Energy-efficient plants
Sustainable product solutions need smart production processes that increase energy efficiency during production, lower carbon emissions in the long term and reduce material and resource consumption. Digital interconnectivity and monitoring help optimise product quality and plant availability.
Next generation bottle fillers, for example, require up to 20 percent less energy, and at the same time reduce carbon emissions by up to 50 percent – all thanks to optimised vacuum pumps. “We have installed pressure sensors in every single filler valve. These sensors seamlessly identify any deviations from set values as well as breakages,” says Manfred Härtel, Product Manager Filling at KHS, explaining the automated processes used in the Innofill Glass DRS bottle filler. A camera-assisted controller monitors the high-pressure injection system and regulates the development of foam, which in turn reduces product losses by up to 50 percent. The use of process warmth combined with a lower water consumption during cleaning also have a positive impact on the machine’s energy balance and reduce production costs.
Artificial intelligence
At the end of 2019, the Ende group introduced the prototype of a self-learning filling valve to the public. Aided by artificial intelligence, the valve is expected to optimise the production process whilst at the same time significantly reducing operating and maintenance costs. “To achieve this, we have developed cyber-physical systems that allow the valves themselves to find the best way to fill a certain container with a certain beverage – in the most efficient manner and as quickly as possible,” says Jochen Ohrem, Expert of R&D Management at KHS, explaining the new development. When learning, the valve focuses on self-configuration, analysis, self-diagnostics and, finally, self-optimisation.
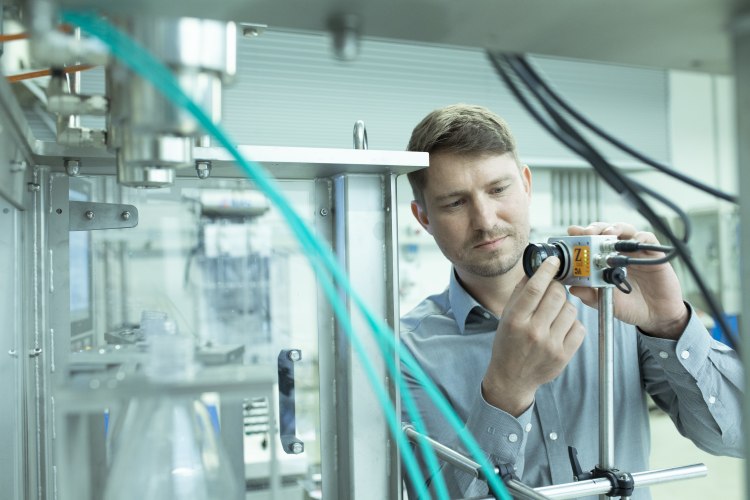
A camera controls the impact of bubbles and foam during the bottling process, which helps prevent product losses. Photo: KHS GmbH
Augmented Reality
interpack exhibitor Krones AG also uses viable technologies. The German group offers its customers 24/7 support provided by service specialists, using remote support to troubleshoot and resolve problems should unscheduled downtimes and short-term difficulties occur. In addition to conventional support by phone, plant operators can also request augmented reality support. This option uses smart glasses, which give the support specialists virtual, on-site access.
However, Krones banks on prevention to ensure that one day, downtimes will be a thing of the past. The data-based system is able to identify and resolve weaknesses in the production process at an early stage. Support specialists continuously monitor the production process; they access the machine’s data from the outside, notify users of emerging problems in due time and guide plant operators through the troubleshooting and resolution process should worst come to worst.
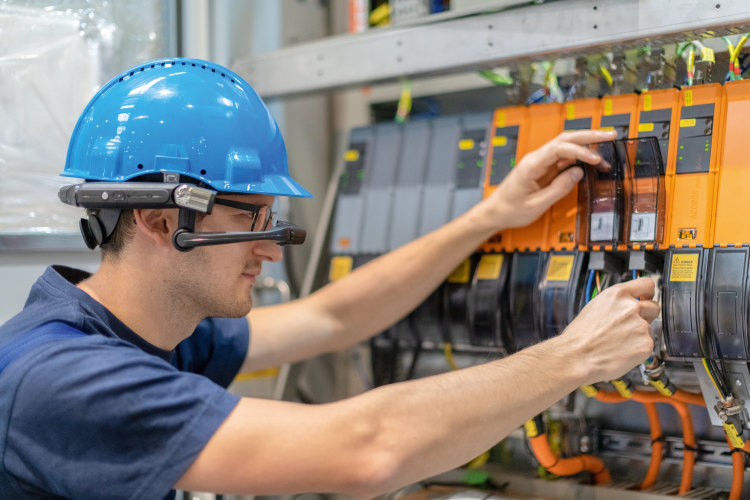
Augmented reality support: Smart glasses provide immediate support when plants malfunction. Photo: Matthias Jeserer, Krones AG
Autonomous production is the future
Innovations like these, and the many others that will be exhibited at interpack 2020, prove that smart factories are no longer visions of the future but are already a reality today.
We do not need a crystal ball to predict that cyber-physical systems (CPS) will be a dominating presence in the future of beverage production. Unaided by humans, these systems independently control production and processes, share information among one another, and plan and trigger actions independently. This is certain to affect operation processes in companies, but it won’t stop there. We can expect this new technology to include partners, suppliers, warehouses and customers, which will all be connected to one another.
Author: Melanie Streich
[1] Beverage Industry Analysis [Branchenanalyse Getränkeindustrie], Stefan Stracke and Birte Homann, 2017 Hans Böckler Foundation
[2] https://www.coca-cola-deutschland.de/stories/welche-nachhaltigkeitsziele-hat-coca-cola
[3] Chemical recycling