Equipped with state-of-the-art technology Tomra’s metal sorting systems recover recyclable metals from mixed metal streams and enable plant operators to create the purest material fractions, such as furnace-ready aluminum. As the industry strives for sustainable production and a reduction of CO2 emissions, the global demand for recycled metals continues to surge and so does the need for accurate material recovery and processing. “We have a long legacy in the metal industry but given current market trends and our customer’s requirements we will concentrate even more on this area in the future. With our expanded test capacities and the most advanced technology, we are well-equipped to support the industry in processing higher volumes and reaching the required qualities”, explains Radice.
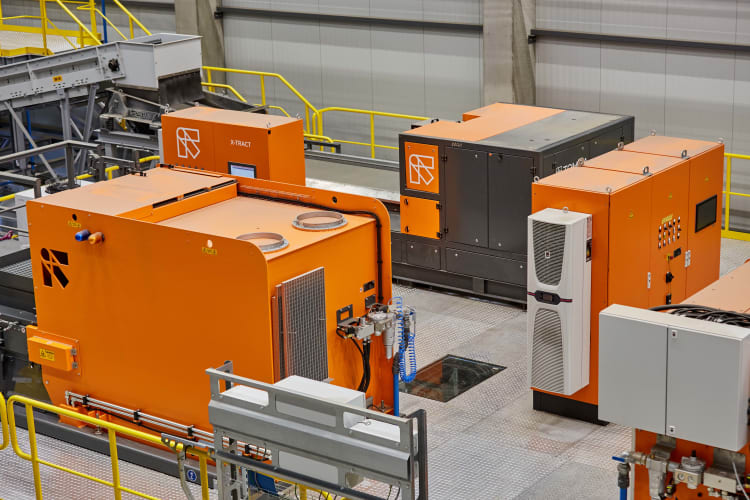
Tomra’s X-Tract and Combisense in new Test Center
While the new facility allows the company to place a stronger emphasis on the metals segment, waste applications continue to play an equally important role. The original test center started as a mobile test station in Andernach, Germany, moved to Mülheim-Kärlich in 2009, and steadily grew in sophistication. Today, it offers 1.500 m2 for waste sorting trials. The test possibilities range from the recovery of recyclable polymers from mixed and source-separated waste streams, to flake sorting, the separation of wood by material type, and many more.
Also, deep learning technologies, as a subset of AI, are part of Tomra’s product portfolio and can be tested in different sorting tasks. Available as a complementary solution to its core technologies, deep learning is a future-forward tool that helps improve sorting performance by detecting previously hard or impossible-to-detect materials. Summarizing the advantages of the new test center setup, Ralph Uepping stresses: “All our products are installed and can be tested in a complete circuit. Together with our expert teams, we can simulate the entire sorting process with eddy currents, magnets, screens and a ballistic separator. This allows us to demonstrate the importance of material pre-treatment and define processes that are stable and economically viable even with changing input streams.”
The rationale behind the expansion was extensively explained during the three-day conference that took place both at Tomra’s German headquarters as well as in a hotel nearby to combine theory and practice. On the first conference day, participants listened to numerous presentations to learn more about Tomra’s strategy, new ventures, its digital offerings including deep learning, as well as its approach to customer service. On the second day, it got more practical on-site. After a presentation held by Tom Eng, SVP and Head of Tomra Recycling Sorting, to explain the evolution of the site in Mülheim-Kärlich, the management team guided the participants to the new facility to cut the ribbon an declare the new building opened. Divided into different groups, the conference attendees were guided through the plant and saw live demonstrations for numerous applications. The tour was rounded off by presentations that emphad how TOMRA and its technology support maximizing resource circularity in the plastic, metal and wood industries.
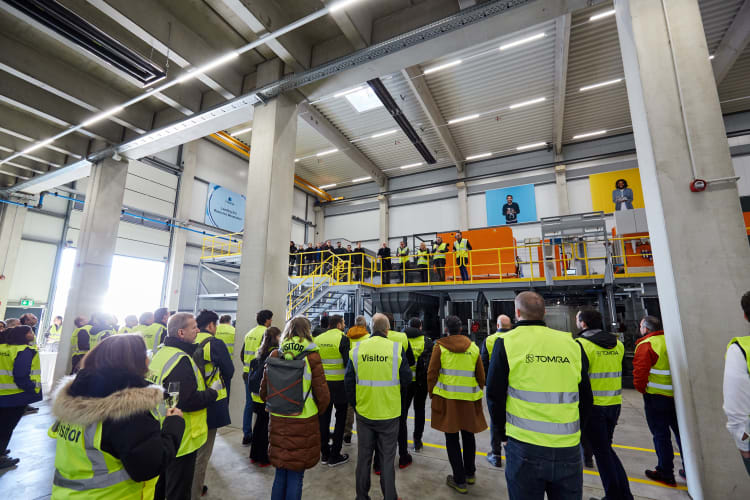
Opening words in new Test Center.
The opening of a new trial hall as well as the conference set the stage for Tomra’s growth ambition, its commitment toward stakeholders and its mission to enable a world without waste. Customers and partners are invited to take the opportunity to work with Tomra’s experts to specify the most suitable sorting solution for their requirements.