A complete work step saved
The injection molding process dictates the timing for printing on finished parts. The printing process must be fully completed within the cycle time. This is why the only feasible option was a direct print requiring neither pretreatment nor a long drying time. The print must not be blurred when the gripper picks up the parts again immediately after printing.
Wittmann evaluated many different printing methods, colorants and suppliers. Pad printing was ruled out due to the required pretreatment, and many colorants did not pass the stringent durability tests. Wipe and abrasion tests were carried out with various solvents. For later on, when used inside the sprayers, the piston pressure gages can be exposed to aggressive media such as pesticides or detergents.
The final choice was an ink jet printer from Videojet, which not only delivered the best result in colorant durability, but also in terms of flexibility. “We are now able to print out very fine variations in the position of the scale”, says Sellmayr.
The trend towards process integration is on the increase - a trend that Wittmann also observes among other injection molders. The aim in each case is optimal utilization of each system component’s capacities. Especially robots often have free capacity for handling additional tasks during the injection and cooling process, such as printing on finished parts as done at Mesto.
“The more tasks the robot can take over inside the injection molding cell, the less labor input we have in the assembly”, says Élise Sellmayr. “The piston manometers leave the injection molding cell ready for mounting. By integrating the printer, we save a complete work step.” And that saves a lot of logistic expense, too, since the piston manometers were previously produced on stock first, and then printed later on.
Power consumption reduced by a third
SmartPower injection molding machines dominate the scene on Mesto’s production floor. Ever since the company started a comprehensive project in 2017 to increase its energy efficiency, old injection molding machines are being consistently replaced by servo-hydraulic SmartPower models. The high energy efficiency of the Wittmann machines tipped the balance. “With the changeover, we immediately saw some first savings”, Élise Sellmayr reports. “Up to now, we have been able to reduce our power consumption by a third with the same number of machines.”
A further benefit: focusing on just one brand of machinery makes daily work easier for machine setters and operators. “They all get along very well with the Wittmann control system”, says Sellmayr.
On our company tour, we have now arrived next to a SmartPower 180 injection molding machine. Pressure vessel tops are running off the conveyor belt, flat black discs with piston rods protruding from their centers. In a 2-cavity mold, the container lids are molded directly onto the piston rods. The material processed is a fiberglass-reinforced polypropylene.
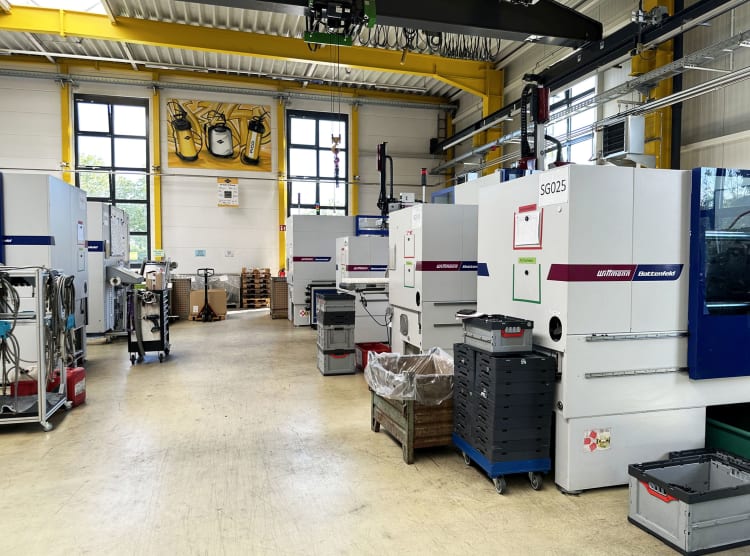
An extremely compact arrangement of all components also catches the eye in this production cell. And here too, flexibility is an important issue. In this system, Wittmann has integrated the feeding device for the metal rods to be insert-molded into the overall concept. The challenge for this system was to process various types of piston rods for different sprayer models, which were all to be fed in through the same magazine.
The piston rods come in varying lengths and diameters. There are rotationally symmetric rods and rod bars with wings and threaded sides, which must all be inserted precisely in a certain position. The material of the rods and consequently their magnetic behavior also varies.
All of these aspects had to be considered in planning the gripper concept. The task was further complicated by the fact that insertion of the metal rods and removal of the finished parts had to take place from the same side of the mold. Accordingly, all of the gripper’s functions had to be united on only one side, and that very compactly, so that it could still operate safely inside the open mold.
In all considerations concerning the gripper layout, the and complexity of the resulting gripper and its efficiency in production were weighed against each other. In this way, all requirements could be accommodated on two grippers, with a fully automatic gripper changeover.
The ultimate goal in all projects is: “no overengineering!” For this would counteract efficiency, flexibility and easy operation. “In every new project, I let people show me what is possible and what new ideas are available”, Élise Sellmayr emphas. “Then we make up our minds about which innovation level makes sense. At the end of the day, these are all customized special machines that are only built once each. Precisely that makes it so exciting. “