Good parts around the clock
Currently, the new high-speed production cell is fully utilized with a mold for producing crystal clear bowls. With their facet design, these plastic bowls are indistinguishable from glass bowls at first sight. They can be found on the refrigerated shelves of supermarkets filled with barbecue salads of the Merl brand. Heinrich Axmann has been producing these packages for many years for FMR Frische Manufaktur Rheinland GmbH&Co. KG.
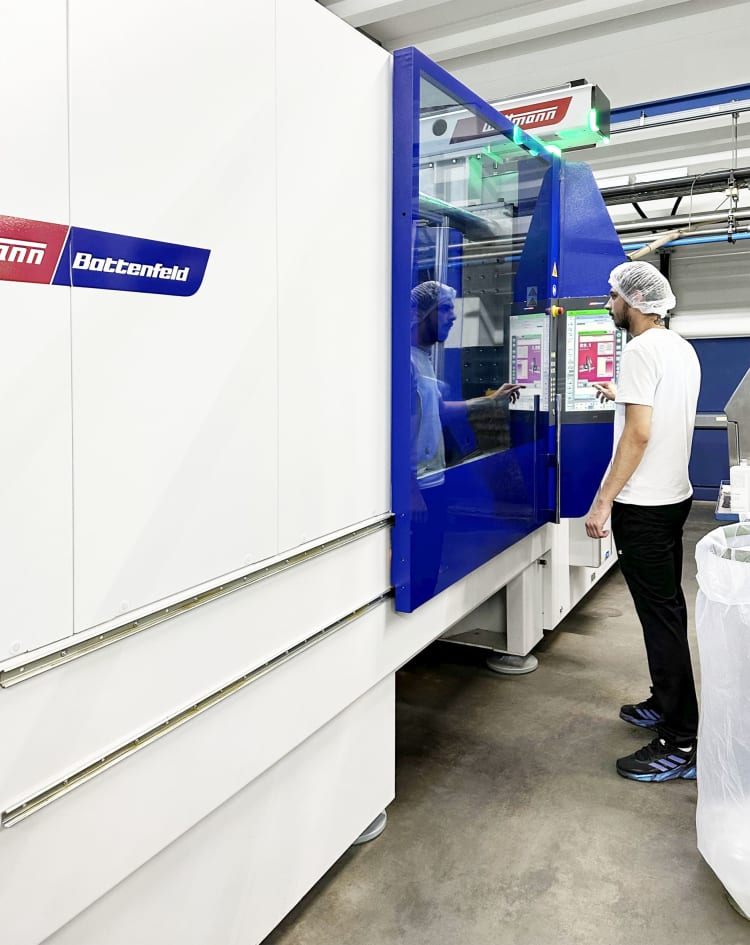
- These salad bowls make very similar demands on thin-wall injection molding to those of the newly developed ready-to-eat food bowls - Brüggemann points out to us - On this product we are testing how far we can go with the new EcoPower Xpress - The crystal clear bowls also come with only 0.5 mm wall thickness and a sophisticated design. They are produced in a two-cavity mold with 5.7 seconds cycle time. The filling time for the total shot weight of 44 grams is less than 0.1 second.
At the time of our visit to Rodenkirchen, the fourth week of continuous operation has just begun. - The machine runs around the clock with maximum performance and consistently high parts quality - Brüggemann reports - Ultimately, the machine’s reproducibility is the decisive argument in favor of its use for injection molding food packaging products.
Reliable robot movements
The target set for the new tear-open bowls is a cycle time below 5 seconds. The total shot weight will be 70 grams, and here, too, the maximum filling time is expected to be 0.1 second. The main factors determining the cycle time are cooling time and parts removal. This is why the EcoPower Xpress has been equipped with the Sonic robot. Wittmann presented this high-speed robot model specially developed for high-speed applications in the packaging industry for the first time at the K 2019. - Its strength is its great reliability in extremely fast movements - Jörg Schröer, Regional Sales Manager of Wittmann, explains. - This is precisely what shortens the removal time.
Wittmann robots have enjoyed the highest level of trust at Axmann for decades. The company’s machinery includes more than 30 injection molding machines of different brands. All of these are equipped with linear robots from Wittmann.
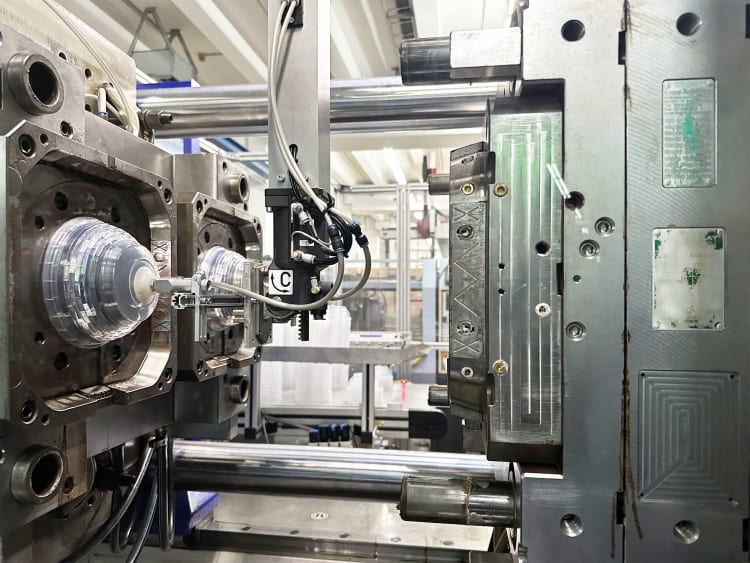
With the new complete production cell for making the thin-walled bowls, the company has purchased for the first time a fully integrated solution from a single source. - For us, this had the great benefit of getting the entire equipment delivered in full compliance with the CE standard - Heiner Axmann reports. - This has saved us a lot of time and money.” A further advantage is the easier operation of the production cell, where the machine and the robot can be operated jointly from the central monitor of the machine’s control system.
