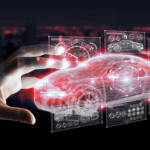
The specialty chemicals company Lanxess sees great application potential for its technical plastics under the brands Durethan (polyamide) and Pocan (polybutylene terephthalate) in the New Mobility growth market. This is why the High Performance Materials business unit founded the “e-Powertrain team”, which is geared to the needs of the global automotive industry and supports external partners throughout the entire development chain for components of electric vehicles and the associated infrastructure. This support includes materials that are tailor-made for specific customers and applications as well as processing development and engineering services for component design such as CAE simulations, moldflow calculations and finished product inspections.
The new group is the central point of contact for electromobility development projects and inquiries from all regions. “We coordinate knowledge exchange among our application and processing development centers, which we operate in all of the world’s major economic regions. The aim is to provide our international partners with the best possible products and service locally. We are also responsible for close-to-production and advance development projects,” explained Julian Haspel, who heads the team.
90 percent of all new vehicles electrified by 2035
It is estimated that far in excess of 120 million vehicles will be produced in 2035. According to studies conducted by Lanxess, around 90 percent of those will be electrified - equipped with either a mild-hybrid drive, plug-in-hybrid-drive or fully electric drive. However, around 80 percent - the vast majority - of newly registered vehicles will still have a combustion engine. “We expect both increasing vehicle electrification and the trend toward autonomous driving to entail a sharply rising demand for polyamides, polyesters such as PBT and continuous-fiber-reinforced thermoplastic composites,” said Haspel, looking ahead.
New mix of properties needed
Above all, the main properties of the plastics used in components such as electric drives include low flammability, good thermal conductivity and, increasingly, electromagnetically shielding behavior. In addition to high strength, rigidity and toughness values, good electrical properties such as high creepage current resistance will still be needed. Furthermore, conductive components must not be prone to electrical corrosion – at least as far as this is possible. Taken in isolation, all these properties are nothing new for plastic applications in electrical engineering and electronics. To meet New Mobility requirements, however, these sometimes mutually exclusive requirements have to be combined. “Thanks to our many years of doing business with the E/E and automotive industries, we already have materials that conform to the most important global standards and standards of the E/E sector and are also used in vehicles,” said Haspel. “We are also constantly working on new formulations to meet customer requirements.”
Collaboration on setting norms and standards
The requirement profiles for many applications in electric vehicles are either still under discussion or vary among countries, automotive manufacturers and suppliers. Haspel: “We work together on projects with our partners from the automotive and E/E industries to influence the definition of new standards, and we utilize our experience with both sectors for that purpose. Our customers benefit from that.”