Saving resources and reducing weight with alternative materials plus ultra-modern equipment and process technology
With a MacroPower1100/12800 fitted with an energy-saving, speed-controlled servo motor and a constant displacement pump, Wittmann Battenfeld will produce an indoor panel which stands out by its light weight, using a single-cavity mold supplied by FRIMO, Germany. Here, Wittmann Battenfeld relies on using natural and recycled materials. The door panel consists of an extremely light mat made of natural fibers, onto which a map pocket made of polypropylene regrind from Borealis is over-molded. To achieve further savings in material input and weight, the patented Cellmould structured foam technology developed by Wittmann Battenfeld is used.
The reduction in material input thus realized benefits the environment in more than one way. Firstly, valuable resources are saved, and secondly, the parts are lighter, which reduces the car’s fuel consumption and/or extends the battery range in electric vehicles. In this application, the pre-cut natural fiber mats are picked up from a buffer stack and inserted into an IR heating station by a WX152 robot from Wittmann. Next, the heated mats are placed into the mold on the fixed mold half by a combination gripper (removal and insert gripper), formed, cut to and over-molded. Prior to insertion of the next natural fiber mat, the finished part and the trimmings are removed from the fixed mold half and subsequently transported to the storage position.
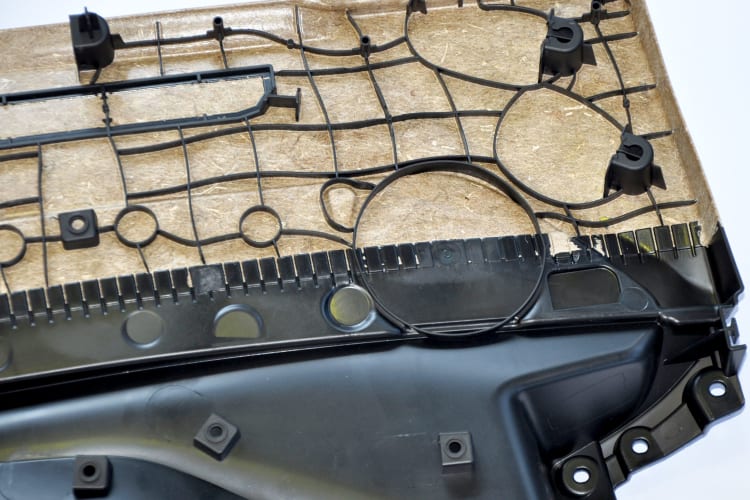
The MacroPower is equipped with the newly developed Wittmann CMS Lite condition monitoring system. This system continuously checks the state of health of the servo-hydraulic axes, from which the condition of the pump and axis valves can be derived.
New SmartPlus with high-tech automation and digitization
At this year’s K fair, Wittmann Battenfeld will present an outstanding demonstration of its digitization and automation expertise by manufacturing a spirit level on a machine from the new SmartPlus series with the new B8X control system. Special features of the servo-hydraulic SmartPlus are high levels of cost and energy efficiency and repeatability. By using proven technologies combined with carefully selected options, it has become possible to offer an excellent price/performance ratio for these machines.
On a SmartPlus 90/350 equipped with the CMS Lite conditioning monitoring system and an automation cell designed and manufactured by Wittmann Battenfeld Germany, a spirit level made of ABS is produced with a 1+1-cavity mold supplied by SOLA, Austria. As a first production step, the top and bottom parts of the spirit level housing are injection molded. The top part is then deposited and printed at a laser station. Simultaneously, the bottom part placed on a tray is fitted with vials from SOLA. Next, the top part is pressed onto the bottom part by a pre-set force. The finished parts are then transported to a testing station, where the positioning of the vials is checked by a vision system. After quality inspection, the finished spirit levels are removed and deposited on a conveyor belt by a WX138 robot from Wittmann.
Standard and micro liquid silicone processing
Silicone processing is one of Wittmann Battenfeld’s core competencies and will be demonstrated at this year’s K trade fair on two exhibits.
