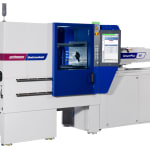
Following a year of “Fakuma break”, the Wittmann Group is now looking forward to presenting itself again live on site in Friedrichshafen and showing its product highlights at booth 1204 in hall B1. But this time, “live” is more than just being there on site. In addition to the exhibits to be viewed physically, Wittmann will also offer the opportunity of live connection with its various facilities via its new media technology Wittmann Interactive to obtain information about additional exhibits.
Highlight SmartPlus
The highlight of this year’s presentation by Wittmann Battenfeld is the new SmartPlus. The SmartPlus is a servo-hydraulic machine which stands out by its high level of cost and energy efficiency, as well as repeatability. Thanks to the use of proven technologies and carefully selected options, short delivery times and an excellent price-performance ratio have been made possible for this machine.
A special feature of the SmartPlus is the new B8X control system with system components developed in-house. These enable a higher frequency, shorter response times and a higher repeatability rate for parts, with the same operating comfort as before and the familiar visualization concept. Of course, the SmartPlus also offers the KERS energy recovery technology originally developed for the EcoPower.
The SmartPlus is currently undergoing practical tests at selected customers. From the 4th quarter of 2021 onwards, the machine is expected to be available in a first series with clamping forces ranging from 60 to 180 t.
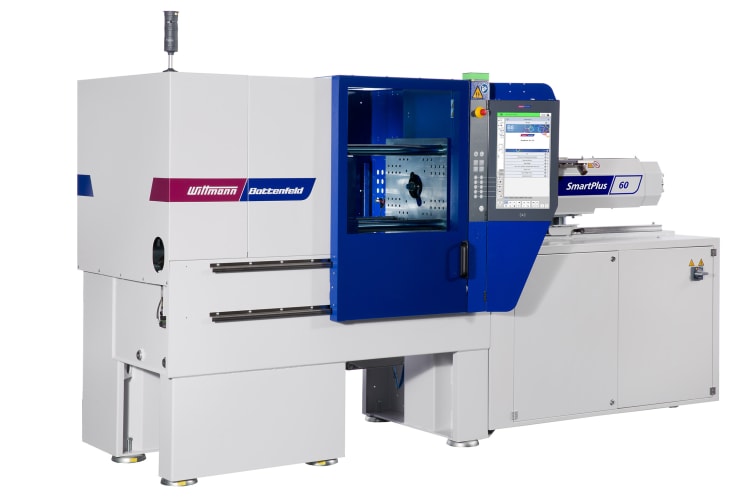
SmartPlus 60
The advantages of the new SmartPlus will be demonstrated on a SmartPlus 180/750. This machine is equipped with the HiQ Flow® application software, the new CMS-Light condition monitoring system to monitor an extended range of service-relevant machine parameters and a GRAVIMAX G14 gravimetric blender. The automation system, using a PRIMUS 26T robot from Wittmann, is implemented via an Easy Cell developed and manufactured by Wittmann Battenfeld Deutschland in Nuremberg. The Easy Cell mounted on castors requires no safety gate and thus takes up only a minimal amount of space beside the injection molding machine. In spite of its compact design, customers receive the complete range of CE-compliant safety features.
On the SmartPlus 180/750 a hub-cap for lawn mowers will be manufactured from PP, using a mold supplied by Uralan, Germany. In the interest of sustainable manufacturing, the part will be produced from a mixture of virgin material with regrind. The HiQ Flow® software will be used to ensure adequate parts quality. This is a material viscosity-related injection control system to compensate the effects of temperature and batch fluctuations on the viscosity of the material.
