Standardization and traceability
The ability of AM to produce geometrically complex parts, its role as an enabler of mass customization, and the potential time and cost savings associate with its use are all important for the future of industry. However, when compared to more familiar and established manufacturing methods, AM technology is dynamic and rapidly evolving, and technology innovators are working to overcome the barriers to adoption of AM for production applications, including those related to quality control standards.
ZYGO is actively researching calibration, traceability, characterization, and verification for surface topography measurements, with 16 papers published in the last 5 years alone on these topics, and a further seven specifically focused on physical modelling of optical measurements of surface structures - including complex, steeply-sloped surfaces characteristic of AM parts - and five more papers on the measurement of AM parts per se.
ZYGO is also a partner in the €2.2M EMPIR 20IND07 TracOptic project, with the title “Traceable industrial 3D roughness and dimensional measurement using optical 3D microscopy and optical distance sensors” - of obvious value to the AM sector.
National and international standards are critical both to Industry adoption and to assuring quality control across multiple, developing manufacturing technologies. ZYGO is an active member of ISO TC213 WG16 for the development of the ISO 25178 surface texture standards, working in collaboration with international experts on the ISO 25178-603 and 25178-604 standards for interference microscopy, and the 25178-700 standard for instrument calibration and traceability. ZYGO is also a member of the ASME B46.1 working group on surface texture analysis, which currently includes a task team concentrating on AM metrology standards.
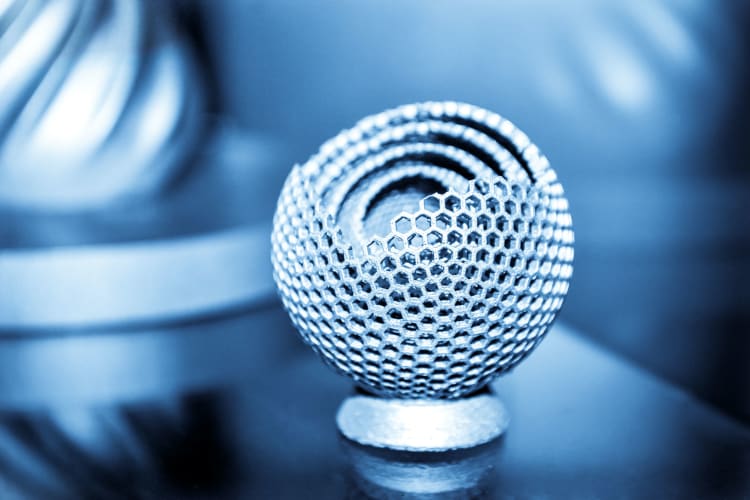
Post-process metrology
Measurements of AM parts post-process serve to validate conformance with design intent, and to provide clues into fabrication problems left by surface signatures. However, the uniqueness of AM processes and produced parts lead manufacturers to use an array of different mechanical and metrology verification techniques. They adopt an empirical approach as no one solution is trusted to provide accurate enough data. Gage R&R is used as a stand-in for a more rigorous measurement uncertainty approach. As a consequence, AM parts are often “over-tested” to improve confidence, but this means extra time and extra cost, areas that must be addressed to make AM for production more viable.
The open question is how to improve this situation for greater efficiency while maintaining confidence. The answer is for metrology solutions providers to adapt existing metrology technologies to better align them with the unique characteristics of the AM process and end-use AM parts, which are characterized by irregular, steeply sloped surface topography that many measurement technologies fail to capture.
Through extensive research and development of the foundational coherence scanning interferometry (CSI) technology in the ZYGO 3D optical profilers, high-accuracy AM metrology tools are now available to industry. Both instruments use innovative hardware and software upgrades, the package of improvements being referred to internally at ZYGO as “More Data Technology,” which makes the instruments much better suited to AM parts.
“More Data” significantly improves the baseline sensitivity of CSI and enables high-dynamic range (HDR) operation making it valuable for a wide range of parts, from steeply sloped smooth parts to exceptionally rough textures with poor reflectivity. Additionally, HDR measures parts with a wide range of reflectance, often a struggle for other instruments that use interferometry as a measurement principle. ZYGO was the first to demonstrate full-colour surface topography measurement of metal additive manufactured surfaces using interferometry, and ZYGO engineers actively use AM internally for instrument prototyping and applications development.
Peter de Groot
Peter de Groot, PhD, is Chief Scientist at Zygo Corporation, which is owned by AMETEK, Inc., a leading global manufacturer of electronic instruments and electromechanical devices with annual sales of approximately $5 billion. ZYGO designs and manufactures optical metrology instruments, high-precision optical components, and complex electro-optical systems, and Its products employ various optical phase and analysis techniques for measuring displacement, surface shape and texture, and film thickness. Electro-Optics and Optical Components businesses leverage ZYGO's expertise in optical design and assembly, and high-volume manufacturing of precision optical components and systems, for the medical/life sciences, defense and industrial markets.