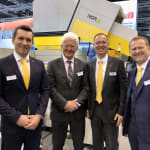
K 2022 was a complete success for Next Generation Recyclingmaschinen GmbH (NGR). In addition to numerous completed orders, a great deal of global interest in the innovative PET recycling process of the Upper Austrian machine builder was generated. More and more brand owners worldwide rely on the LSP technology of Next Generation Recyclingmaschinen GmbH for the processing of post-consumer PET.
K trade fair was a great success for NGR
Driven by the mission statement "working for a better future", Next Generation Recyclingmaschinen GmbH presented its future-oriented technologies in the market segments Post Industrial Recycling, Post Consumer Recycling and PET Improvement at this year's K trade fair.
During the eight days of the fair, a large number visited booth C21 in hall 9 to experience the future of plastics recycling live. From the first to the last day of the trade show, the machine builder enjoyed enormous interest in their highlights and scored a success all along the line. "K 2022 was a complete success for us. The interest of trade visitors in our technologies was enormous,” says a delighted Gerhard Ohler, CEO of the company, confirming that this interest resulted not only in a large number of inquiries, but also in an equally considerable number of orders in all three market segments.
K trade fair as an industry barometer
As the world's leading trade show, this year's K trade show was once again the industry barometer for current trends and future developments in the plastics industry. Every three years, industry and research from all over the world present the standards of tomorrow in Düsseldorf.
For Günther Klammer, CTO of NGR, the current developments in the industry are very pleasing: "Worldwide, more and more brand owners are focusing on the standards of tomorrow and are using our LSP technology for the processing of post-consumer PET. We are finding that Liquid State Polycondensation is a real game changer in PET improvement and is rapidly gaining popularity due to its better energy efficiency and outstanding cleaning performance. We believe it will soon become the widely accepted standard for bottle-to-bottle PET recycling."
Liquid State Polycondensation: new dimensions in PET processing
NGR has been the leading manufacturer of LSP technology for years. Back in 2011, the machine builder decided to take a new approach to PET recycling. With the LSP process, a completely new way of processing PET waste back into food-grade material using an extremely efficient process was developed under the product name P:REACT. While conventional PET processing methods change the material properties in the solid phase of the plastic, requiring many hours, the decontamination of the material in the LSP process takes only minutes. In the LSP process, all impurities are removed from the PET melt while still in the liquid phase, which guarantees simultaneous upgrading of the plastic and recycling to the highest standards of the brand owners.
In direct comparison to conventional systems, NGR's LSP process offers an energy-efficient and, in terms of melt quality, better physical cleaning process.
With this innovative process, the company exceeds the regulatory requirements in the direction of food suitability many times over and further upgrades the product quality of the recycled PET much better than the existing technologies.
FDA and EFSA confirm: Limit values far undercut
Approvals by the FDA (Food and Drug Administration - USA) and the EFSA (European Food Safety Authority) certify that the LSP-Process is the most suitable recyclate for 100% contact in food packaging.
In addition to the high mobility of the molecules in the liquid phase, the enormous surface area of the material strands contributes to the extensive cleaning. As a result, the quality of resulting material far exceeds the safe limits set by EFSA and FDA.
Due to the extraordinary cleaning performance, the processed PET can be recycled many times with no disadvantages, thus saving further valuable resources compared to Virgin PET or energy as with other packaging materials such as glass or aluminum.
Through years of experience: one step ahead
While other manufacturers are now also working on LSP solutions for PET processing, the specialists from Upper Austria have already sold more than 50 systems in over 20 different countries and gained the critical experience and process knowledge in the process.
"Of course, it was initially a big risk for us to rely on a different technology," Günther Klammer notes. "But we always believed in success and have learned a lot over the years. We are now in a position to offer mature and completely developed solutions for our customers. Whether for film production, spun yarn production or beverage bottle preforms, our systems are running and we are thus a decisive step ahead," explains the CTO.
"Anyone who wants to set tomorrow's standards today and benefit from our many years of experience in PET recycling should opt for a system from Next Generation Recyclingmaschinen GmbH," the trio of managing directors, consisting of CEO Gerhard Ohler, CTO Günther Klammer and COO Erich Fürst, emphatically agree.
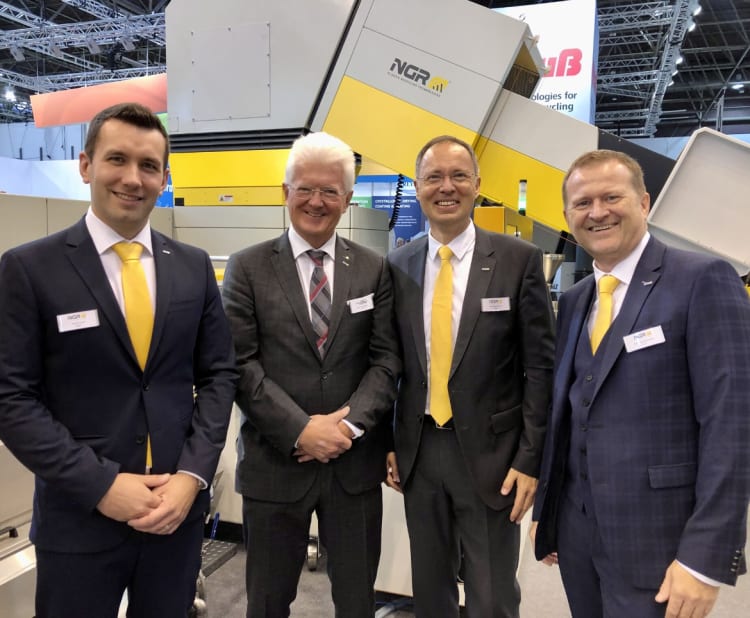
trio of managing directors with owner Josef Hochreiter