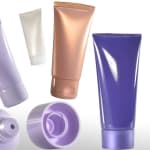
It combines a well-balanced set of mechanical properties with ease of processing and consistent quality. It can be typically used for tubes for cosmetics, toothpastes, food pastes, and household and industrial products.
For tube manufacturers, the high consistency of SABIC HDPE F4520 is important, as this helps to ensure optimum aesthetics when it comes to decoration and printing. SABIC believes it will enhance chances of approval of the new grade at our customers. “Even very small imperfections in the polymer could show up on the printed surface,” says Shyam Parameswaran, Technical Marketing Engineer at SABIC. “We have a stringent internal gel count control in place to ensure material quality.”
Tubes extruded in the new material are very flexible, making it easier for users to squeeze out the contents. In addition, the tubes can be squeezed repeatedly without puncturing – an important advantage over aluminium. SABIC HDPE F4520 also has very good resistance to stress cracking. Furthermore, tubes and necks can be welded together easily, thus optimizing production.
Very strong optical properties, gloss and transparency, providing good contact clarity when required are the main characteristics of SABIC HDPE F4520. It is easy to process and can be used in monolayer tubes, in coextrusions and laminates. It can also be blended with other polyethylenes with the same melt flow range and is already approved at several major tube manufacturers.
“We are operating in a market where the quality of the primary packaging plays a very important role,” says Hubert Polak, Purchasing Director Tubes at Albéa. “Using SABIC HDPE F4520, with its excellent aesthetics and squeezability, makes a lot of sense for us, and we expect it to quickly have a positive effect on our bottom line.”
“We expect SABIC HDPE F4520 to make important inroads into the European market for collapsible tubes, which currently numbers around 10 billion units per year,” says Patrick van der Meer, SABIC Technical Marketing Engineer. “At present, just over half of these are in plastics. The total market is increasing above GDP growth levels, and the share of plastics in that market is also increasing.”
SABIC has a complete portfolio of polyolefins for flexible tubes, with grades for injection moulded shoulders and caps as well as for extruded bodies. Mono-material solutions have obvious advantages for post-consumer recycling. In addition, SABIC has a comprehensive range of low and linear low density polyethylenes, and polypropylenes, for the tubes market.
Van der Meer concludes: “We have a long-term commitment to this important market. SABIC will continue to develop new and innovative products for it in close cooperation with our customers.”