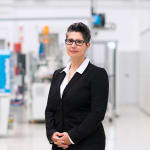
The potential of digitalization in injection molding production is nowhere close to being exhausted. Nadine Despineux, Vice President Digital and Service Solutions at KraussMaffei, sat down with PlastEcho for an interview. She talked about the opportunities and solutions available to make use of the advantages of Industry 4.0 and generate measurable added value for the customer. Artificial intelligence plays a groundbreaking role here.
The rapid development of digital technologies has largely opened the door to the era of what is known as Industry 4.0. What effects does digitalization have on the injection molding machine industry, and how has it changed the approach to injection molding processes?
The trend in our market is that traditional differentiating features such as price or technology alone are cited less frequently as the critical factors when buying a machine. Therefore, providers must actively look for new differentiating factors, where digitalization plays an ever larger role. The transformation from being product-centered to being customer-centered is critical here.
At KraussMaffei, being customer-centered is the focus of digitalization. This approach uses individualized customer communication according to target groups or personas. We have very different types of customer contact persons with diverging interests. Different target figures exist depending on whether we deal with the Head of Production, Head of Maintenance, CFO or CEO. When we take all these factors into account and develop customized digital services in conjunction with our state-of-the-art machines, we help our customers improve their business economics and market opportunities. This makes us an invaluable cooperation partner.
Here's a concrete example of how this influences the injection molding process: One of the success factors of our digital socialProduction product is the clear focus on the customer and collaborating with them – in every stage from the initial idea to field tests to optimizing the product. Using socialProduction, the production process of the injection molding machines is continuously monitored by a patented, self-learning process. Relevant anomalies and trends in the process are identified at an early stage based on all detected machine data and communicated proactively by means of user notifications. The process parameters are evaluated completely autonomously and without prior configuration by the process owner.
We are, after all, still in the early stages of progressing digitalization. Generally speaking, the degree of maturity with regard to the digitalization of injection molding processes is by no means uniform yet. What solutions does KraussMaffei offer?
You're right in saying that the degree of maturity of digitalization within various technologies and applications is still not uniform. Back in mid-2018, we at KraussMaffei launched the Digital & Service Solutions business unit as an addition to our three machine technology segments, Injection Molding Machinery, Reaction Process Machinery and Extrusion Technology. In addition, the traditional service business, including maintenance, spare parts, retrofits and training, has been linked to the development of new business units and the development of digital services. Accordingly, our digitalization is advanced compared to the rest of the industry.
As part of the transformation of the entire corporate structure, the operational business at KraussMaffei is currently based on two divisions. In addition to Digital & Service Solutions, the second division bundles the three machine segments and structures them into global functions and five regional units instead of product segments.
The basic objective of our realignment is to develop into a comprehensive solution provider focused on production efficiency and sustainability and placing the focus on the customer.
In doing so, we have endeavored to mesh both divisions closely in order to offer our customers added value over the entire product lifecycle. Within Digital & Service Solutions globally, we have adopted a structure that reflects end-to-end processes. Standardized and managed global processes are a basic prerequisite for being able to scale digital products and services.
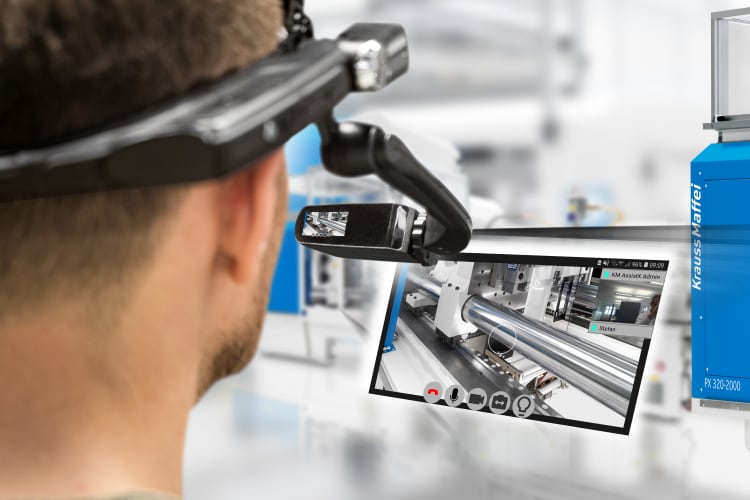
Despite this, one challenge for our customers is that production facilities usually have uniform equipment because different systems are purchased from different suppliers. Therefore, the objective must be to harmonize and standardize interfaces so that systems from different manufacturers and suppliers can interact and communicate with each other. The Euromap initiatives, which are based on OPC Unified Architecture (OPC UA), provide a state-of-the art, efficient communication standard with standards defined on a cross-manufacturer basis.
