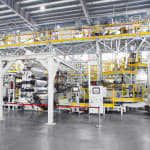
Since the company establishment, back in 1958, it has been designing and manufacturing, extruders and extrusion lines for a vast array of applications, ranging from food to the pharmaceutical packaging, medical industries, from the automotive sector to construction and agriculture, to mention a few. Its custom-engineered fully automated lines are suitable to satisfy the most stringent project specifics, in full compliance with the most prominent international standards, guaranteeing high and great quality output. An extensive technology, strong know-how and consolidated level of experience characterize our extrusion lines for the production of foils and sheets, waterproofing membranes, pipes and profiles. Tailor-made solutions with different capacity, processing several kinds of thermoplastic materials, resulting in great quality products are designed, produced and tested at our facility in Novara.
Extrusion lines for waterproofing membranes.
Thanks to advanced technical know-how, developed for the production of PVC and TPO, single or multilayer waterproofing membranes, Amut design sand provides customized plants equipped with either double or single calender. These diversified systems may reach an overall production up to 15 million sq. m. and 8 million sq. m. of high-quality membrane per year, respectively. The Single Calender is the result of the technological innovation conducted in over 40 years of experience, which led our group to be the only provider in the world. This configuration allows to produce in one single step a co-extruded 3-layer membrane, adding the inner reinforcement (polyester, polypropylene, fiberglass) and the fleeceback scrim bonding for support. The end product is a finished membrane composed of up to five materials/layers coupled in a single step, offering to end-users a completely different proposal from those currently available on the market.
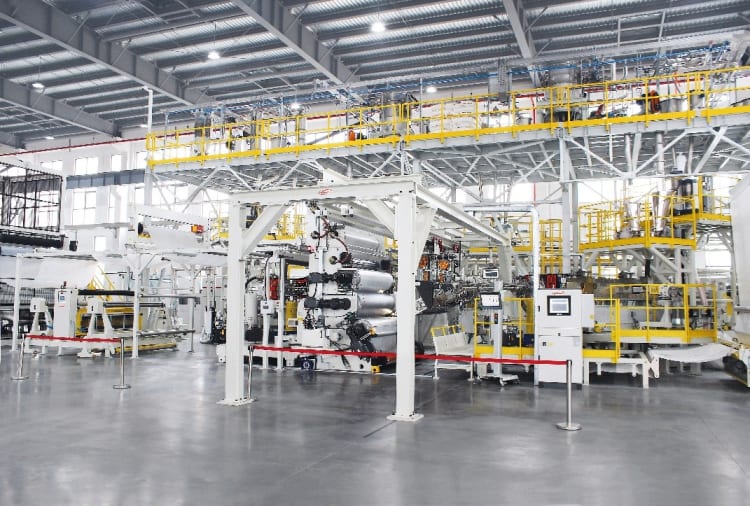
Extrusion Line for waterproofing membrane
Extrusion lines for r-PET
The Bottle to Packaging application lines are designed to process 100% post-consumer PET bottle flakes into certified food grade thermoforming foil, FDA and EFSA approved. The lines are proposed with a net width from 1,000 to 2,000 mm configuration with one layer, three layers or up to 5 layers upon request. The thickness is from 0.15 to 2 mm and the output is around 1,500 kg/h in max production.
Amut cast lines
Equipped with the ultimate PROWIND4.0 winder, unique in the world for its use of idle shafts for rolls winding thus ensuring the best finished roll quality.
The Prowind4.0 winder for stretch film, developed by our R&D team, is a purely contact winder. Winding shafts are not motorized. The synchronization of the new shaft entering the winding process is though magnetic field force avoiding any direct contact with the entering shaft during speed up process.
