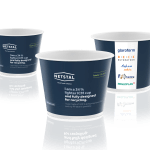
At Fakuma, Netstal (Hall B3, Booth 3119) will be producing thin-wall packaging optimized for the circular economy using the injection compression molding process. Another highlight is the new Axos 9 control generation.
It's light as a feather, the yogurt cup that Netstal is presenting at Fakuma. The other key data: Filling volume 200 g, part weight 5.4 g, wall thickness 0.3 mm. Since the cup and label are made of 100 % polypropylene (PP), the packaging is particularly easy to recycle. Unlike a conventional in-mold label, the label comes off in the mechanical recycling process. The PP stream is not affected because printing ink particles are reliably separated from the pure PP. Injection Compression Molding (ICM) reduces the weight of the cup by a remarkable 34 %. Another improvement in terms of sustainability: the combination of the ICM process and product optimization also results in a 27 % reduction in packaging volume.
Sustainable cup, energy-efficiently produced
The sustainable thin-wall packaging for dairy products is produced in 4 cavities at a cycle time of 2.7 seconds in an Elion 1750 with hybrid injection unit. The Netstal machine operates with reliable performance and leading energy efficiency. With the optionally available adaptive system pressure reduction, Netstal has been able to further optimize the efficiency of its hybrid machines. In automatic mode, the control system determines the optimum point at any time and adjusts the pressure in the hydraulic system accordingly. Depending on the application, the energy consumption for providing the required system pressure drops to a minimum.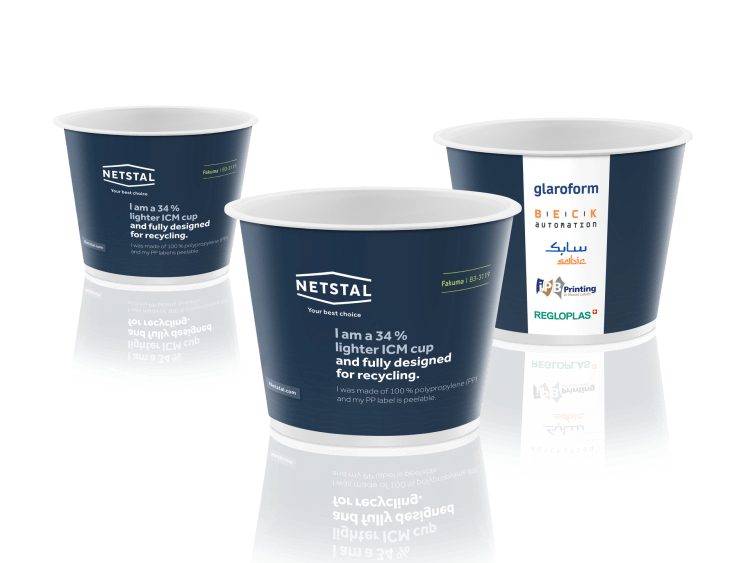
34% lighter: the cup produced using the injection compression molding process weighs only 5.4 g
The packaging application, optimized for recycling, was developed in collaboration with high-end system partners Glaroform, Beck Automation, SABIC, IPB Printing, motan, Regloplas and Uniform Color. The development partner from the food industry is Emmi AG, the largest bottler of dairy products. The specifications of the packaging were optimized with and under the guidance of Emmi's requirements. In the process, the previous appearance of the cup was to be retained.
Operate the machine intuitively with the new Axos control system
With Axos 9, Netstal is bringing the latest generation of its control technology to the Elion and Elios series machines. Thanks to the innovative operating concept, users get the maximum performance out of their Netstal machine. Thanks to the integration of Smart Operation, employees in the production environment operate the machines quickly, safely, and effectively. The feature was previously available as a paid option and is included in the scope of delivery from Axos 9.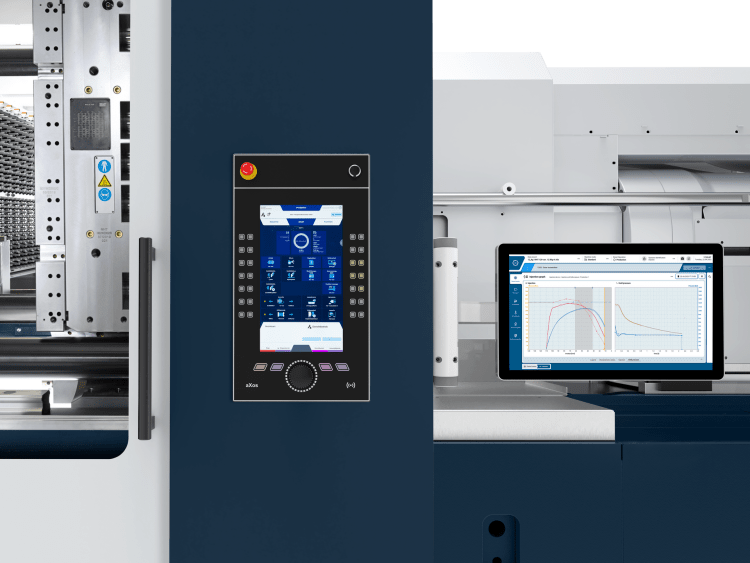
Intuitive control: The new Axos control is equipped as standard with Smart Operation