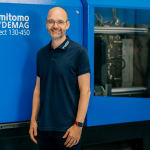
Interview with Dr. Thorsten Thümen, Senior Director Technology at Sumitomo (SHI) Demag.
The rapid development of digital technologies has widely opened the gate to the era of the so-called Industry 4.0. What impact does digitalization have on the injection molding machine industry and how has it changed the approach to injection molding processes?
Ultimately, this is the consequence of the past years. Injection moulding or the injection moulding process has long been regarded as a holistic production cell, with the knowledge that only the perfect interaction of all components leads to success. The many years of effort with regard to data exchange between the injection moulding machine and all the peripheral devices involved via the EUROMAP/OPC-UA standards is now paying off. Because we create transparency about the process status via the data. The next steps are to build artificial intelligence on the basis of this data with the aim of achieving higher overall availability (e.g. through assistance systems, preventive maintenance functions, regulation of process fluctuations, etc.).
But these are still the beginnings of advanced digitalization and, generally speaking, the level of maturity in terms of the digitalisation of injection moulding processes is still heterogeneous.
Sure. We are still at the beginning of the road and still have to test and validate many topics in everyday industrial life. But the possibilities are promising and a variety of technologies are available. The important thing is for each individual to deal with the topic step by step. The first step is always to ensure a clean infrastructure for data acquisition.
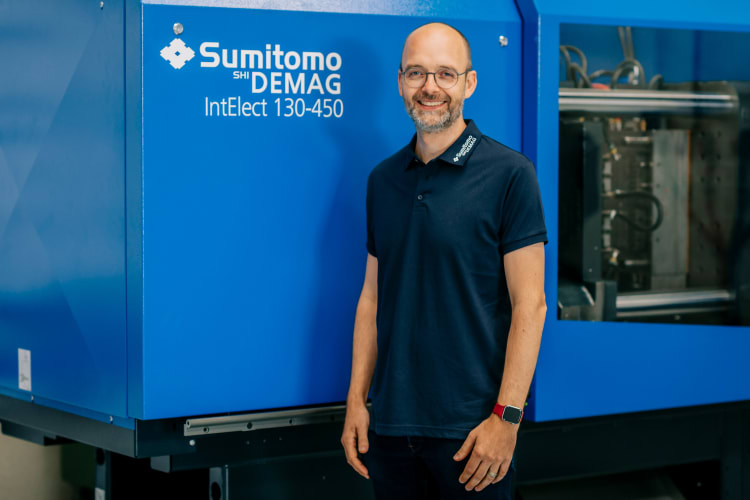
This is the first step towards transparency. Building on this, the next steps follow, depending on which objective is important for the final step. The important thing here is to start simple and then work on it continuously. This is how you successfully reach your goal. Wanting everything at the beginning ends in a complexity that is almost impossible to control.
Well, let's say what doors digitization opens - what specific opportunities it makes available.
As already mentioned, it brings a high degree of transparency with regard to the production conditions. This transparency leads to new insights and higher productivity. As we have more data available and easy access to it, challenges can be solved more quickly - be it process fluctuations, technical problems and help on site or via the internet.
As injection molding processes become more digitized, the amount of data increases. Data contains a lot of information but this is often not recognisable at first glance. How does using this information support processes optimization?
The injection moulding process has many unique characteristics. Because of this, deviations or discontinuities can be easily detected automatically. This can be made usable in the first step through good visualisation and key figures. We can pursue two different approaches. On the one hand, trend monitoring via the known, cyclical characteristic values. From these trends, creeping process adjustments can be automated. E.g. the readjustment of changeover points depending on the progressive wear on the non-return valve. The second approach is to analyse the curves in the process and thus react to process fluctuations at short notice and thus reduce rejects - these can be, for example, dosing fluctuations caused by problems in the material feed or similar.
For the full potential, however, more advanced techniques from statistics or AI methodologies are necessary. If additional information, for example on part quality, is added by the process engineer, further dependencies are formed. This makes it possible to identify links or dependencies that can only be recognised at second or third glance or only by very experienced people.
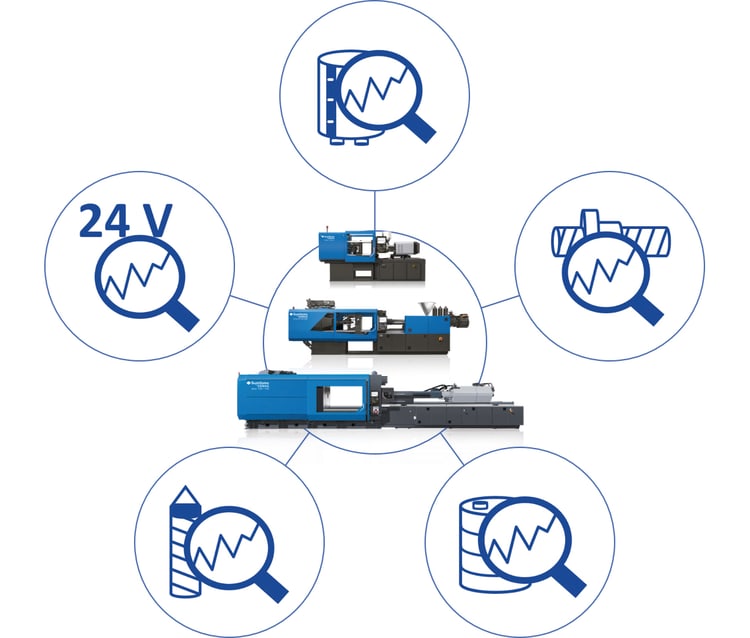