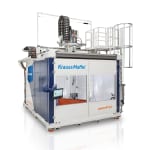
“Make plastic green – with high quality and efficiency” - this is KraussMaffei’s motto at the NPE show in Orlando, Florida (May 6 to 10, West Hall, booth W 600). Front and center of the trade show appearance are innovative technologies and solutions of injection molding, extrusion, reaction process machinery, automation and additive manufacturing focusing on circular economy and reducing the CO2 footprint.
- Sustainability is an added value - for us and for our customers. In line with our motto ‘We make plastic green’, we therefore aim to be a leading global supplier of sustainable solutions for the plastics processing industry - explains Nolan Strall, President KraussMaffei Corporation. In order to achieve these goals, the circular economy is a supporting pillar of KraussMaffei's corporate strategy.
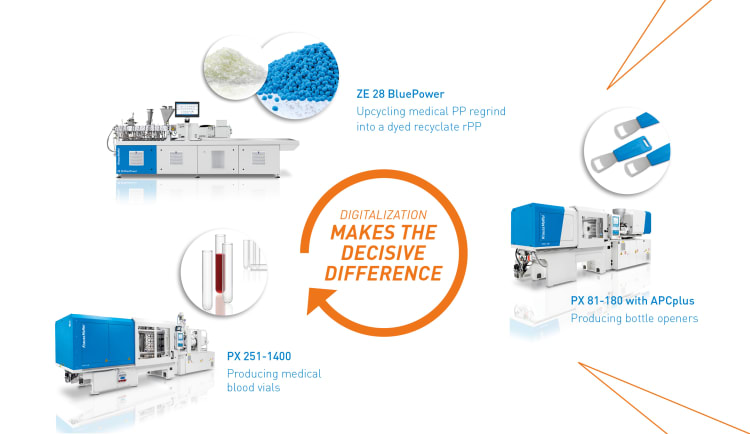
Circular Economy live @NPE
Trade show visitors at NPE can experience the entire material cycle, from a short-live medical blood vial to a long-live bottle opener, at the KraussMaffei booth. Starting with injection molding on a PX 251-1400, moving on to the upcycling process and to the twin-screw extruder ZE 28 BluePower and then to the all-electric injection molding machine PX 81-180, KraussMaffei demonstrates everything from valuable utilization of raw materials from disposable articles to production of premium quality components with a long service life.
The all-electric PX 251-1400 produces 32 medical blood vials per shot from PP 9074 MED material supplied by ExxonMobil. After shredding, these vials serve as base material for the up-cycling process carried out on the ZE 28 BluePower twin-screw extruder. Here, various additives such as bonding agents and liquid pigments are added, mixed and homogenized. The resulting re-compound is transferred to the downstream injection molding machine – more precisely to the an all-electric PX 81-180.
As recyclates can cause significant process fluctuations due to different viscosities, the PX 81-180 is equipped with APCplus. This machine function reliably compensates for these fluctuations. This allows components to be produced with consistently high quality with scrap reduced to a minimum - another important contribution to greater sustainability.
Saving CO2 and costs with DCIM
Another highlight form the area of sustainable solutions at the KraussMaffei booth is the DCIM process (Direct Compounding Injection Molding) with which up to 50 percent of material costs can be saved, also giving the processor considerably more freedom and control in the development of formulas. For DCIM, a single-screw extruder is installed in a space-saving piggyback position directly over the injection unit of a standard hydraulic machine.
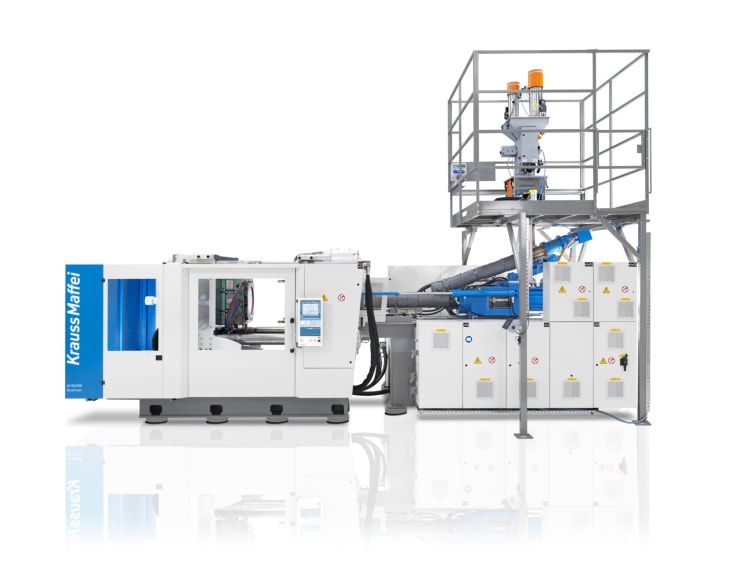
The compounded melt is conveyed into the plasticizing unit in a single heating process, which reduces degradation of the polymer. In addition, the one-step process conserves energy and reduces the CO2 footprint. At the NPE show, a GX 1100-4300 DCIM will produce rugged reusable crates made of three different recycled materials.
The intuitive machine function smartOperation allows the startup and control of the injection molding machine as easy as using a coffee machine. This not only enables defect-free machine operation but also increases process stability and thus boosts efficiency in production. In particular, machine operators without in-depth prior knowledge of injection molding technology benefit from the advantages of smartOperation.
New MuCell screw with 30 percent higher plasticizing performance
MuCell can do everything that's currently in demand - generate savings on material, energy and investment costs - and thus noticeably reduce the CO2 footprint of products. At the NPE show KraussMaffei is highlighting its new universal screw for MuCell applications with 30 percent higher plasticizing performance.
The new HPS-Physical Foaming screw has a longer three-zone area, which can be universally used for all plastics (with and without fiber reinforcement) and has a plasticizing capacity that has increased by up to 30 percent. This allows for the selection of lesser screw diameters than before, which significantly reduces investment and operating costs for the plasticizing unit, or for the generation of a greater output using a screw of the same as before.