Reducing global warming potential by up to 85 percent
The development partners have tested a variety of injection moulding materials, including bio-based and recycled PP grades in addition to conventional PP from fossil sources. The global warming potential (GWP) was determined for the various material combinations. Compared to the series production version - a seat made entirely of fossil PP - the tape sandwich technology reduces the GWP by 27 percent when also using fossil PP. This value is achieved solely by reducing the material. Using polypropylene from renewable sources reduces the GWP value by 85 percent. The component weight was reduced by 26 percent in each case. This is possible because even very thin components achieve high stiffness.
The consistent single grade plastic approach also contributes to the reduction of greenhouse gases. In combination with tapes from a PP matrix, parts can be created which can be recycled at the end of their service life. "This new development sees us open up an affordable and sustainable solution for future mobility," Füreder emphasises.
The first step will be to set up tape sandwich technology for use in the KTM family of motor-cycles. Besides this, ENGEL and KTM Technologies have their sights set on many other lightweight applications in a wide range of mobility disciplines. The two development partners are offering the tape sandwich process jointly, and developing solutions tailored precisely to the specific use case.
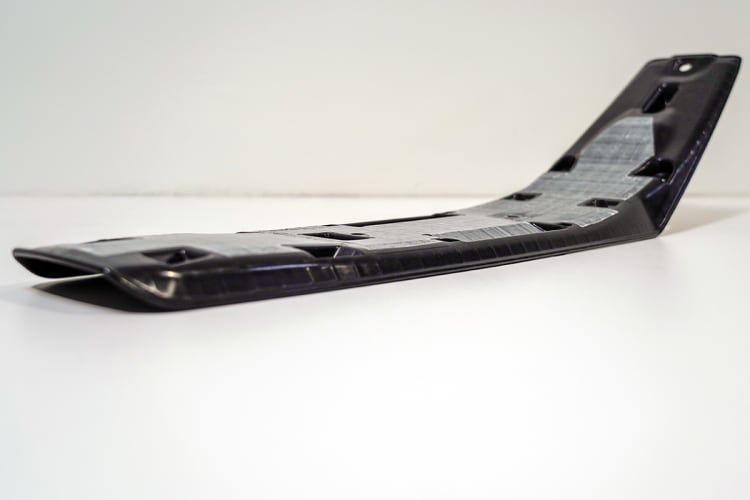
Reduced assembly overhead and labour costs
An Expert Corner focusing on automotive applications will also be dedicated to the ENGEL organomelt process. Among other things, the SPE Award-winning front-end module carrier by Lucid Motors is being showcased. Series production of the part is by ElringKlinger - headquartered in Dettingen an der Erms, Germany - and relies on the ENGEL organomelt. Depending on the vehicle type, the front-end module carrier acts as a support for the charge air cooler, the headlamp modules, the wash-water tank, the horn, the distance radar module or the air intake. It also supports the bonnet through add-on bonnet locks.ElringKlinger has succeeded in minimising both the number of pre- and post-processing steps as well as the costs, despite a total of 37 inserts. The extremely high level of functional integration in the injection moulding process results in lower assembly overhead, which, in turn, reduces labour costs. The front-end module carrier is used in the “Air”, the first electric vehicle model by US car manufacturer Lucid Motors.
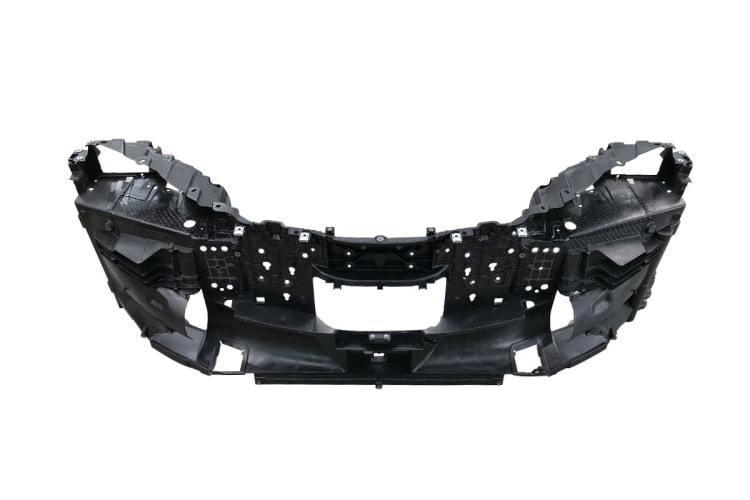
ENGEL at the JEC World 2024: Hall 5, Stand L106