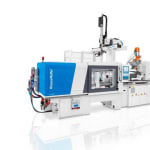
The all-electric, made-to-measure machine
Through its new PX series, KraussMaffei sets new standards in all-electric injection molding machines. The new PX series combines the advantages of an all-electric injection molding machine with maximum modularity in an unprecedented way. "The success of the PX series introduced at K 2016 proves us right. Our customers appreciate the great variety and flexibility, not only in the configuration of the right machine - for example through a wide selection of clamping unit and injection unit combinations - but also in production or retrofitting," says Dr. Hans Ulrich Golz, President of the Injection Molding Machinery segment of the KraussMaffei Group and member of the KraussMaffei Managing Board. "The demand is enormous, especially from customers located in Germany, but also from those in the USA and China," adds Golz. In order to meet the high demand, KraussMaffei wants to double the production capacity of the PX series in the coming year.Selected exhibits at Fakuma will demonstrate the unparalleled combination of the highest precision and maximum flexibility with an all-electric injection molding machine.
PX 50-180 SilcoSet: Flawless Fresnel lenses made from silicone
The manufacturing of transparent diffusion lenses, called Fresnel lenses and made from silicone material, is extremely challenging. Since silicone or LSR (liquid silicone rubber) is of extremely low viscosity, particularly highly transparent silicone, it requires an especially high precision during injection. Thanks to the superfine molding accuracy, the facet profile is of such high resolution that no structures are visible on the lens. The lenses are virtually flawless. "In the case of this application, the modular concept of the new PX series from KraussMaffei particularly distinguishes itself. At Fakuma, the PX 50-180 SilcoSet will combine hydraulic nozzle contact force with an electric injection unit in an unparalleled way. The result is extremely high precision. The machine-to-mold connection is tight, the production is leakage-free," explains Jochen Mitzler, Head of Strategic Product Management at KraussMaffei. Special screw seals on the shaft support this argument. Additionally, the spring-loaded return-flow lock of the screw guarantees secure closing behavior during processing of low-viscosity material.The APC plus function from KraussMaffei assumes a special task with this application. It compensates for the batch fluctuations commonly encountered in LSR processing. As the process progresses, APC plus monitors the viscosity of the material and corrects the filling volume even in the shot. "The process as a whole is made even more precise, while the part weight remains constant. The APC plus is even able to reliably compensate for any potential preliminary cross-linking of the silicone," says Mitzler.
The compact design of the PX 50 provides lots of space for demolding and peripherals, as well as excellent accessibility. For example, an integrated industrial robot demolds the lenses. In the next step, visual quality control is performed with regard to quality of magnification and flashing before the finished lenses are stored in magazines.