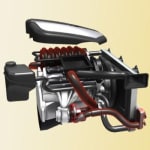
High oil prices, increasing environmental awareness and changing political conditions are more and more focusing attention on the energy efficiency of automobiles. Lightweight construction, and thus the use of plastics as a substitute for metal, plays a key role in this regard.
However, in the face of increasingly challenging demands, it is becoming ever more difficult to replace metal with polymeric materials, especially in the hot area near the engine: High-performance plastics are frequently ruled out because of the system costs. On the other hand, the performance capability of the remaining plastics no longer satisfies today’s requirements.
With the new polyamide (PA) specialty grade Ultramid Endure, researchers at BASF have now succeeded in finding a way out of the dead end. The material is a glass-fiber-reinforced polyamide that combines outstanding resistance to heat aging with the good processability of PA 66.
Compared to the standard PA 66 grade Ultramid A3WG7, the processability has been improved notably as well. Thanks to this combination of characteristics, it is now possible to produce, at justifiable system costs, under-the-hood components that are exposed to very hot air and in this way contribute to a significant weight reduction.
The new Ultramid Endure easily withstands continuous use at temperatures up to 220 as well as spikes up to 240 degrees Celsius. This extends the field of application of polyamides into the high-temperature realm. For comparison, Ultramid A3WG7 with the same glass-fiber content has a long-term service temperature of 170 degrees Celsius, while products in the heat-resistant Ultramid W2 line (PA 66/6) such as Ultramid A3W2G6 can withstand 190 degrees Celsius in continuous use.
This enormous improvement in resistance to heat aging is achieved through innovative stabilization technology development by BASF. Formation of a protective surface layer even at temperatures up to 220 degrees Celsius provides continuous protection against attack by oxygen.
The effect of this technology can be seen especially well on aged surfaces. In conventional PA 66, oxygen has eroded channels in the surface after 1000 hours at 220 degrees Celsius, allowing ever more oxygen to reach and attack ever deeper layers. In Ultramid Endure, the surface is sealed off very quickly by the new stabilization and sealing process, so that the material remains protected – except for a thin layer of carbon black on the surface – even after four months at 220 degrees Celsius.
Under-the-hood components are frequently bonded together by means of welding. As a result of the lower glass-fiber content, the weld line can create a weak spot, especially after aging. The new stabilization mechanism not only protects the polymer itself, but also strengthens this potentially weak spot. Weld lines also withstand continuous use at elevated temperatures very well. No cracking at the joint is evident even after 1000 hours at 220 degrees Celsius. Weld line strength remains high as well.