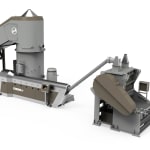
K 2025 sees EREMA launch the Agglorema generation of machines, a new recycling system specially developed for processing heavily contaminated post-consumer waste. The machine processes film rejects with high levels of fluctuating moisture from sorting systems on a large scale to produce agglomerates with a high bulk density that are an ideal feedstock for chemical recycling, among other applications.
"It is our job to build machines that support chemical recyclers in the recovery of low-grade waste fractions," explains Klaus Lederer, Business Development Manager Chemical Recycling at EREMA. Many chemical recycling plants require standardised, pourable input material. "Agglorema closes the gap between highly contaminated, heterogeneous and often thin-film waste streams, and reliable feedstock for the reactor. This is a particularly robust and energy-efficient system," says Klaus Lederer. This series of machines complements the company's product portfolio for chemical recycling and aligns perfectly with the Chemarema.
High throughput with a high tolerance to contamination
Agglorema processes heavily contaminated waste streams with a low bulk density (from 30 kg/m³) and moisture contents of up to 12 per cent. This is made possible by combining the EREMA Preconditioning Unit (PCU) with patented Counter Current technology and a specially designed extruder screw. Even when the composition of the feed material varies greatly, for example in terms of polymer, geometry and moisture, this combination ensures stable process control. The material is homogenised, degassed, preheated, and continuously fed into a short extruder without upstream drying. "Conventional agglomeration systems quickly reach their limits if the feed material has a low bulk density or fluctuating parameters. This is not a problem for Agglorema, however, thanks to the advantages of the PCU and the robust design of the system," says Klaus Lederer. He sees a particular advantage in the scalability of the EREMA system. It handles up to 2.3 tonnes per hour, with ample headroom to increase throughput.
From the extruder, the partially melted material strand is fed directly through a melt pipe into the water-cooled melt mill. Here, it is formed into agglomerates with bulk densities of 280 to 380 kg/m³ and a defined particle . Depending on the configuration, downstream drying can reduce the residual moisture up to less than one percent. The process layout is deliberately kept straightforward and robust. The system capitalises on the advantages of extrusion, but significantly reduces process temperature and energy consumption. "Our specially designed extrusion technology only inputs as much energy as the material requires," explains Klaus Lederer.
The Agglorema can be used to prepare feedstock materials for chemical recycling as well as for mechanical recycling. Agglomerates produced from mixed polyolefin fractions can be used in the manufacture of simple components, for example.
Chemarema feeds melt directly into the reactor
In addition to the new Agglorema system, EREMA also offers the Chemarema series, a solution for chemical recycling in which the melt is fed directly into the reactor. In recent months, the company has started up several Chemarema machines with throughputs of between 2 and 3.5 tonnes per hour. EREMA offers these systems with a throughput of up to 4.5 tonnes per hour.
In order to withstand the high abrasiveness of the contaminated input material over the long term, Chemarema systems feature a design that is significantly more robust. "The specifications for wear resistance and temperature resilience are increasing," says Klaus Lederer. "We are working on new materials and extruder screw concepts that can handle these challenges even better. More specific information on this will be presented at the K trade fair in October."
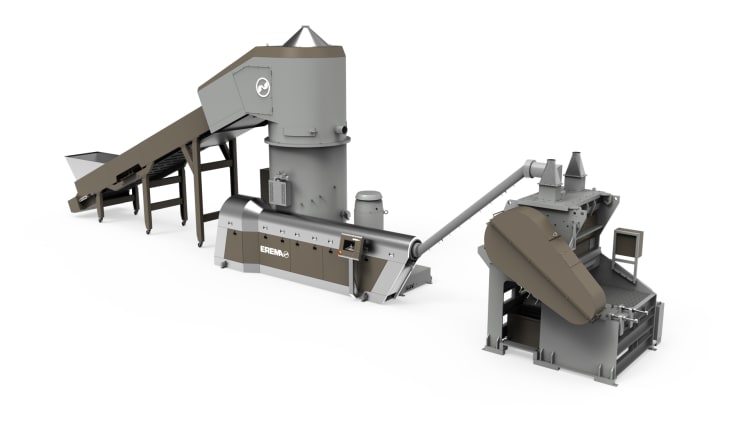
Edvanced Recycling powered by EREMA
The current campaign Edvanced Recycling - EREMA Prime Solutions for Advanced Recycling sees EREMA present a wide range of advanced plastics recycling solutions. More than 40 years of experience, combined with practical application expertise, are the basis for EREMA systems consistently delivering high-quality recycled pellets to meet precise quality specifications, from food and cosmetic grade to more straightforward applications. Edvanced Recycling shows how EREMA is working together with its customers to sustainably increase the proportion of recycled materials used to make new plastic products. All the information is available online at edvanced.erema.com
Find out more and visit EREMA at K 2025: Hall 9, Stand: C09 and at the Edvanced Recycling Centre: Outdoor area, CE03