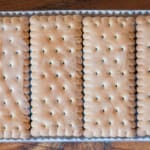
Bioplastics are already part of our everyday life. Driven by high consumer demand and market innovations in advanced technical properties and functionalities, companies have already taken some major steps towards the transformation to a bio-based and circular economy. The goal is to decrease environmental impact concerns by decoupling packaging material from fossil resources, changing consumption patterns and reimagining packaging designs.
Flexible multilayer plastic packaging design remains a major challenge, as most conventional multilayer films are neither recyclable nor compostable. As of today there is a lack of recyclability for this kind of packaging that still makes up over 75 % of the food industry usage.
Understanding this gap in the market, four key players in the bioplastics industry have joined together to find a solution. Eurotech Extrusion Machinery, NatureWorks, Nippon Gohsei and Sukano have now successfully processed a multilayer transparent bio-based barrier film.
Ingeo resin processed into a film is already used in many types of flexible packaging. Using Ingeo provides for a reduced carbon footprint, as well as compostability as an end of life option. For higher gas barrier requirements, a coating or a metallization surface treatment of the film is typically required. However, the need for this coating or metallization can be eliminated through the use of a barrier polymer to produce a coextruded structure. This provides an additional, new option for packing foods which require an extended shelf life, while still offering clarity and compostability.
The coex film processed at Eurotech used a K5A 5 layer blown film lab machine in a configuration using 2 extruders 25 mm., and 3 extruders 20 mm., including the die lip of 100 mm. diameter and 1.4 mm gap.
The total film thicknesses of 45 microns, 280 mm width, contains Ingeo PLA 4043D from NatureWorks and is used in the inner A layer, with an outer bubble layer E including Sukano masterbatches processing aids. These PLA-based Sukano masterbatches were specifically designed for this application. The tie layers use BTR8002P and the barrier layer uses G-polymer both from Nippon Gohsei. This combination of formulation and process conditions yielded a stable bubble, excellent film transparency, and good roll quality.
Testing showed that the use of Sukano masterbatches offered increased melt strength, and therefore better processability, good transparency and better adhesion during sealing. Mechanical properties were also maintained. As an additional benefit each material used in the film has either been tested and certified or assessed to be biodegradable and industrially compostable according to European norm EN 13432. Less film sticking was managed via the use of slip agent bio-based masterbatches, which increased the processing window and ensured good processability conditions and a lower COF, therefore conferring better film properties for secondary fabrication steps.