With a servo-hydraulic SmartPower 120/350 LIM, four different closing caps for beverage cans and bottles will be produced from liquid silicone in a single injection-molding process, using a 4-cavity mold from Nexus, Austria. The open design of the SmartPower’s injection unit enables easy integration of the LSR metering unit. Die Nexus X200 metering unit comes with a new Servomix dosing system and is connected with the machine’s B8 control system via Euromap 82.3 OPC-UA integration. In the mold, latest cold-runner technology with FLOWSET needle shut-off regulation is used. The parts are removed by a Wittmann W918 robot and packaged by a flow wrapping machine.
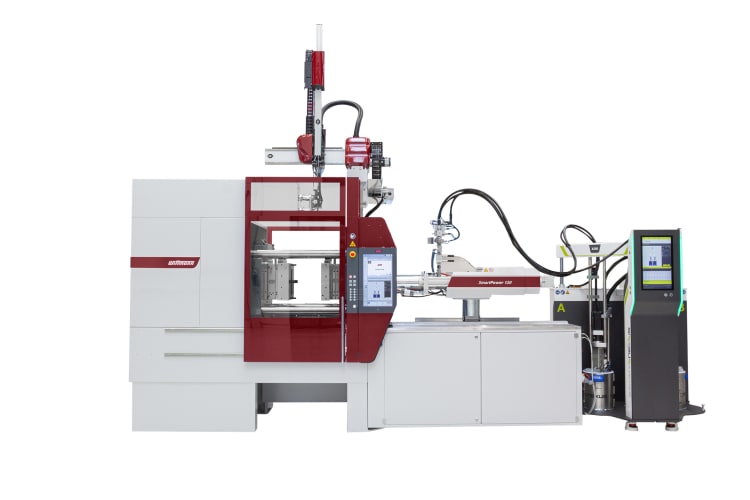
The second LSR application to be presented at the K is production of a membrane for a high-quality micro loudspeaker made of thermoplastics and liquid silicone, manufactured on a MicroPower15/10H/10H Combimould with a single-cavity mold supplied by Starlim Spritzguss GmbH, Austria. The choice of a single-cavity mold serves to demonstrate the high precision of the mold in combination with the machine, which is specially designed for the production of micro parts. It is often necessary to build costly multi-cavity molds already at the prototyping stage for the sole purpose of reaching the necessary minimum throughput of the machine. The MicroPower is equipped with a 2-step screw-and-plunger thermoplastic aggregate and a 2-step screw-and-plunger LSR aggregate. The LSR metering pump supplied by EMT Dosiertechnik, Germany, is a 1-liter cartridge system developed for extremely small metering volumes. Smooth, continuous emptying of the cartridges ensures highest precision together with consistent quality. Another advantage is the blending section reduced to a minimum, with the special benefit of rapid cleaning and minimal material loss with every material changeover.
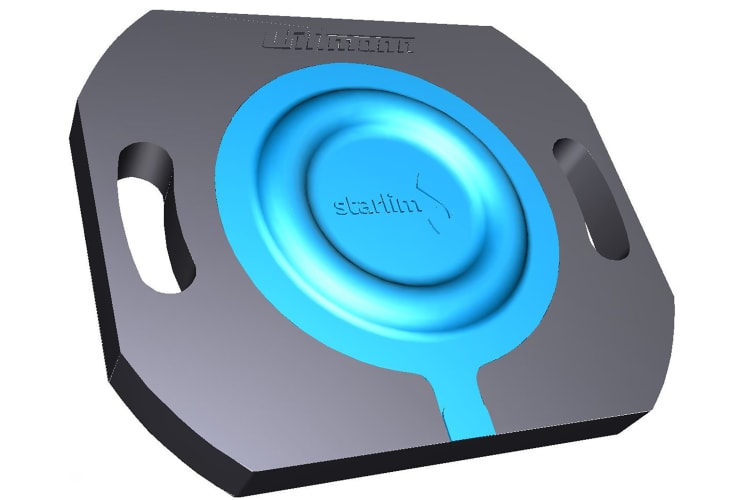