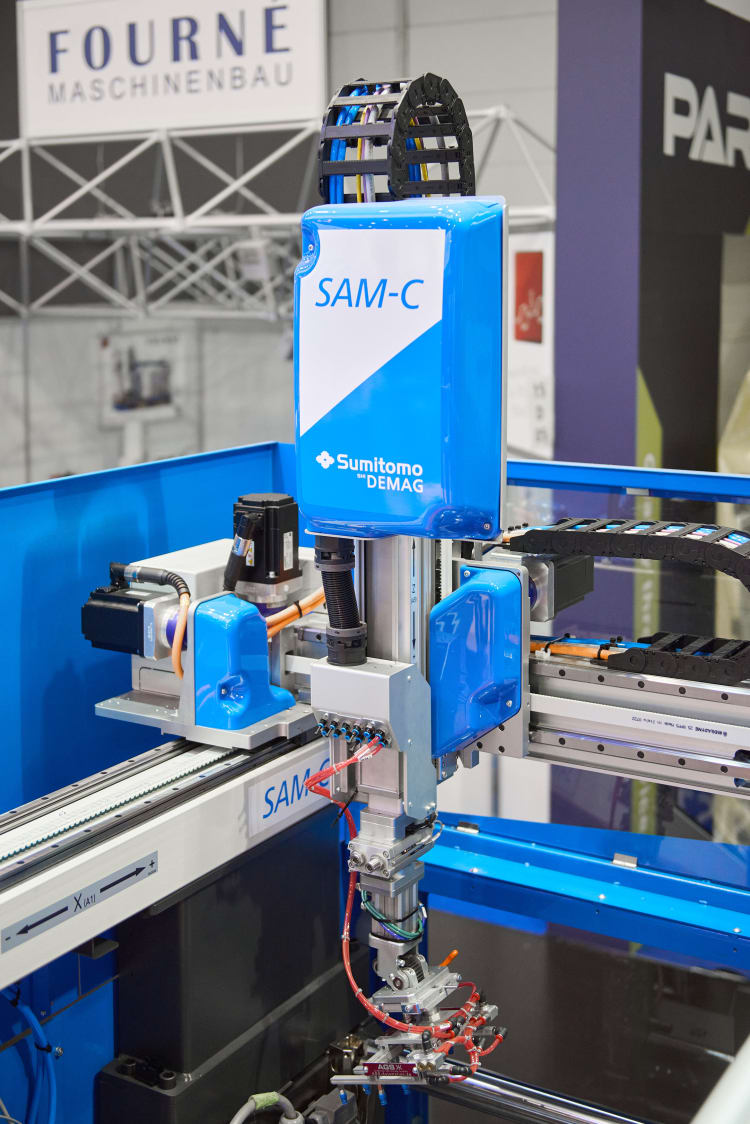
At Interplas 2023, Sumitomo (SHI) Demag will unveil its new Productivity Whitepaper along with a compact, full turnkey cell featuring an IntElect75 and SAM-C5 handle & box robot