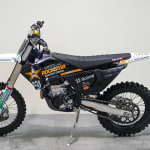
With its many years of experience in injection moulding and its high level of automation expertise, ENGEL develops highly cost-effective production concepts for the manufacture of composite parts in large quantities. At JEC World 2024 from 5 to 7 March in Paris, France, the machine manufacturer - headquartered in Austria - is demonstrating how high production efficiency and cost effectiveness can be combined with sustainability for both the aerospace and automotive industries.
In the ENGEL organomelt process, thermoplastic fibre composite preforms - for example thermoplastic sheets and UD tapes - are formed and functionalised in a single integrated process step. For example, reinforcing ribs or assembly elements are moulded immediately in the same mould after thermoforming using a thermoplastic from the same matrix material group as the thermoplastic sheet. This not only enables a highly efficient and fully automated production process, but also contributes to the circular economy. The consistent thermoplastic mono-material approach facilitates subsequent recycling of the parts.
At its stand in Paris, ENGEL will be demonstrating the huge potential of organomelt lightweight technology with a live machine exhibit. An ENGEL victory 660/160 injection moulding machine and an ENGEL easix articulated robot are being used to automate the production of inspection flaps for the fuselage of passenger aircraft. The production cell also includes an IR oven, which also comes from ENGEL in-house development and production.
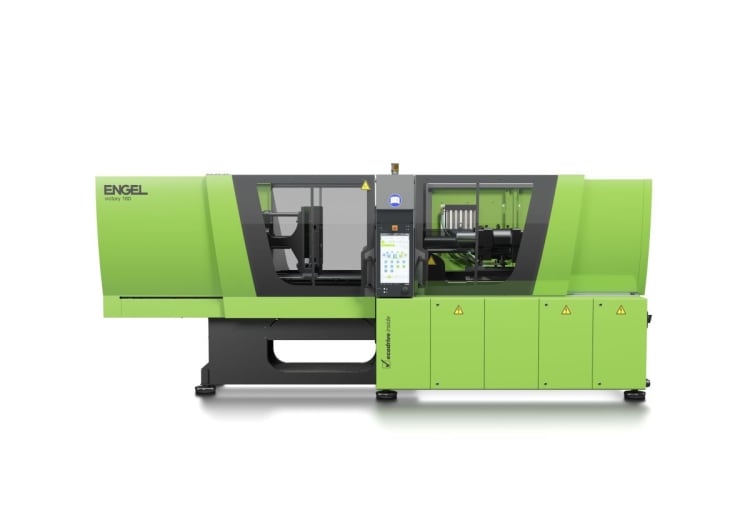
To enable a sustainable and cost-effective process, a composite material with a recycled long-fibre core is used in combination with fabric-based cover layers. To ensure that the part can be recycled in the best possible way, care is taken to ensure that the organic sheet and injection-moulded structure are of the same type.
The thermoplastic sheets are heated in the IR oven, taken into the mould by the robot, formed in the mould and immediately overmoulded. The reinforcement ribs and a mounting clip are formed.
Heating up the thermoplastic sheet is a process step which determines the cycle time and is also relevant to quality. The thickness of the preform defines the heat-up and cool-down times. Heating up the material quickly without damaging it is important, as are short paths for transporting the heated thermoplastic sheet to the mould, to avoid the sheet cooling down again on the way to the mould and losing its malleability. This is where the tie-bar-less technology of the victory machine plays to its strengths. Barrier-free access to the mould area makes it possible to position the IR oven very close to the mould. And the robot can take the shortest path to the mould without working around interference contours. Both factors accelerate hot handling and ensure process consistency and high component quality.
In integrated ENGEL system solutions, the robot and the IR oven are integrated into the injection moulding machine’s CC300 control unit. This allows the entire process to be operated centrally using the machine display. Another advantage is that the injection moulding machine, robot and IR oven access the same database and precisely coordinate their motion sequences with one another. This reduces the cycle time in many applications.
ENGEL is showcasing the production of the inspection flaps at JEC World 2024 in cooperation with its customer FACC (Ried im Innkreis, Austria). The other project partners are Ensinger (Nufringen, Germany), Neue Materialien Fürth in Germany and Voidsy, based in Wels, Austria. The latter will be showcasing an ultra-compact system for contactless and non-destructive material and component testing using active thermography.
