
At the K trade fair in Düsseldorf from October 8 to 15, Promix Solutions will be presenting solutions for mixing, foaming and cooling for the plastics industry in Hall 9, Stand E18. The focus is on raw material savings with the Microcell Technology and real-time monitoring and process control with the Visco-P inline viscometer. The inline viscometer is now available with a closed control loop for connection to a dosing device. This enables fully controlled raw material management depending on the viscosity measured in the production process, such as for example the control of the IV value in PET processing.
In extrusion, material accounts for 80 % of the CO2 footprint. This is where Promix comes in. Microcell Technology creates a microcellular foam structure in the polymer by adding environmentally friendly atmospheric gases. This reduces the product weight by 20-50%, resulting in significant material savings. This not only reduces production costs but also protects the environment.
Promix Microcell Technology is mainly used for films, sheets, foam core pipes, profiles and cable sheathing and works for almost all polymers. In addition to saving polymer, new product properties associated with foaming, such as weight reduction, improved noise or heat insulation, better shock/impact absorption, light-diffusing optics or other visual and haptic effects, are often an additional incentive for using Promix Microcell Technology.
At K, Promix will be showcasing relevant key components and providing information on the possibilities within the specific fields of application. One promising new field of application is the foaming of monofilaments. Promix is currently developing foamed monofilaments for artificial grass together with an industrial partner.
Microcell technology is available for both, newly planned extrusion lines and as a retrofit solution for existing lines. To date, more than 350 industrial references are on the market and various machine manufacturers are successfully integrating the technology into their lines.
Updated graphical user interface and optimized foam additives
The gas dosing system, the heart of the physical foaming process, has been equipped with a modernized graphical user interface for even easier operation. In addition, an improved grade of Procell nucleation additives is available, ensuring even finer cell structures. In higher dosages, it also acts as a foaming additive. This can be helpful in extrusion lines with very low throughputs or for preliminary testing, since additive foaming does not require any changes to the extrusion line. The experts at Promix will be happy to advise you.
Monitor and control raw material quality and process conditions in real time
The increasing use of recyclates and raw materials from different sources makes it more and more difficult to keep extrusion processes under control. The inline viscometer "Visco-P" measures the actual viscosity under processing conditions and in real time directly in the melt stream, without any bypass or loss of material. The maintenance-free measuring module, which is tailored to the application, homogenizes the melt without the risk of clogging, deposits or decomposition. The Visco-P is therefore ideal for recyclates as well as filled and shear-sensitive materials.
At the K trade fair, Promix will be demonstrating how Visco-P can be used to measure and control the IV value during PET extrusion. The system has a closed control loop into which a dosing device can be integrated As soon as the IV value measured in the production process falls below the target value, the software triggers the dosing of an IV enhancer until the quality of the melt has reached the desired level again. The same logic is possible in PP recycling by dosing respective chain extenders.
Trend evaluations and reporting tools enable the measurement results to be recorded with statistical analysis. User-selectable limit values for the viscosity trigger an alarm and show the operator current deviations from the target value. This means that corrective measures can be taken immediately, even without a control loop.
The Visco-P inline viscometer is compatible with all common extruder types and almost all polymers and can be retrofitted to existing systems. All common interfaces are optionally available to flexibly network the new products with Industry 4.0 platforms.
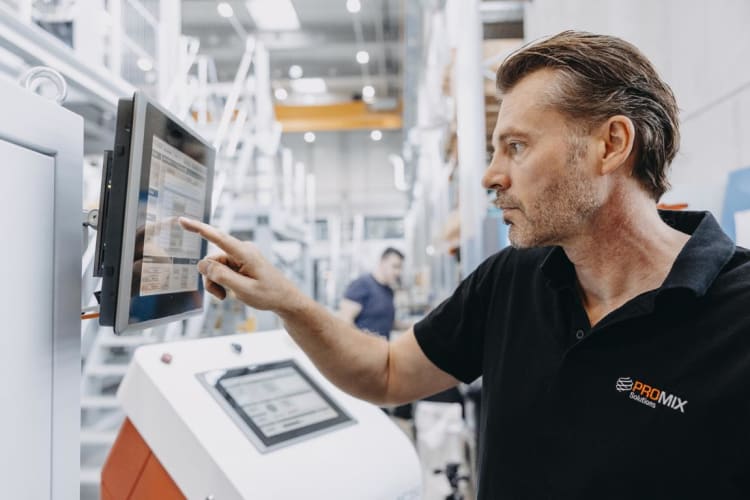
New CEO and new hall with 1600 m2of additional space
Dr. Krischan Jeltsch joined Promix in April 2024 and takes over the position of CEO from Rolf Heusser, who is gradually withdrawing from the operational business and focusing on the management of the Supervisory Board. Krischan Jeltsch previously worked as Head of Business Development & Marketing at Buss AG after many years in the chemical industry at BASF and Dow Chemical in technical and management roles. With his profound technical and commercial background and experiences with innovation & digitalization projects, he brings the necessary know-how to successfully lead Promix into the future. Krischan Jeltsch will be present at K from October 12 to 15 and looks forward to meeting personally.
Another milestone for the company is the completion of a new hall with office wing in Wetzlar, Germany. The new building will be occupied from the end of June '25 and will consolidate manufacturing, assembly, engineering, order processing and logistics on 1600 m2of floor space.
Promix Solutions AG, Hall A9, Stand E18