A clean and energy-saving solution
The demands placed on recyclate quality and throughput are increasing. Energy costs are to be reduced. Overall, these are no easy tasks considering the rising energy costs and the fact that plastics are increasingly extracted from waste streams, meaning that heavily contaminated input materials are finding their way into plastics recycling more and more. Lindner provides the solution to these challenges with no less than two new products: the patented Rafter-type pre-washing system and the new EcoDry thermal dryer. ‘Purity, throughput performance and energy savings – these are the topics currently occupying our clients and that’s why we are displaying two product innovations at K 2022. The new EcoDry thermal dryer achieves energy savings of up to 30% thanks to cleverly used heat exchangers and sustainably insulated material handling components. Having a residual moisture of <1%, the materials achieve a particularly high degree of drying, which means that the flakes are better prepared for the subsequent process,’ explains Harald Hoffmann, Managing Director of Lindner Washtech, Lindner’s subsidiary specialising in plastics recycling. ‘We are also presenting another production innovation: our patented Rafter-type pre-washing system. By using a larger rotor, the dwell times can be increased, cleaning the material to a higher standard. Additionally we were able to sustainably increase the throughput – 3 t/h for films,’ says Hoffmann, pleased.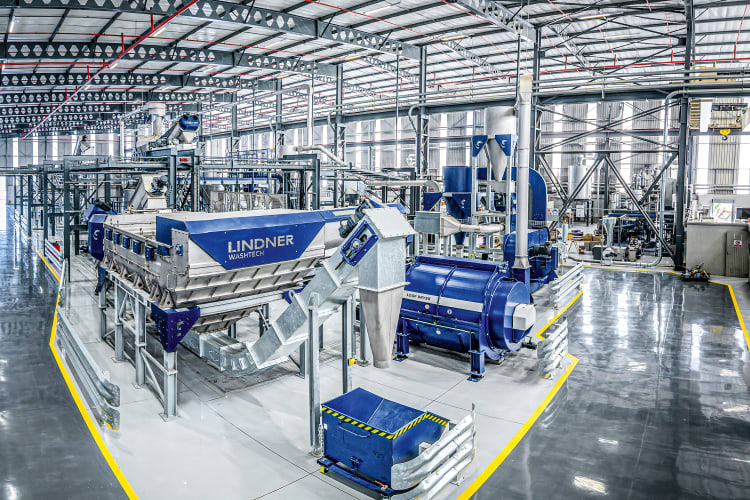
From homogenous flakes to immediate injection moulding
As part of the VDMA Circular Economy Forum, Lindner once again showcases its products in the outside area at K 2022, this time with three live demonstrations daily. The new Micromat HP shredder, the Twister friction washer and the mechanical Loop dryer demonstrate the process stages of shredding, washing, drying and water treatment using post-consumer rigid plastics. As a special highlight, the shredding of post-consumer plastics, called dolly pallets, provided by Engel, takes place daily at 4.30 pm. Together, Lindner and Engel show how, with a residual moisture of <1% and a uniform particle of 8 mm, homogenous and clean plastic flakes can be directly processed further in a two-stage injection moulding process. ‘This will open up many different possibilities for our clients,’ explains Michael Lackner, Managing Director at Lindner Recyclingtech. ‘Until now, injection moulders have bought granulate. Now they also have the option of purchasing and processing clean plastic flakes – as long as the parameters fit. Besides a specific particle , a low residual moisture content is particularly crucial. These are exactly the requirements we meet with our recycling solutions,’ emphasises Lackner.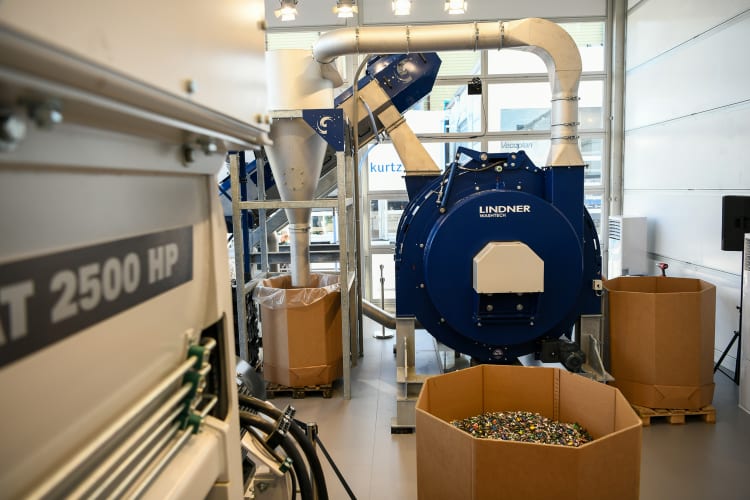
New precious materials from ocean waste
In partnership with other plastics recycling leaders, visitors can also learn more about the Atando Cabos project in Lindner’s outside area. The company Comberplast in Chile clears the coasts of broken fishing nets and ropes, turning them into new products such as crates for tulips or a well-known brewery. A demanding shredding task, considering that fishing nets and ropes are designed for robustness and durability and that the collected materials contain many abrasive substances such as stones and sand. Lindner’s Micromat was commissioned remotely in 2020 during the pandemic and has been supporting Comberplast in the daily production of new precious materials ever since.
Visit us at:
Hall 9, booths B17 & B19
Circular Economy Forum in the outside area CE-02