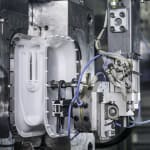
Founded in 2014 and located in Kartuzy near Gdańsk, SolidPlast has made a difference by strategically implementing digital assistant systems. In an increasingly competitive market, the company relies not only on modern injection moulding machines but also on smart process control - foremost among these are the digital assistant systems from ENGEL. With the digital assistant iQ hold control, the company has now succeeded in further reducing production costs.
With 17 injection moulding machines, SolidPlast produces technically sophisticated plastic parts, including for companies such as Aptiv, Avery Dennison and Apator-Metrix. The challenge: high component quality, short cycle times, maximum energy efficiency - all under continuously increasing cost pressure.
The Challenge: Cycle time reduction while maintaining consistent quality
A specific project prompted the introduction of iQ hold control. In 2022, a long-standing major customer commissioned SolidPlast with the series production of a new component - a gas meter housing made of POM. The specifications were demanding: a short cycle time, high dimensional stability, and reproducible quality. At the same time, the company did not have machines on site with sufficient clamping force to conventionally use the large tool.
The solution involved a combination of experience, smart machine design, and digital tools. After a thorough evaluation, SolidPlast opted for the use of an ENGEL victory 220 - a tie-bar-less, space-saving, and precise machine. With iQ clamp control, the actually required clamping force was calculated and successfully confirmed. The system measures the so-called mold breathing and optimally adjusts the clamping force.
"We were on the edge, but it worked - thanks to digital support, we were able to safely proceed with series production," recalls Dariusz Barton, CEO of SolidPlast. Yet, the real challenge was still to come: The required cycle time of under 50 seconds was initially unattainable - even with process optimization, it remained at 53 seconds.
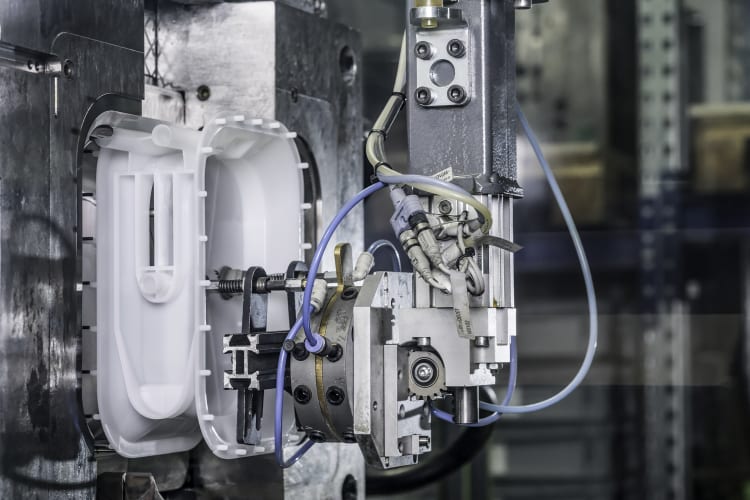
iQ hold control: Digitally determined sealing point.
In the spring of 2023, ENGEL offered the company a new option: the use of iQ hold control, an intelligent assistant system that optimizes the holding pressure time of the injection moulding process. The software monitors the material solidification in the component in real time and automatically adjusts the holding pressure time to avoid unnecessary hold times.
"After the installation, we conducted initial tests with ENGEL. The result surprised us: the holding pressure time was reduced from 14 to just 9.5 seconds - a saving of 4.5 seconds," said Barton. This reduced the total cycle time by 4.2 seconds, which corresponds to an improvement of around 10 percent.
The effects were immediately measurable: SolidPlast achieved an improvement in machine utilization with 11% more output in the relevant production. "This means an additional production capacity of about 20,000 parts per year for us - without additional machines," Barton further explained.
Quality, economy, and sustainability in balance
Typically, a shortened cycle time entails risks, especially regarding component quality and dimensional accuracy. However, this is precisely where the advantage of intelligent process management is evident. "Usually, too short a holding pressure time leads to warping or missing filling areas. This problem, however, is actively prevented by iQ hold control by monitoring material consolidation," explains Dawid Stefański, technical supervisor at SolidPlast.
The result: no loss of quality, stable processes - and a cost reduction of about 4.2 percent in series production. SolidPlast even passes on part of the savings to the customer - a prime example of lived partnership.