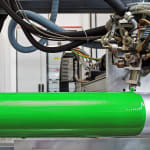
Manufacturing at lower cost than in Eastern Europe and on a competitive level with Asia - this was the target when RING Kamm und Haarschmuck GmbH, based in Bavaria, decided to relocate parts of its injection molding production back to its own facility. Wittmann accepted the challenge and supplied a highly integrated production cell grouped around a SmartPower injection molding machine with in-line recycling, able to manufacture autonomously for up to 18 hours. RING thus saves material, energy and manpower and achieves internationally competitive unit costs.
The RING brand has a long tradition. - My great-grandfather established the company in 1931 - Stephanie Renner told us during our visit in Regensburg, South Germany. Together with her mother Elfriede Renner-Weigert and her brother Walter Renner, she manages RING Kamm und Haarschmuck GmbH today, a company known primarily for its top-quality combs. - In the 1970s, there were 200 merchants selling combs in Germany - she reports from what she has been told. Today, the business is concentrated on major drugstore chains. The numbers of units per customer have increased, but so has the price pressure, too.
The grandparents already adjusted to the changing times and started to diversify the product range. Today, the portfolio includes more than 3,000 products in 3 different business segments, which are being sold in more than 30 countries worldwide.
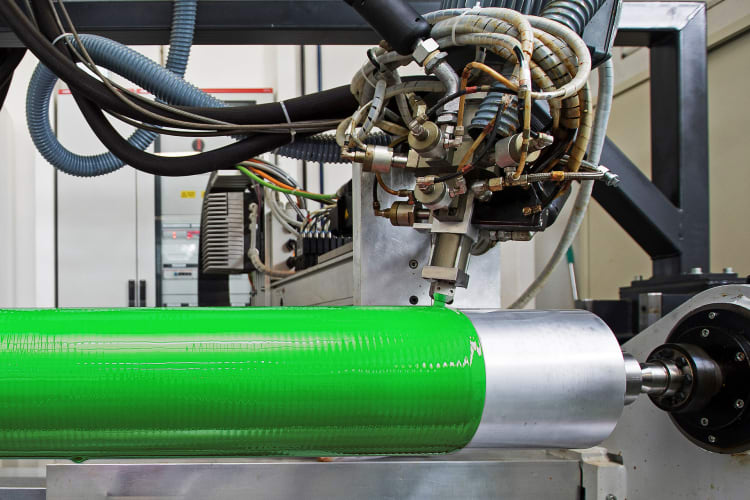
For a long time, RING manufactured all its products at its own facility. Then part of its production had to be relocated abroad, due to rising labor and production costs.
The Corona pandemic brought about another change. - We had problems with having our products delivered on time from our supplier - Renner reports. - What is more, the supplier also wanted to increase the price by up to 30 per cent because of the higher energy costs. In that case, we would have ceased to be competitive - she reportes
So, the family council decided to relocate part of the production back to the company’s own premises. At first this concerned the most important tooling for making bathroom accessories, such as tooth mugs, toothbrush boxes, soap dishes and combs, which are now being manufactured in Regensburg in large quantities for a German drugstore chain.
On the day of our visit, tooth brush boxes are running off the production line on a SmartPower injection molding machine from Wittmann. Made of polystyrene, in mother-of-pearl white, one of the current trend colors in the drugstore range.
For more than half a year now, the SmartPower has been producing around the clock, with breaks only for set-up and servicing. The production cell is designed so that it can operate autonomously for up to 18 hours.
Counselling and service made all the difference
The path was not entirely smooth between deciding to resume in-house production and actually starting up the new Wittmann production cell. - My grandfather and my father have long since passed away, and with them, we have lost much of our injection molding expertise - Elfriede Renner-Weigert remembers. - We had to start all over again to recover the know-how - Here, the family-owned company received extensive support from Wittmann.
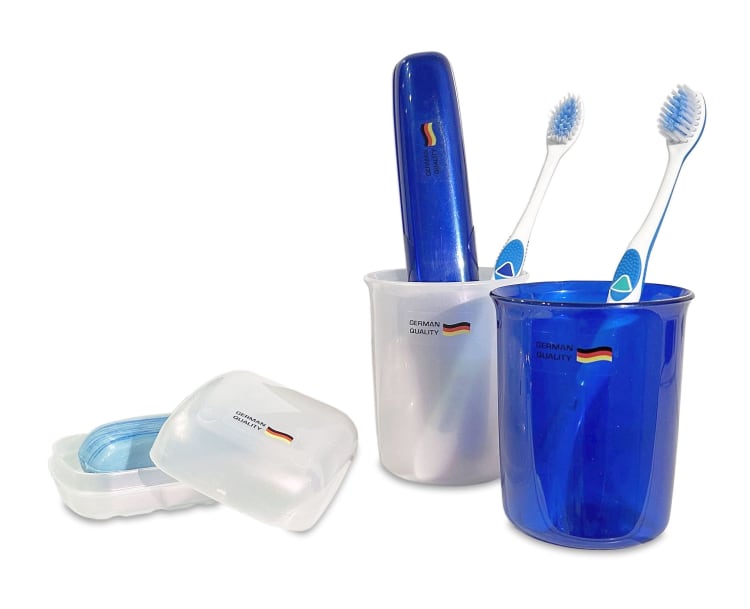
- My father knew Werner Battenfeld personally - says Renner-Weigert. - Formerly, all our injection molding machines came from Battenfeld. So, I know that these are good-quality machines - Nevertheless, enquiries were not only made to the Wittmann Group, of which Battenfeld is a part today. On the contrary, the entire market was thoroughly scrutinized and negotiations conducted with several injection molding machine manufacturers. But in the end, Wittmann won the contract, and so this tradition is also being continued at RING.
- With Wittmann, we felt from the beginning that we were very well advised - Stephanie Renner emphas. - Wittmann had the best answers to meet our requirements. For our decision to purchase, their counseling and excellent service tipped the balance in their favor - she concludes.
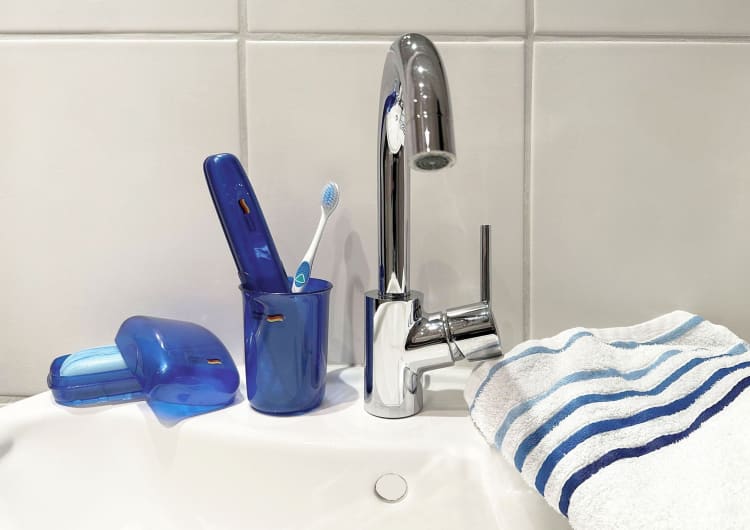