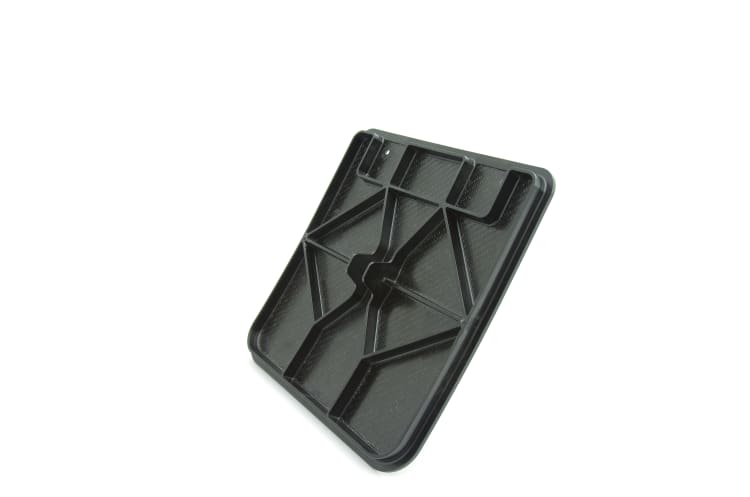
Great potential in all areas of mobility
In addition to the live exhibit on display, ENGEL and its Austrian partner KTM Technologies, based in Anif, Salzburg, will also be focusing on another aspect. On display will be a motorbike seat base produced using the newly developed tape sandwich process. This makes it possible to achieve a more compact part design with higher rigidity, lower weight and high cost efficiency.
"In the tape sandwich process, we work with very thin, single-layer reinforcement materials such as tapes and fabrics with a polypropylene matrix, which are inserted into both cavity halves of the injection mould without preheating before the cavity is filled with polypropylene," as Franz Füreder, Vice President Automotive & Mobility at ENGEL's headquarters in Schwertberg, Austria, explains. "Due to the specific mechanical properties of the sandwich structure, we can already meet the stiffness required for motorcycle seat bases with a single-layer UD-tape. This means that the tape sandwich process requires significantly less energy and simpler production cell technology than conventional fibre-reinforced plastic composite processing methods. At the same time, the production costs drop."
In the case of this technology demonstrator, the seat bottom, with identical stiffness, the nec-essary installation space could be reduced by 66 percent and the weight by about 26 per-cent. "The new sandwich structure, in which the reinforcing fibres are as far away as possible from the neutral fibre, offers maximum stiffness while minimising the number of fibres required," says Hans Lochner, Team Leader Material and Applications at KTM Technologies. Another advantage of the sandwich structure is that standard thermoplastics can be used in components exposed to high mechanical stresses, since the part performance is driven ex-clusively by the tape structure. And that boosts cost efficiency, too.
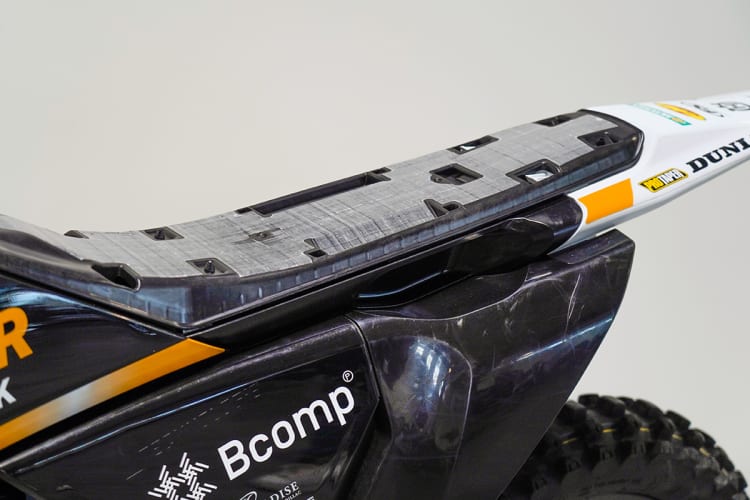