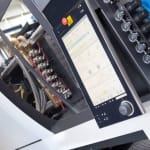
inject 4.0 is ENGEL's answer to the challenges of the fourth industrial revolution. The goal is the smart factory in which production processes continuously self-optimise through the networking of production systems, the systematic use of machine, process and production data, and the utilization of decentralised, intelligent assistance systems. During the three days of the trade fair, ENGEL will demonstrate how plastics processors can increase the productivity and quality of their production and respond flexibly to ever more rapidly changing requirements with the production of inject 4.0 logos on an all-electric and tie-bar-less ENGEL e motion 170/80 TL injection moulding machine.
Self-optimising injection moulding process
The CC300 control is capable of simulating process fluctuations; the automatic readjustments by the intelligent assistance systems can then be tracked on the display of the machine. Three assistance systems from the inject 4.0 programme of ENGEL will be used. While iQ weight control maintains consistent injected melt volume throughout the entire injection moulding process, iQ clamp control monitors the mould breathing in order to calculate and automatically adjust the optimal clamping force. Thirdly, iQ flow control will connect the injection moulding machine, which is equipped with the e-flomo electronic temperature control water distributor, to the temperature control unit, enabling the pump speed to automatically adjust to the actual requirement. This results in higher energy efficiency. ENGEL, together with its partner HB-Therm, has developed a new line of temperature control units called e-temp. The machine is connected via OPC UA, thus pointing the way for further applications. Together with its market partners, ENGEL is actively committed to establishing OPC UA as the standard for communication models in injection moulding applications. OPC UA enables platform-independent, high-performance, and above all secures communication, both within the shop-floor level and with higher level control systems such as MES and ERP.The assistance systems from ENGEL's inject 4.0 programme that are integrated into the CC300 of the injection moulding machine ensure that process fluctuations are adjusted before rejects occur