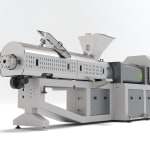
Plastic recycling is a central driver of the circular economy. With innovative, practical solutions, MAS creates real added value for efficient, sustainable recycling and upcycling of various plastic fractions. Our advanced extrusion technology significantly revolutionizes existing recycling processes, offering a comprehensive range of energy-efficient, resource-conserving products and lines.
But what is the difference between single-screw and twin-screw extruders in plastic recycling? And how can customized MAS solutions provide valuable impulses to the circular economy?
The difference between single-screw and twin-screw extruders
MAS offers a wide range of state-of-the-art, multifunctional extruders characterized by compact design, large feed openings, and energy-efficient processing of various plastic fractions. However, not all extruders are the same: the difference between single-screw and twin-screw extruders primarily concerns the material to be processed and the desired end product.
Function of single-screw extruders
Single-screw extruders are suitable for processing homogeneous, pure materials. The polymer melts primarily through friction against the extruder wall. Throughput directly depends on the screw speed - a higher speed leads to more throughput. The quality of the end product (e.g., melting behavior, degree, and mixing effect) is solely influenced by the design of the extruder screw and is therefore only limitedly adjustable. While mixing processes are fundamentally possible with a single-screw extruder, they are limited and of lower quality.
How twin-screw extruders work
In contrast, twin-screw extruders are significantly more versatile. Throughput is primarily determined by material dosing, while the screw speed can be freely selected within a broad range. A higher speed results in more energy input, enhancing the mixing effect and increasing the melt temperature. If a product requires particularly gentle processing, this can be easily achieved by reducing the screw speed.
Functionally, twin-screw extruders - so-called compounders - are ideal for processing complex formulations, such as combining different material streams (e.g., plastic, fillers, color masterbatch). They are particularly suitable for demanding and high-quality applications. While single-screw extruders are designed for simple, pure input fractions, twin-screw extruders are often used when higher quality is required, such as in film production, where the highest demands on the purity and homogeneity of the granulate must be met (e.g., avoiding gels in transparent films).
MAS extruders in the circular economy
In the circular economy, extrusion is an essential processing step: from the collected end product (e.g., used packaging), a high-quality intermediate product - the granulate - is produced.
Initially, the material must be dried, as residual moisture can negatively affect the granulate quality. This is done either by pre-drying before or by degassing during extrusion. Since input materials are often impure and contaminated with foreign substances (such as aluminum, wood, labels, straw, paper, or sand), significant technical effort is required to achieve a high-quality end product. The removal of these contaminants is accomplished through melt filters.
An example of an efficient circular economy is the PET bottle: it is already possible to produce new food packaging from used bottles (“bottle-to-bottle” recycling).
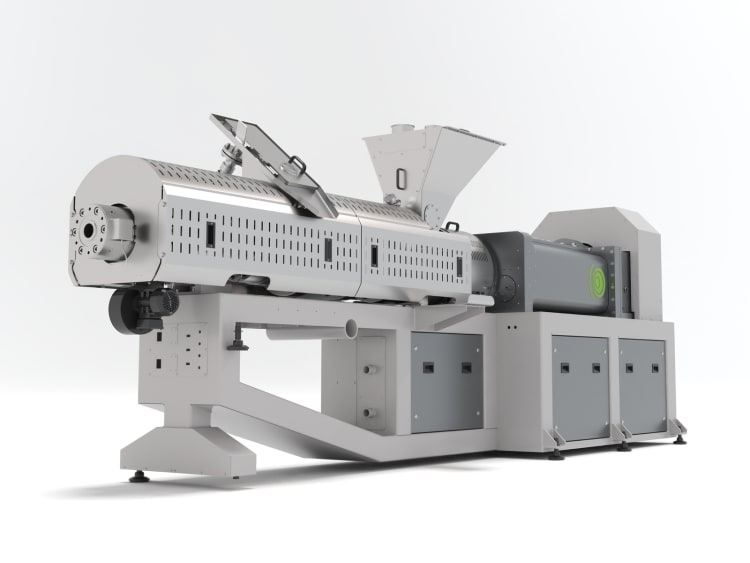