What doors, concretely speaking, does digitalization now open? What specific possibilities does it offer compared to the past?
Digitalization has increased the speed at which the market is changing. At its core, KraussMaffei is a mechanical engineering company with a longstanding tradition, and so it will remain for the foreseeable future.
However, the possibilities of digitalization bring about the danger that traditional mechanical engineering companies will have to compete with tech companies from unrelated industries, namely the software and Internet industries.
Therefore, we mechanical engineering companies have to combine our expertise in this domain with the expertise we have in digitalization. Today, this protects us from competition from data companies by adding more customer value than the pure software companies are able to deliver. This is the door we have to open.
Concretely speaking, digitalization helps us fill the vessel of customer-centricity with content and develop new, value-creating services for our customers. Ultimately, being customer-centered is a trade or craft that can be learned. Such expertise has to be developed in relevant organizational units. For this purpose, the digital world provides a well-stocked toolbox of digital technologies and methods for being customer-centric.
Digital solutions have already changed the service business in mechanical engineering, for example through remote-service solutions. Going forward, data-based solutions will also be the basis for predictive maintenance solutions. The technological prerequisites for this are already in place today.
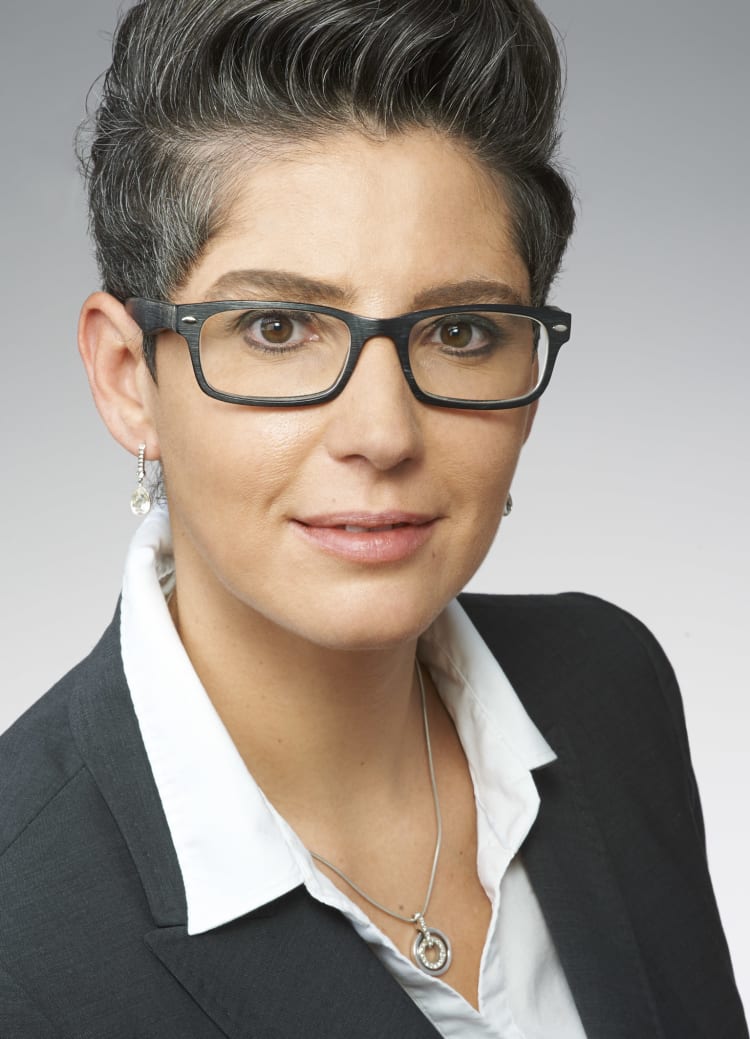
Nadine Despineux, Vice President Digital and Service Solutions at KraussMaffei