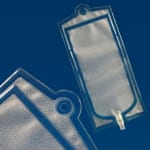
An innovation in radio frequency (RF) plastics welding now enables manufacturers of medical bags and pouches to obtain the clarity, elasticity, and performance advantages of Medalist medical elastomers while providing a safe and fully compliant alternative to PVC, thermoplastic polyurethane (TPU), or natural rubber latex.
Teknor Apex Company and Genesis Plastics Welding are jointly announcing this breakthrough at MD&M East, where ecoGenesis RF plastics welded samples of fluid drainage and storage bags from Medalist-based film are on display at the exhibits of Genesis and Teknor Apex.
While conventional RF plastics welding works well with such polymers as PVC and TPU, low dielectric loss materials such as Medalist elastomers from Teknor Apex have until now not been bondable with this process. The ecoGenesis RF plastics welding technology developed by Genesis enables film produced from a Medalist elastomer to form strong permanent bonds with itself as well as with polypropylene and similar polymers.
And while the alternative technique of heat sealing produces only a straight-line bond, the sample bags shown at MD&M East exhibit the ability to weld complex patterns in one sequence, displaying the wide range of design possibilities available for Medalist elastomers with ecoGenesis RF plastics welding technology.
This new capability for joining and assembly makes available to manufacturers of medical fluid delivery, storage, and drainage bags several important advantages over widely used PVC. Besides being free of halogens and phthalates, Medalist elastomers are available at lower hardness ranges, provide a broader processing window, exhibit greater elasticity and superior low-temperature flexibility, have a wider range of service temperatures, and save weight because of their lower density. Like PVC, Medalist elastomers are available in fully transparent grades.
“ecoGenesis RF plastics welding is the latest addition to a rapidly expanding portfolio of methods for fabricating medical devices with components made from Medalist elastomers,” said Elliott Pritikin, new business development specialist for Teknor Apex’s Thermoplastic Elastomer Division. “High-purity Medalist compounds can be sealed or bonded using standard techniques, including adhesive bonding, vibration welding, heat-sealing—and now RF welding.”
The availability of RF plastics welding capability for Medalist elastomers gives greater scope for designers and processors of medical bags and pouches, noted Tom Ryder, president and CEO of Genesis Plastics Welding. “In making it possible to RF-weld Medalist elastomers, the proprietary ecoGenesis technology opens the door to lower manufacturing costs, elimination of heat-seal additives, and the possibility of reducing raw-material costs. In addition, RF plastics welding yields dependable, clean-looking seals—even in intricately shaped patterns.”
Genesis provides companies using Medalist elastomers with two options: to use the welding services of the company as a contract manufacturer employing a regulation-compliant clean room at its facility in Indiana, U.S.A.; or to license the ecoGenesis technology for use on their own standard RF welding equipment.