Among the main characteristics of the Amut latest Prowind4.0, the following should be mentioned:
- winding process through idle shafts (no motors used)
- speed synchronization of winding shaft during the change cycle is without direct contact of the motor on incoming shaft
- carton cores loading in a separate module especially designed to allow the line running even if cores are missing from the loading box
- total absence of hydraulic parts
- electronic control of contact roller pressure
- winding with two contact rollers on each turret (winding shaft) – with lowest roll tail available on the market
- constant film winding angle, with in-line adjusting
- no theoretical roll weight calculation, but real weighing of each roll during the unloading process
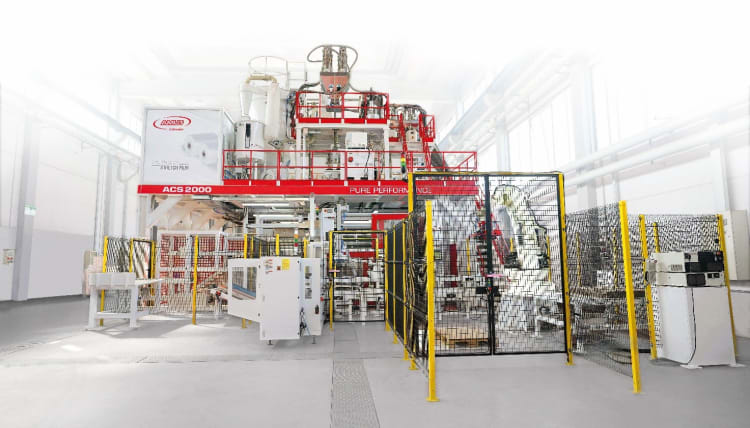
Cast line for stretch film
Amut recycling plants
Amut recycling solutions are instrumental in reducing environmental impact, through the valorization of post-consumer plastics scraps. Amut single source, integrated sorting and washing solutions, developed for a cleaner environment, are equipped with the patented De-Labeller and Friction Washer. The complete plants, ranging from a capacity of 1,250 up to 6,000 Kg./h., are designed to process PET, HDPE, PP bottles, containers and PE film. These turn-key lines suitable for the treatment of contaminated plastics, from the front-end sorting section to washing, allow to obtain high purity flakes, with reduced water consumption and energy savings. Amut modular systems guarantee, through the De-Labeller unit, the removal of all types of labels with 95% efficiency; full preservation of bottles’ necks and bodies and low operational costs.
Amut recycling technology has been provided in several state-of-the-art facilities, worldwide. Among the most recent successes is worth mentioning the Circular Plastic Australia project where its high-performance PRF and washing plants are operating at cutomer’s full satisfaction. A successful case history for which Amut got the prestigious "APPMA Sustainability Award", together with the client and local partner.
Amut is perfectly positioned to provide high-end technology to enhance sustainability.
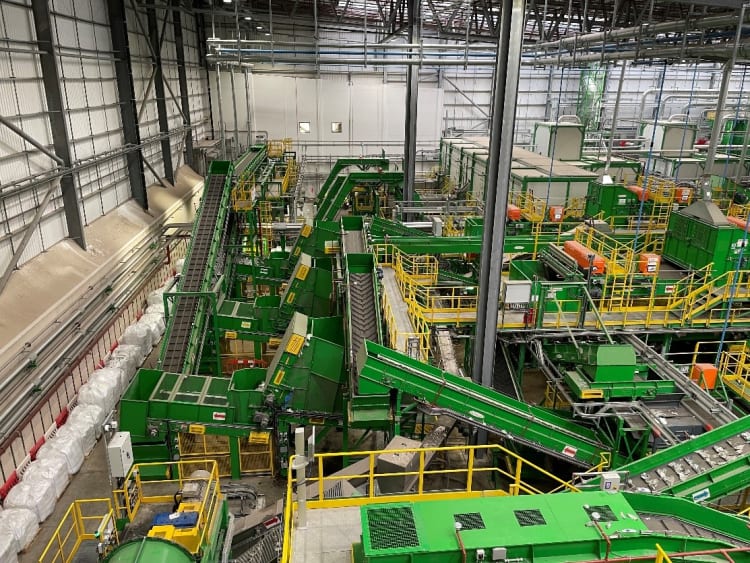
The world’s largest integrated sorting and washing plant