DC technology in view
- Thin, thinner, thinnest - is Andreas Brüggemann’s answer to the question about current manufacturing trends. The requirements for thin-walled products are becoming more and more stringent, in particular for reasons of material efficiency.
The sustainability targets were also the factor that tipped the balance in favor of acquiring an injection molding machine with an all-electric drive. - Energy efficiency is now the most important criterion whenever we invest in new machines and technologies - says Heiner Axmann. - Especially for machines making packaging products, for which we require extremely fast movements and high injection speeds, energy efficiency is a decisive factor in reaching the required lowest possible costs per unit. The modern machines display the consumption figures, so that we can easily compare them. Compared to a hybrid machine, the EcoPower Xpress consumes over 30 per cent less electricity when used with the same mold.
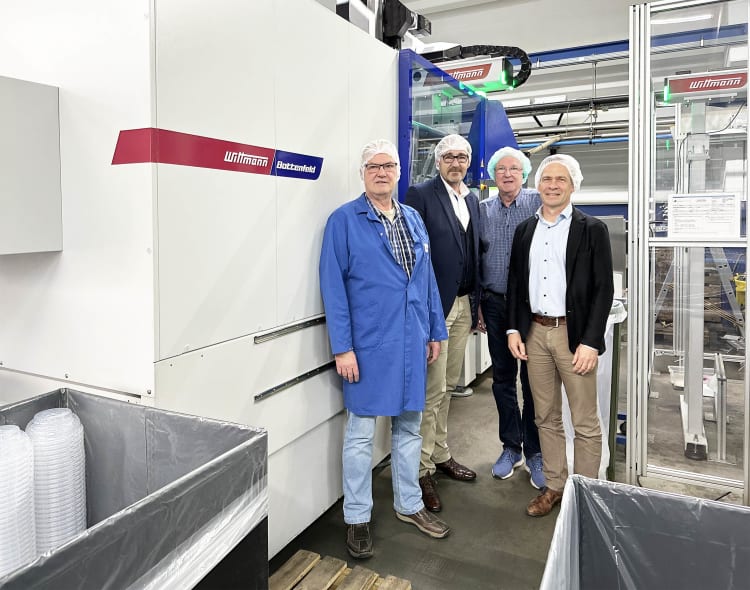
As a member of BVFE, the German Federal Association for the Promotion of Energy Efficiency, it is a matter of honor for Heiner Axmann to work meticulously on keeping energy consumption as low as possible in all corporate departments. Many actions to that effect have already been taken. - Over the last few years, we have reduced our total energy consumption by 1.5 million kWh - says Axmann. Most recently, the company’s photovoltaic system to generate its own electricity has been extended. Axmann is already discussing with Wittmann how the DC technology with a battery storage system presented at the Fakuma 2023 could be used at their own company.
- Wittmann is a family-owned company, like us, and that makes the difference - says Heiner Axmann. - We very much like working with family-owned companies, since they take a different approach. They are more dedicated in counseling as well as in service. They seek genuine partnerships rather than mere profit maximization. They want us to be satisfied customers.
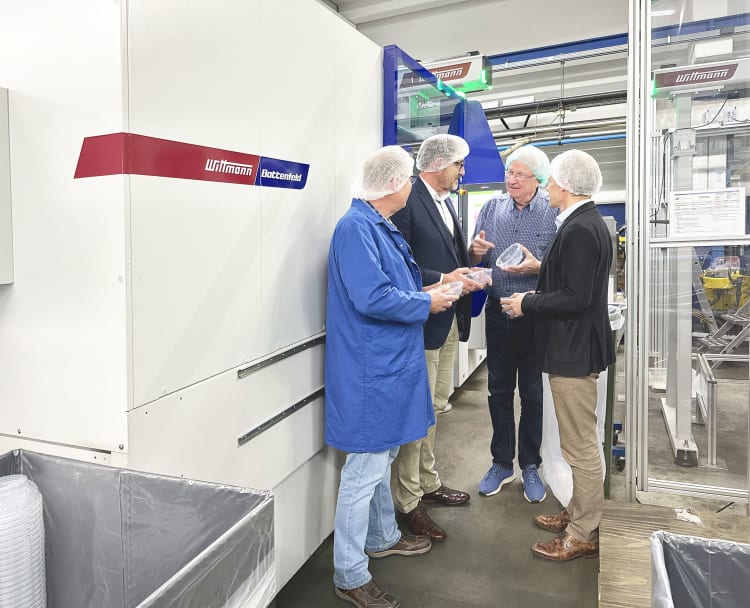