Reliable processing of recyclates
An Allrounder Golden Electric 470 E with a Yaskawa six-axis robot will be demonstrating how post-consumer recyclate (PCR) can be reliably processed. In a technically demanding process, toy dolphins will be made.
In turn, a vertical Allrounder 375 V machine will overmould inserts with single-variety post-industrial recyclate (PIR) based on a glass-fibre-reinforced PA 66/6 to produce ready-to-use bicycle tools. Tool cases in the Arburg design will be produced using components made from Arburg partner Leonhard Kurz's Recopound® material, which is obtained from post-industrial recyclate (PIR) on the basis of PET films. In addition, an ISCC mass-balanced material from Covestro will be used. The coveted give-away will be produced on a turnkey system based around a hybrid Allrounder 920 H with a clamping force of 5,000 kN.
Prime examples of digitalisation and automation
Arburg's stand will feature a wide range of automation solutions – from simple part removal with various linear Multilift robotic systems to complex handling with Yaskawa and Kuka six-axis robots.
The application example of a tyre lever will show how digitalisation and automation go hand in hand to produce plastic parts efficiently and with 100 per cent traceability. A turnkey system with a vertical Allrounder 375 V and a six-axis robot mounted in a space-saving hanging position will be producing this ready-to-use bicycle tool. The Arburg Turnkey Control Module (ATCM) Scada system and 'Invisible Tracing' from partner Detagto allow each product to be clearly traced and identified.
Efficient injection moulding processes
Energy-efficient two-component injection moulding will be demonstrated by an Allrounder More 1600, equipped with two electric injection units, which will produce a container made of thermoplastic (PBT) and liquid silicone (LSR). The LSR dosing unit from Reinhardt Technik is integrated into the Gestica control system via OPC UA and the Euromap interface 82.3.
As an energy-efficient, resource-saving application and alternative to thermoforming, an all-electric Allrounder 720 A Ultimate packaging machine will be producing IML round cups with a wall thickness of only 0.37 millimetres. This is done by injection compression moulding, which also reduces the energy requirement and mould wear.
An IML process designed specifically for medical technology will be presented using labelled centrifuge tubes as an example. In addition to Arburg, partners Kebo, MCC Verstraete, Beck Automation and Intravis are involved in this innovative joint project involving an electric Allrounder 520 A with an 8-cavity mould.
Industrial additive manufacturing
A high-temperature Freeformer 750-3X, Arburg's largest yet compact 3D printer, will be producing air diffusers from Ultem, original aerospace-approved plastic granules. An innovatiQ LiQ printer from for processing liquid silicone will also be presented from the ARBURGadditive division.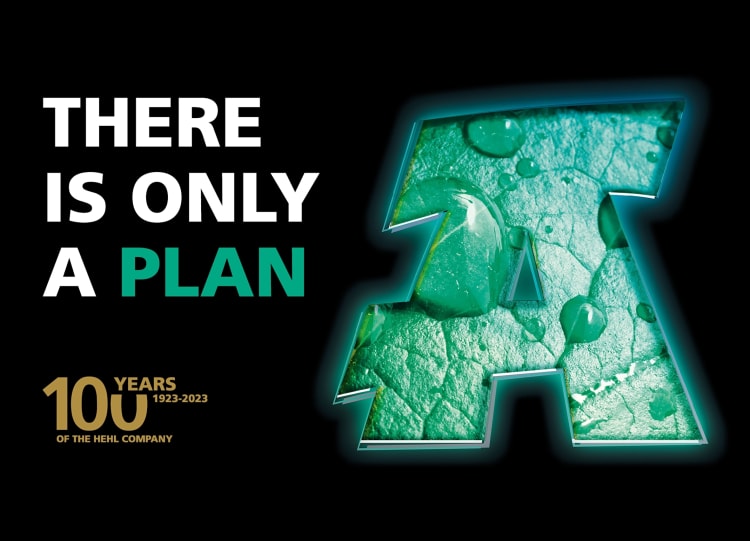
Arburg's 'Plan A' brings together everything the company has to offer on the topics of sustainability, digitalisation, automation and energy efficiency.
Ten additional exhibits on partner stands
Ten additional injection moulding exhibits on partner stands will demonstrate the wide range of applications for Arburg machine technology. These will include:- an Allrounder 1300 T rotary table machine that produces vegetable slicers by overmoulding metal blades with ABS (Maschinenfabrik Lauffer, Hall A3, Stand 3008),
- an Allrounder 470 H hybrid machine that uses an 8-cavity mould with a special laser surface to produce closure caps from recycled PP (Barnes Group, Hall A1, Stand 1208) and
- an electric Allrounder 370 A that processes solid silicone into cable ties (ACH, Halle A4, Stand 4307).