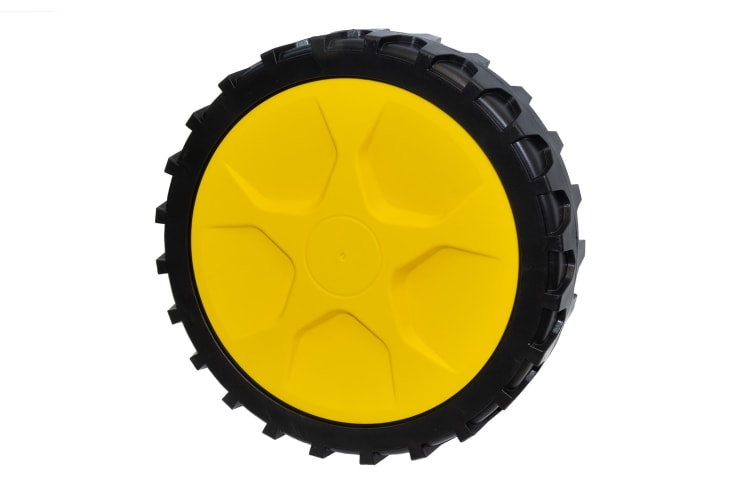
Hub cap for lawn mowers, produced on the new SmartPlus 180
Medical application on EcoPower 55 production cell
With the production of a hose clamp for medical technology in an 8-cavity mold supplied by WILAmed, Germany, Wittmann Battenfeld will demonstrate its digitization expertise. The machine to be used is an all-electric EcoPower 55/350, equipped with the software packages HiQ Flow® for compensating viscosity fluctuations, HiQ Melt for material quality monitoring and HiQ Metering for active closing of the check valve.
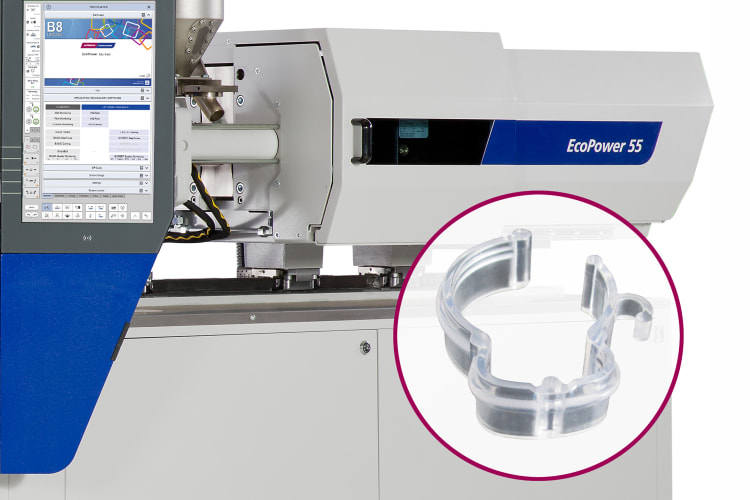
Hose clamp for medical technology, produced on an EcoPower 55/350 Wittmann 4.0 production cell
Equipment integrated in the machine’s UNILOG B8 control system via Wittmann 4.0 will include a Wittmann W918 robot, an ATON plus H30 segmented wheel dryer and three temperature controllers from the TEMPRO plus D series, as well as the TEMI+ MES system. The electronic mold data sheet will also be used by UNILOG B8. It enables the production cell, integrated via a Wittmann 4.0 router, to check whether the connected auxiliaries are sufficient for the selected product data set, or whether additional equipment is needed. In this application, too, the automation will be installed by way of an Easy Cell from Wittmann Battenfeld Germany.
LSR application on MicroPower 15/10H/10H Combimould
Wittmann Battenfeld will show its expertise in the area of LSR processing as well as injection molding of micro parts at the Fakuma by manufacturing a support ring with a silicone membrane made of PC and LSR on a MicroPower 15/10H/10H Combimould.
This multi-component version of the MicroPower comes equipped with two injection units in horizontal configuration and a rotary disc. The machine is laid out for clean-room injection molding. The rotary disc is completely encapsulated. All connections for heating aggregates, temperature sensors, water tempering, core pull pneumatics and sensors, as well as the blow-off valve, are mounted on the rotary disc. The connections to the mold have thus been kept short to enhance the machine’s user friendliness. As in the standard machine, the injection units of the multi-component MicroPower also take the form of two-step screw-and-plunger aggregates with a shot volume of 4 cm³, which enable processing of thermally homogeneous melt with minimal flow paths to achieve excellent parts quality.
The materials used to make the support ring presented are polycarbonate (Macrolon) from Covestro and a self-adhesive LSR (Silopren) supplied by Momentive. The mold has been constructed in cooperation with Nexus. The LSR dosing unit comes from Nexus and is equipped with a new Servomix dosing system including an OPC-UA interface (Euromap 82.3).